Getting Ready to Soar. Since August of 2018, members of the Sustain Alive team have gathered at least twice weekly to work on Sustain Alive, the rocket they will submit to the Spaceport America Cup competition in June.
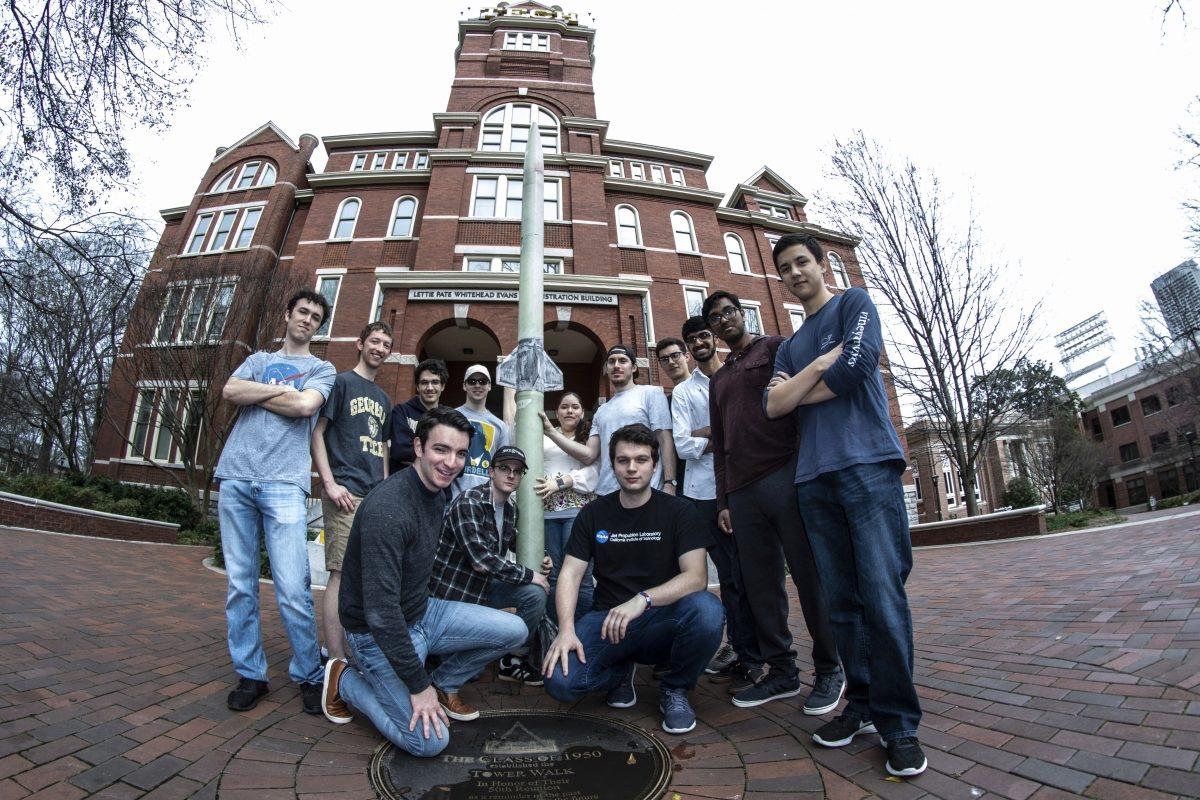
They are, from left to right: (kneeling) Matthieu Capuano, Carson Coursey, Casey Wilson. (back row) Carson Dobbs, Nicholas Brophy, Taha Krarti, Austin Hatch, Brenda Valdez, Matthew Chicky, Eduardo Sebastian, Vishnu Pulavarthi, Shanmurugan Selvamurugan, Michael Watanabe. (not shown: Rachel Thomas, Simon Pahlsmeyer, Sawyer Flanagan, Dan Fries, Patrick Finley, Mai Vo, Austin Lee, Blake Lathrop, Benjamin Jensrud, Coleman Pethel)
First-year aerospace engineering student Nicholas Brophy may have a lot on his mind these days - finals, registration, homework - but he seems pretty chill.
That may be because the Arkansas native is burning off that nervous energy working on Sustain Alive, a 13.5-foot, 110-pound rocket that he's hoping will fly to 30,000 feet at June's Spaceport America Cup competition.
"For me, there's no question that I'm going to spend my free time working on this," he says of the rocket -- Georgia Tech's first-ever submission to the world-wide rocket competition.
"In high school, none of us would have been able to build anything like this, but, now, every time I come to work on it, I learn something new from everyone on the team. We all bring some knowledge that gets applied somewhere on this project. And it's really cool."
Cool, indeed.
Brophy is one of more than 20 mostly AE School students who've been brought together by the Ramblin Rocket Club to form Spaceport Cup team that's designing, fabricating, and building the two-stage rocket. With a June 2019 competition date in sight, the team is now busy fabricating components and readying the airframe for the installation of two Cesaroni motors. When they
transport it to the Las Cruces, New Mexico competition in June, they will be up against more than 100 teams from around the world.
