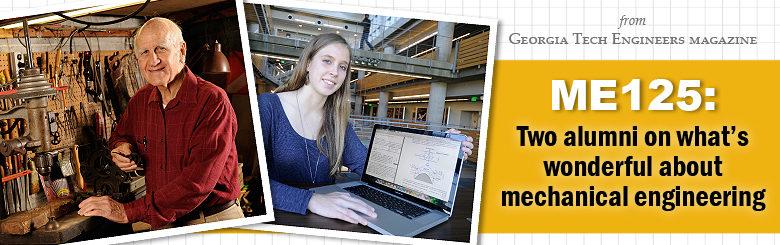
Ed. note: This story appears in the second issue of Georgia Tech Engineers, the magazine from the College of Engineering. To request a copy, please email the editor at editor@coe.gatech.edu
Interviews by Michael Baxter
Photos by Gary Meek
They are mechanical engineers, but they could not be more different.
John Cerny (B.S. ME ’51) is 83, retired. Katherine Polhemus (B.S. ME ’13) is 60 years younger and a Georgia Tech graduate student set to embark on a promising career. John hails from a tiny town on Florida’s Gulf Coast; Katherine was raised in the bedroom community of Roswell, Ga. He finished Tech before women were admitted. Her everyday tool, a laptop computer, is one that never graced his office.
Her work in simulations and computer modeling concentrates on what could happen. His work focused on what did happen – he co-owned a firm that investigated engineering mishaps and malfunctions.
But John and Katherine do share one thing in common: Both decided to become mechanical engineers because the discipline’s vast variety appealed to their intellectual curiosity.
As Georgia Tech’s Woodruff School of Mechanical Engineering marks its quasquicentennial year – that’s a century and a quarter for those keeping count – the insights of these two mechanical engineers from different eras cast a bright light on the wonder of the discipline, and how it’s changed over the years.
–Michael Baxter
Parental influence
JOHN | My dad owned a garage and machine shop in Florida. He borrowed $500 from his father to start the business. As a teenager, I worked there during the summers – first, just sweeping the floors, but later I worked the lathe and drill press and did some welding. At the time, I didn’t realize how valuable it was to get a hands-on education like that.
My father manufactured lawn mowers, the direct-drive kind, and there was nothing fancy about them. We mounted the engines, made the handlebars, even the housings. Most of the mowers had these big bicycle wheels on the back – the grass sometimes grows pretty high in Florida.
KATHERINE | I’ve never been one of the MEs who are super hands-on. I wasn’t the first person trying to nail every single nail when our team was building a robot in undergrad. But I did work with tools when I was young. I sometimes helped my dad with projects, and he taught me how to change a tire on the car. And he would always ask me questions about the world and how it worked, especially on long backpacking hikes.
Both of my parents are engineers at Lockheed Martin. They’ve seen a lot of change – early on, they got to go through the whole process of punch cards, for example. Both kept up with their engineering over the years. And they could always help me with my math and science homework growing up.
Days of study
KATHERINE | My lab research project as an undergrad involved simulating the mechanical properties of particles. I created models of synthetic vesicles using software and changing code. Essentially, I developed the specifications needed for a synthetic particle to expand to the point where it ruptured and allowed smaller particles inside, then close back up. I read research papers to understand the physical properties so that my simulations reflected what was real.
So, envision a small vesicle, a hollow sphere. The point of my project was to see the different mechanics of the sphere – to see what I had to do to the inner matrix inside to make sure it ruptures, lets small particles inside, and then closes back and re-forms properly. Knowing how to do this can lead to new ways to deliver drugs inside the body. My project won a President’s Undergraduate Research Award.
JOHN | I especially enjoyed working in the ME machine shop on campus. One part was the pattern-making lab, where we’d make patterns out of wood to create castings. We used the rough castings, which we learned about from books and the professors. I wore the slide rule on my belt like everybody else.
In 1950, I made a drill press in that shop. They furnished us with rough casting parts, and I did some machine work on them, and drilled and tapped holes. I still have that drill press – it’s in the basement of the house. We used it in my dad’s shop for many years, and I sometimes use it here. So it’s done some work. I also made a grinder, and I still use it, too.
ME outside the classroom
JOHN | After graduation in June 1951, I was called to active duty. Korean War. First I was with anti-aircraft artillery unit in Bavaria, and later I was stationed at Kaiserslautern, near the French border. I returned to Georgia Tech in 1954 to work in the Engineering Experiment Station with other engineers. We mostly did prototype work, building prototype radar systems for the military.
