Agricultural technology finds a place at Tech
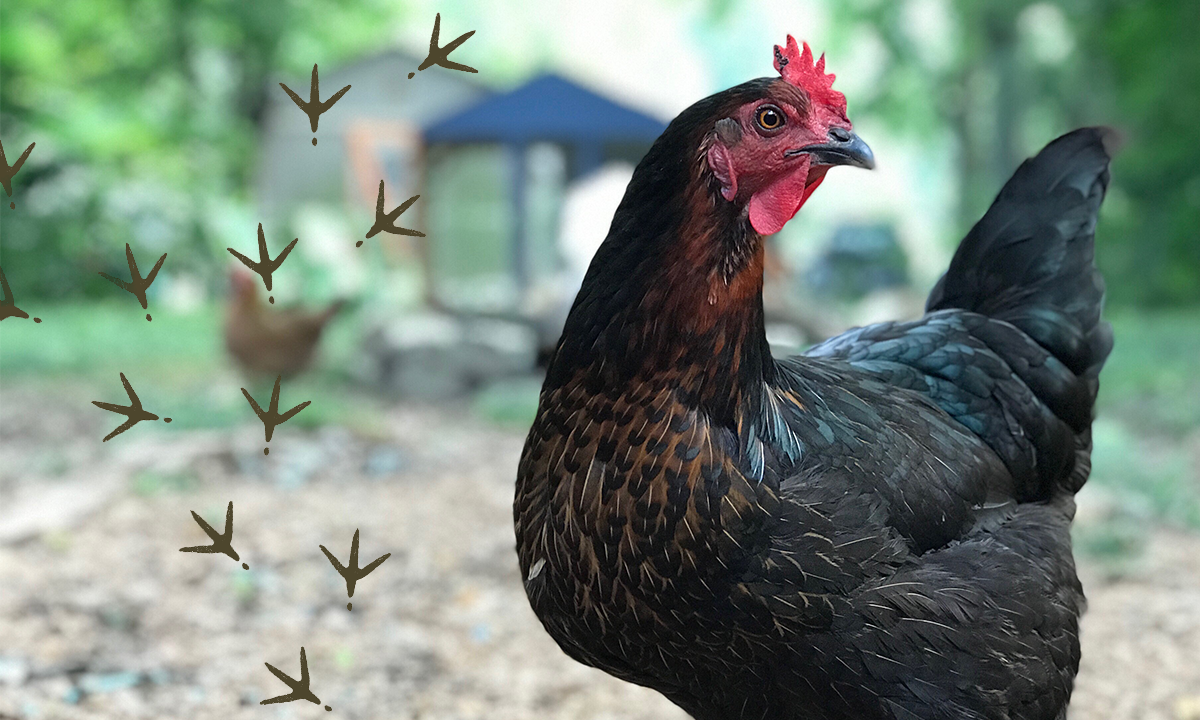
Georgia’s homegrown chicken chain Chick-fil-A boasts, “We didn’t invent the chicken, just the chicken sandwich.” Similarly, the state of Georgia can probably claim, we didn’t invent the chicken, just modern chicken production. Georgia is the top producer of broiler chickens, with 26 million pounds of chicken meat produced daily. The birds bring in $48 billion to the state economy each year.
That’s a lot of chicken sandwiches. And Georgia Tech does its part for one of the state’s biggest industries.
Across many engineering research labs on campus, you’ll see students working on robots that zip through chicken houses to scoop up eggs. Researchers are 3D-printing parts for intelligent cutting machines that dice up chicken with more speed and efficiency. There’s even a listening device that can hear when baby chicks are squawking and better respond to their needs. In a state known for Big Chicken, Georgia Tech engineers play an important role.
Tech’s friendly rival to the east, the University of Georgia, has long been a crucial player in the poultry industry, from chicken breeding to poultry sciences. But it’s Georgia Tech engineers that are working on developing advanced technologies and software to drive the industry forward. Doug Britton heads the $2 million Agricultural Technology Research Program at the Georgia Tech Research Institute (GTRI), and is also an engineering graduate from Tech’s School of Electrical and Computer Engineering.
