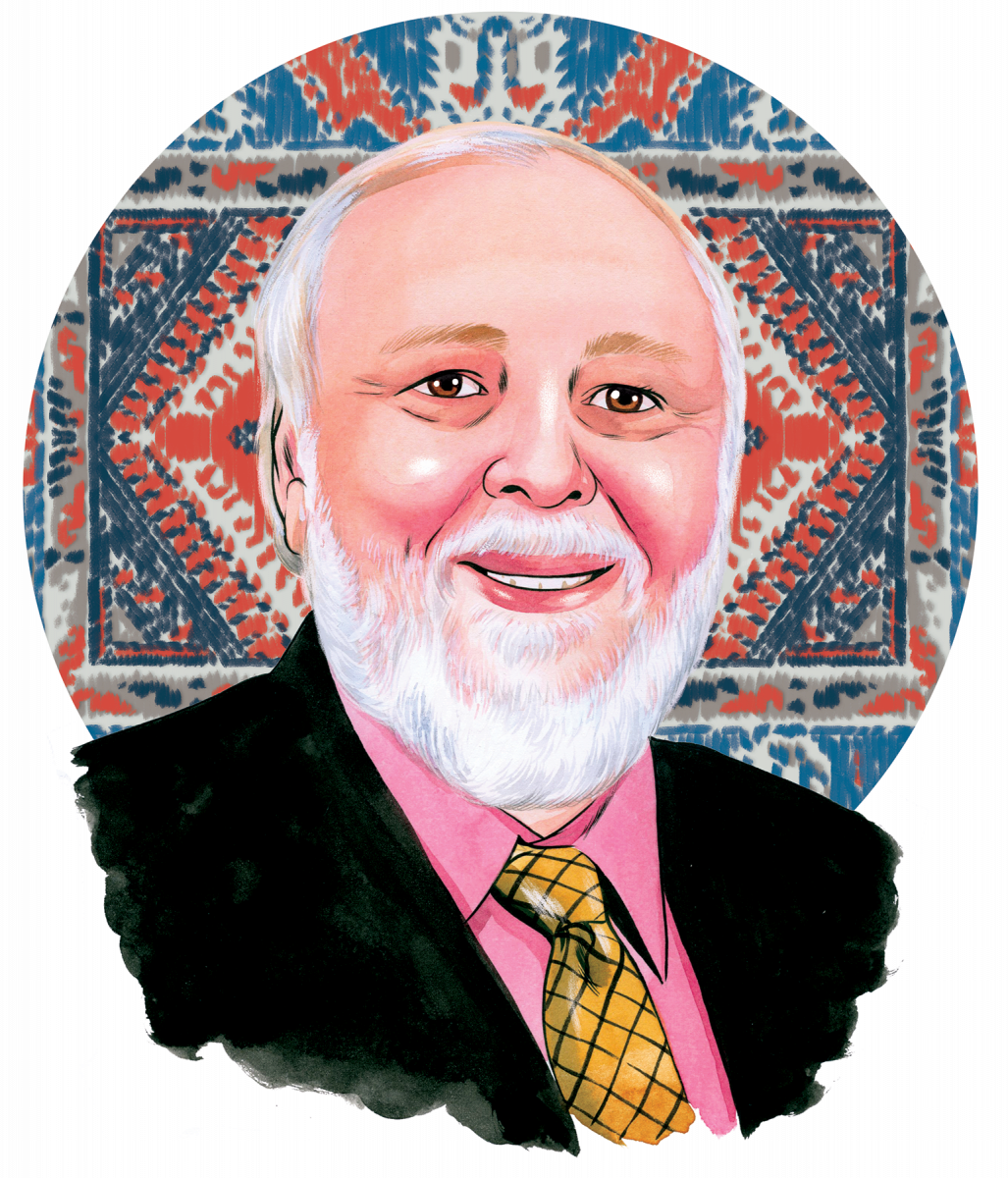
Carpet means big business in Georgia, and Tech professor Fred Cook has been instrumental in bringing cutting-edge textile and polymer chemistry research to the industry. Starting in the 1970s through research and consulting, he helped the likes of Shaw Industries create today’s carpet capital of Dalton, just 90 miles outside of Atlanta. Cook is an alumnus and professor emeritus in the School of Materials Science and Engineering (MSE). Outside the halls of academia, he has also served as an expert witness in high-level patent court cases. He also makes time to take care of his horse and cattle farm in Jackson.