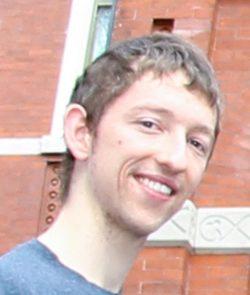
The Spaceport America Cup divides entries into various categories, mostly defined by the type of motor used and the target height of the vehicle's ascent.
Rachel Thomas and Sawyer Flanaganusing a milling machine to drill holes in the sustainer section of the rocket.
photo courtesy Casey Wilson
"We chose to enter the category that required commercial-off-the-shelf motors and a 30,000-foot target apogee ," said Matthew Chicky, a second-year AE master's student who has been coaching the team with fellow AE master's student Robert 'Casey' Wilson and AE doctoral student Dan Fries.
"We also chose a two-staged rocket, with two motors, because we really didn't want this to be easy. We could have gone with one rocket and one really powerful motor, but then where's the challenge?"
The challenge was there, all right. For most of the past year, team members have devoted nights and weekends to learning new skills (and machines) so that they could design and build the airframe, bulkheads, fins, and other parts to spec.
"We need to keep it light, so sometimes we were talking about how to shave off one-tenth of a pound," said Brophy. "That's what a nine-volt battery weighs, so, what you're talking about is: do you want another battery there for added redundancy or is the risk acceptable?"
A lot of that learning took place in the basement of the Montgomery Knight building, where the students worked with Aero Maker Space Machine Shop staff like Chicky to fabricate the components.
"It might take 12-15 hours to fabricate the bulkheads [that bear the thrust from the motor and deliver it to the airframe]," said Chicky.
"No one student could spend that kind of time in the machine shop, so we had six or seven students who got really good at handing the project off without a problem."
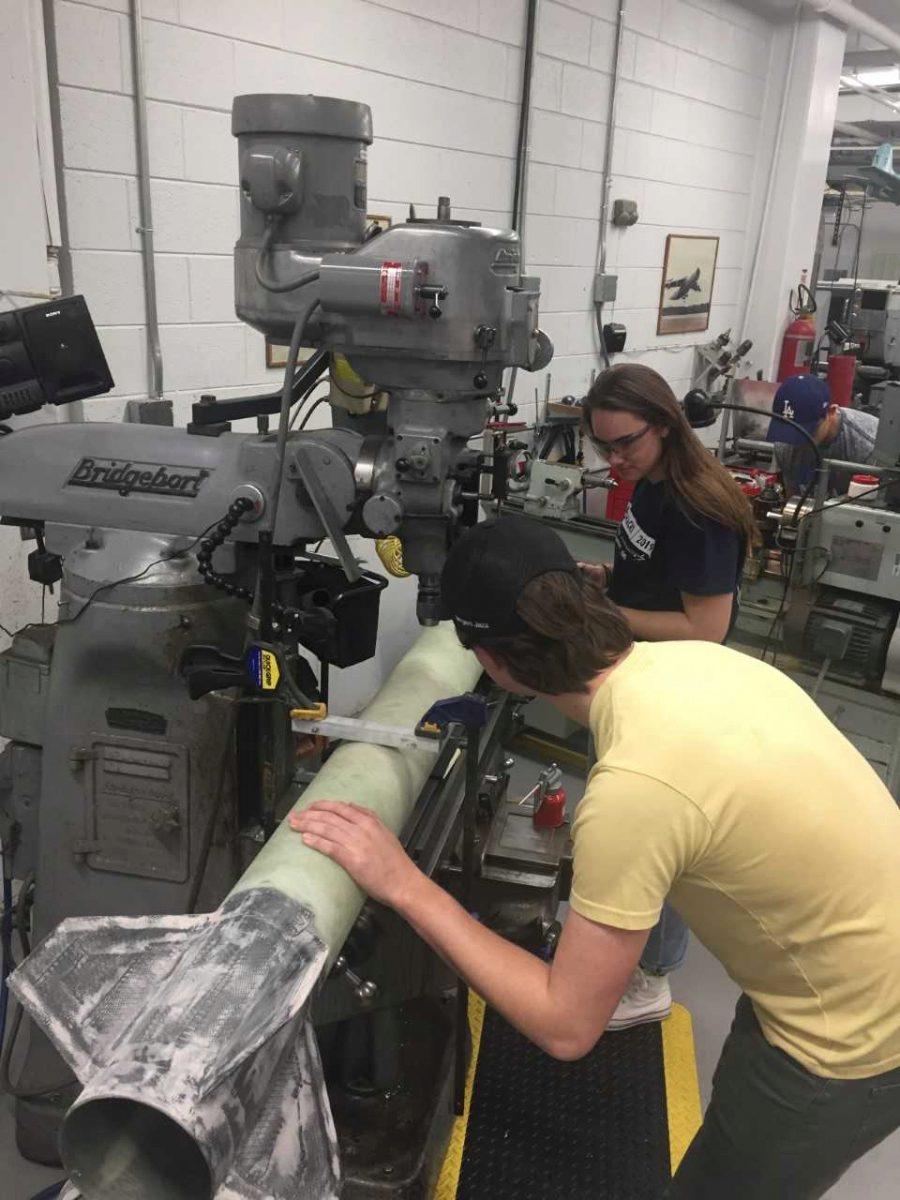
"This was designed to be a learning challenge, and to build capacity for future students. If we went slower during the design and fabrication stage, it was because we wanted everyone on the team to be well-informed, confident engineers. With some teams, you have two or three people who do most of the work, but on this team, we had everyone working. And with 75 percent freshmen, that means we'll still have a strong team when the upper classmen graduate."