“As engineers, we are developing tools to improve efficiency, safety, yield and environmental impact, all while optimizing operations at farms across the state,” said Britton. “We view what we are doing at Tech as not just helping the poultry industry, but truly disrupting it through innovation.”
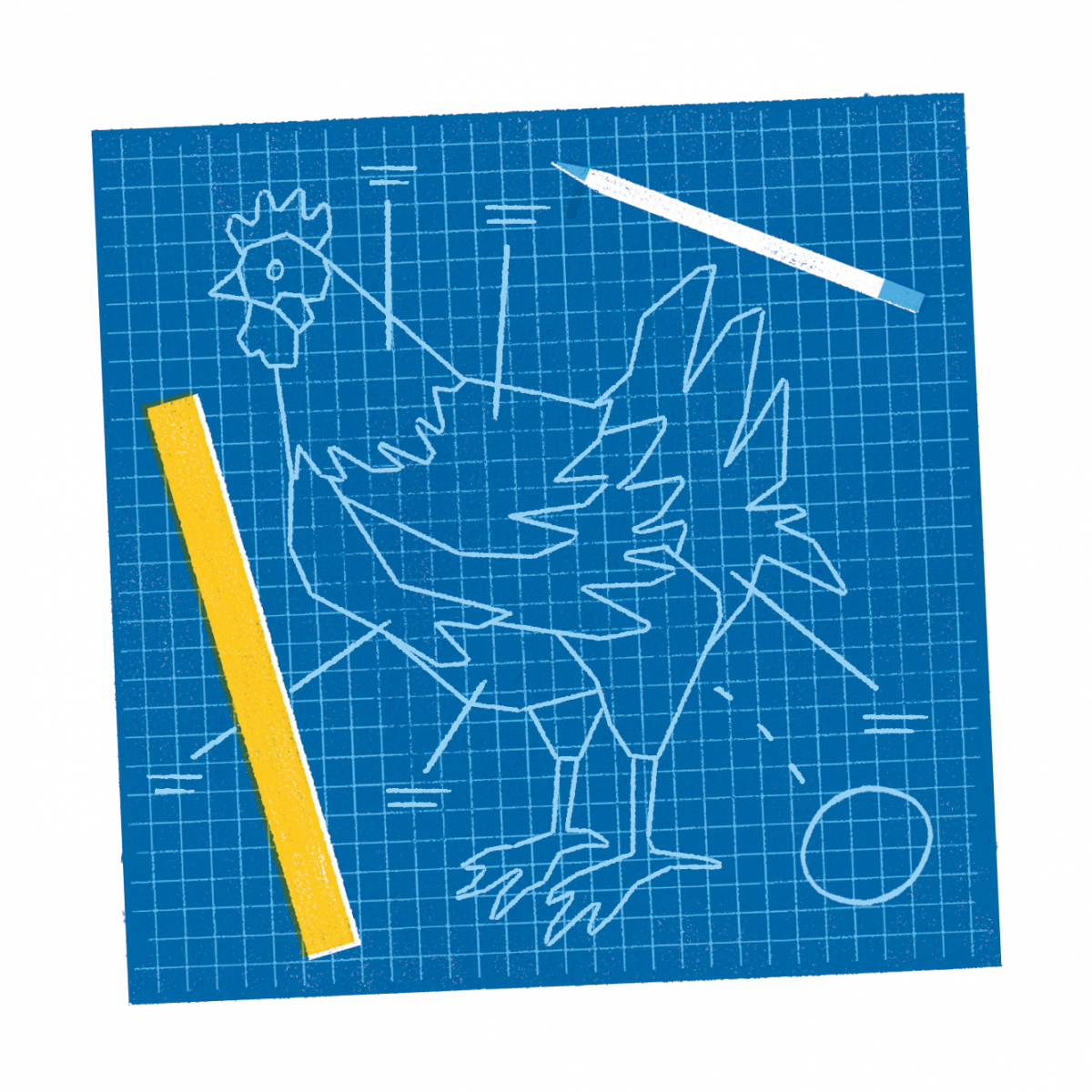
Backyard Beginnings
In the early 1900s, Gainesville, GA, came to be known as the poultry capital of the world thanks to Jesse Jewell, a civil engineering graduate from Georgia Tech. He pioneered vertical integration within the poultry industry, combining all phases of business, such as raw materials, processing, and distribution, into a single company. J. D. Jewell quickly became the largest integrated chicken producer in the world. An innovative, engineering mindset from Tech enabled Jewell to capitalize on and create a booming business in the south.