Where are you from?
Jackson, Georgia
When did you graduate from Georgia Tech?
In 1971, I got my bachelor’s in textile chemistry. Back then, it was the School of Textile Engineering. Today, it’s the School of Materials Science and Engineering. In 1975, I was the forerunner of the Textile Engineering Ph.D. program, but, officially, I earned my doctorate in organic polymer chemistry.
What is your role at Tech?
I am professor emeritus in MSE and retired three years ago.
What got you interested in textile research?
It actually goes back to when I was in high school. I'd already been accepted into chemical engineering at Tech. A group of faculty came by the high school, recruiting for what was then the school of textiles. There was one guy, Gerald Fletcher, who gave me a quote I never have forgotten. He said, "Chemical engineering goes up and down, depending on what the oil market is doing. But as long as we don't go nude, people will always need clothes." That made good sense to me.
Why is Dalton, GA, the carpet capital of the world?
Well, the whole industry developed out of Dalton, GA. The forerunner to it was the chenille bedspread industry. In the early 1900s, a woman in the mountains of North Georgia came up with this idea of tufted chenille bedspreads, and her sons formed an industry around the concept, developed the machinery and automated it, and started producing chenille bedspreads for the masses. After WWII, they had the idea of using a cheaper nylon fiber that could be tufted and glued to create a carpet floor covering that the public could afford. Up until then, carpet was woven from wool yarns and very expensive. The cheaper tufted carpet essentially made the floor covering available to the general public. By adapting and modifying the chenille bedspread machinery, tufted nylon carpet with woven backing gave us today’s modern floor covering. The bottom-line, Dalton is the carpet capital of the world because about 90 percent of the tufted carpet that's made in the U.S. is made within about 60 miles of downtown Dalton.
What is Tech’s role in the carpet industry?
Well, it's been two-fold, historically. First, we've supplied the industry with world-class graduates. As the industry literally exploded starting in the 50s and 60s, they needed solid technical people to come in to grow and expand the industry. What better place to look for engineers and scientists than Georgia Tech? Shaw Industries especially took the lead in hiring Tech folks. That's how Shaw industries became so prominent. They did wondrous things. Second, through joint research and development projects, Tech made contributions to new technologies for the industry.
How has your research helped to improve the carpet industry in our state?
By 1975, The School of Textile Engineering was already starting to supply the industry with a significant number of graduates. We also became the fundamental research arm for the carpet industry. We had the contacts; we had our graduates there; and there was just tremendous synergism that we were able to develop. Though companies like Shaw are very, very successful, even they can't set up a fundamental, ground-up, Ph.D.-driven research operation.
What do you see as the number one innovation that Tech has been a part of within the carpet industry?
Definitely stain-resistant topical finishes for nylon carpet. These fluoropolymer finishes gave the carpet stain-proof resistance to spills of liquids like grape Kool-Aid and coffee. As an example of how we partnered with the industry, I developed a process that sprayed powder fluoropolymer directly into the carpet tufts, followed by a melt stage to coat the surface. This process not only protected against stains, it saved energy and cut down on pollution, as it was a totally dry application.
What was it like being an expert witness in court?
I was involved in some large trials. For example, two Taiwan-based companies entered into a patent war over seam technology in men’s and women’s dress shirts. I served as an expert witness. We gave our side guidance, testified in the court case itself, and plotted strategy. It was high stakes drama with multi-million-dollar implications.
What is your favorite fabric?
Tufted carpet. It’s the epitome of engineering and design.