For now, however, the team isn't thinking about graduations, workloads, or even the cessation of Atlanta's unusually soggy spring weather. All minds are focused on Sustain Alive.
"The thing we're most nervous about is the staging phase," says Wilson.
"That's when the booster falls away and the sustainer rocket's motor ignites, sending the upper stage, we hope, to a 30,000-foot apogee. If the separation is too powerful, you could damage the upper stage sustainer rocket or cause it to change angle, so it wouldn't be flying straight up. In that case, it might not make 30,000 feet. If it's not powerful enough, then the two sections won't separate, but the sustainer rocket's motor will still ignite, and, well, it may still make it to 30,000 feet, but the booster could be damaged."
This is where the name of this rocket begins to make perfect sense. Say it quickly enough, and you'll find yourself humming an old BeeGees hit that nicely echoes their fears and dreams: Stayin Alive.
Somehow, we think they'll do more than stay live.
After all, they're Georgia Tech. They can do that.
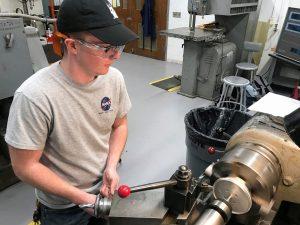
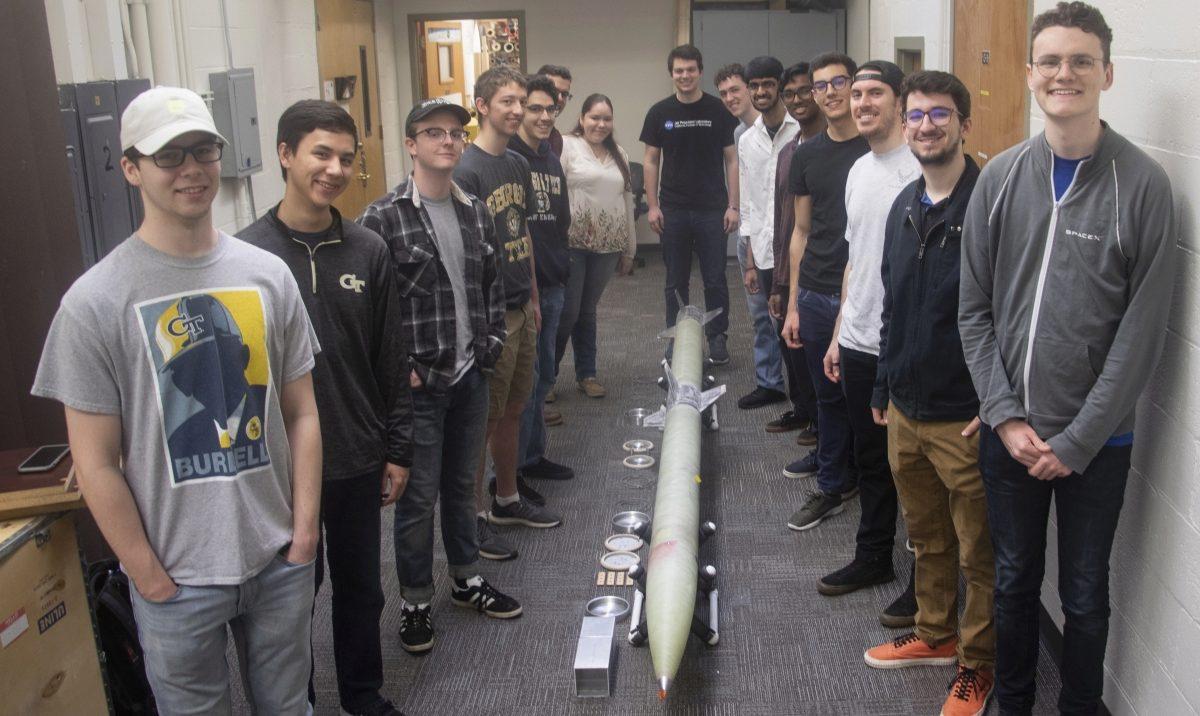