Georgia Tech jumped on the poultry band wagon in the 1930s when they established a helpline that took telephone calls from farmers. Technical experts from Tech would answer and trouble shoot engineering problems. Many of these farmers raised chickens, and Tech became an integral part of the industry, providing on-demand expertise.
Britton recalls the history of this poultry helpline and notes that, to this day, Tech is still seen as the go-to experts for technical issues in the industry. And folks are still calling, like Jerry Lane, president of Claxton Poultry and a Tech graduate. He has reached out to Tech when he’s run into waste processing problems at his farm.
“Tech was the only resource we could get that would come in and help us with the engineering problems at the farm,” recalls Lane. “After reaching out to GTRI, so many projects have now morphed out of those early questions, like ‘how do we modernize and improve operations in our facilities?’”
But now, it’s not just farmers calling, it’s big businesses like Tyson, Monsanto and Marel that are looking to Tech engineers for help. Tech engineers are heeding the call, inventing and evolving the types of technology these companies need to respond to market change and demand.

Leveraging Technology to Shape the Industry
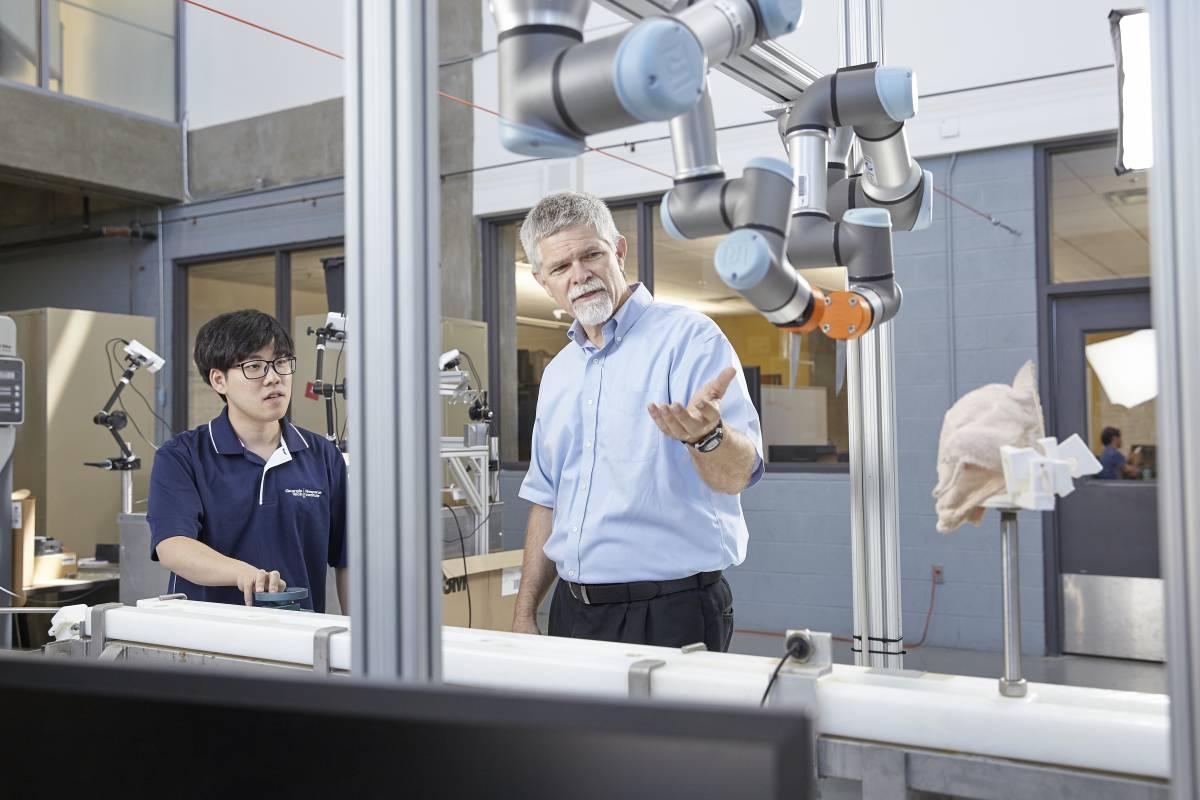
The Chopping Block
The poultry industry presents plenty of complex challenges for GTRI to tackle, and the robotics division is developing tools and processes to bring more automation to problem areas such as labor and animal welfare.