One project involved creating these geodesic lenses that were part of the radar system. Picture two aluminum bowls, each about 4 feet in diameter, and each made out of a flat sheet of aluminum, spun against a large wooden mandrel. They had to be carefully machined, then nested together. I ended up going to Boston and spending five weeks there to supervise their manufacturing. That was an experience.
I was in awe of some of the guys who worked at the Experiment Station. Just really smart, really capable people. We worked as a true team.
KATHERINE | I had a summer internship working for Schlumberger in Houston. They serve companies in the oil and natural gas industry around the world. When a company is drilling for oil, they sometimes need to have sections of the pipe blocked off with this device – I can’t talk much about what it is, but the device takes one form to be put into a pipe, then changes form to serve as a plug. All of this happens in outdoor conditions, so they wanted to make sure that mud and liquid didn’t create problems for the device when it changed form.
So my job was to use ANSYS Workbench software to simulate flow patterns over the device. For example, I created simulations of how mud would flow over this piece of technology – I would apply a wide range of data about conditions to simulate the mud flow. The resulting information would be used to help them decide whether to activate the device in certain conditions.
ME at work in the world
JOHN | One of my colleagues at the Experiment Station, Allen Ivey, had moved on to doing some investigative work in engineering for the insurance industry, and he came back and said, “Let’s put together a business in this field.” Insurance companies need outside help to investigate claims. So we formed Cerny & Ivey Engineering to do just that.
We would investigate cases of failed machinery, explosions, fires, accident reconstruction, structural defects in buildings – our job was to provide an independent analysis. We were called in for many different kinds of cases. What caused this crane to overturn? Why did this amusement park ride fail? Could this accident in the paper mill have been prevented?
We also had a testing lab. Companies would provide us with a product, and we’d test it. For example, the mobile home industry would provide roof sections and wall sections for testing of their load bearing. Our firm ultimately grew to about 12 employees, and we had a number of chemical, mechanical and electrical engineers working as consultants.
KATHERINE | Since I’m a graduate student, my professional work experience is limited. I am taking a Special Problems course, however, which requires us to solve a real-world problem. Basically, I’m continuing what I started in my undergraduate lab project. Before, I was expanding a sphere to create a hole where smaller particles could enter. The method I’m working on now is different – it involves getting the larger particle to capture the smaller particles on top, then having the larger particle self-fold to keep the smaller particles inside.
Imagine polymer sheets made up of two layers, which have mechanical and chemical properties. I input different data points for pressure, motion, temperature change or other stimuli in order to simulate movement in these sheets – to make them fold or bend, and repeat the process, or reverse it. This might be a different way of getting drugs into a larger particle. It’s still simulation work – I picked the research area after looking at bios and papers of research professors.
View of the alma mater
KATHERINE | The best part about going to Georgia Tech has to be the diversity. Tech has so many different classes to take, there’s so much to choose. There’s also diversity through the different faculty. We have professors from all over the world come to teach here. That’s given me a real variety of specializations and perspectives.
I’m also passionate about teaching and tutoring. I have a TA position and help students in lab who have questions. I would like to teach someday, but first work in industry.
JOHN | When I arrived at Georgia Tech, it was awesome to be in a large city for the first time. It was right after World War II, in the fall of 1947. Georgia Tech was covered up with vets. It was tough on us teenagers to compete with them – quite a few of the vets were married with children. They were older, and they were smart.
I’ve kept in touch with Georgia Tech over the years. Many a time, I called upon professors and employees who worked at the Experiment Station to help us in the business. I hired experts in metallurgy, electronics, chemical engineering and other fields.
Today, I see the publications that Georgia Tech puts out, as well as some of the engineering societies, and what’s happening in mechanical engineering is really, really amazing.
Why mechanical engineering?
KATHERINE | There are more job opportunities in ME, and at so many levels. And I like trying new things. I don’t want to be doing the same thing over and over.
When you’re doing research in essence, a lot of times it hasn’t been done before. Last year, when I was doing coding, it may have been just coding in a section of the field. But when I went to the Web and browsed through research papers, I learned that this particular area hadn’t been explored before. That was exciting. People had done variations, but they had never done this particular thing. So every time you try to solve a problem, you might come at it from a different approach. You use all sorts of skill sets from all classes of mechanical engineering.
JOHN | After working in my dad’s shop, I knew that if I was going to go into engineering, it was going to be mechanical. I’ve always found the field interesting. When I had the firm, I became a member of several engineering societies, I attended conferences and seminars, I read the literature. There’s no more interesting way to make a living.