Working in a processing plant involves extremely repetitive and fatiguing manual labor. Finding workers willing to do jobs such as deboning a chicken or cutting up tenders has become increasingly difficult. Matt Brass, mechanical engineering graduate from the College, works as a project engineering manager at Marel, an equipment company that designs and supplies much of the equipment that goes into the poultry processing facilities.
“Technology has taken labor out of the plants, creating much more efficient operations,” said Brass. “If you go back and look at the prices of poultry in the 1950s, it was considerably higher than today due to the number of people involved in getting the chicken from assembly line to grocery store.”
Brass is excited about technology like the Intelligent Cutting Project, which reimagines the best way to cut up a chicken before it’s packaged for the grocery store. Historically, cutting up joints and pulling the meat off the bird was a manual task. The poultry cutting machine automates that process, while at the same time optimizing the amount of meat collected.
“Our machine is able to scan and scrape the chicken to gather even more meat than the manual process,” said Britton. “Even just a one percent yield change in the amount of meat produced in the processing plant equals $1 million in additional revenue. We can really measure the ROI this machine is giving companies.”
Workers are still important to poultry production though, and there won’t be a shortage of jobs any time soon. The required skill set is just different.
“There’s been a big shift in industry because of technology,” says Lane of Claxton Poultry. “The plants previously full of people doing all the work are now loaded with highly technical equipment. You still see many workers, but they are monitoring and inspecting as opposed to doing the manual hand work.”
Birds of a Feather
Other innovations coming out of Tech are more focused on animal welfare with an added business bonus of creating smoother operating processes.
A listening tool developed by Brandon Carroll (PhD, electrical engineering, 2018) records an audio track of the chickens in the grow-out houses. Britton notes that it’s been five years in the making and expected to be commercially available soon. The device listens for anomalies in chicken sounds and records them. To regulate and improve bird welfare, the device listens and maps noise that could signify distress. Farm operations can then be adjusted accordingly. For example, if there is squawking at 1 a.m. because a heater malfunctions and the chickens are cold, the device can notify workers that there is a problem.
The Grow-Out robot is another innovation from Tech engineers that travels throughout the grow-out house - where the chickens live - to monitor the birds. It also has an arm that collects eggs.
“Hens have a mob mentality,” explains Britton. “If one hen lays an egg, all the other hens will do the same. We want them laying in the houses so the eggs are protected, not on the floor. So, if an egg lands on the floor, the robot quickly scoops it up so the others don’t follow suit.”
The Grow-Out robot also checks for diseases throughout the house, which can be highly contagious. Farmers can easily spread germs to other houses, just from the bottom of their shoes. But if each house has their own robot, there is zero cross contamination, creating greater bio security and healthier, happier birds.
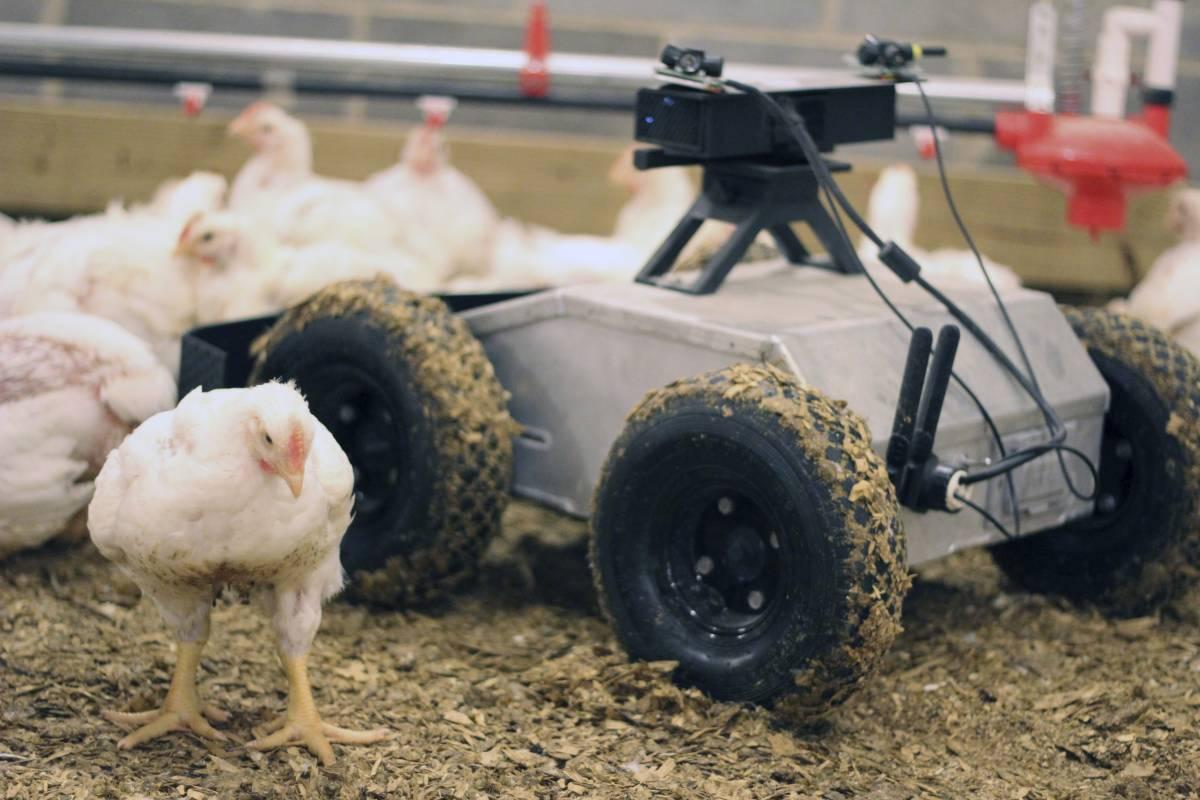
Coming Home to Roost
One of the keys to maintaining success across Georgia’s poultry industry is sustainability. Recent projections from Cargill estimate that global meat consumption is expected to increase seven percent by 2023, with more than 70 percent of that growth potentially coming from poultry. And engineers like Britton and Lane are hyper aware that the industry needs to adapt to that demand in a sustainable way.
“At Claxton, sustainability is critical to what we do,” says Lane. “If we can’t sustain our own operations and those of the industry as a whole, then we have a problem. Our company has been here for 60 years and intends to stay at least another 60, but it will depend on how well we take care of our environment.”
Additionally, consumers are increasingly looking to purchase foods that are produced in a sustainable manner. People care more about the environment a chicken is raised in—is it cage free or free range? They want meat that is free from antibiotics and steroids. And they are willing to pay top dollar.
John Starkey, president of US Poultry and Egg Association and Georgia Tech environmental engineering graduate, said that he has seen humane housing systems and sustainable practices improve in recent years.
“In my grandmother’s lifetime, it took four to five pounds of feed to make a pound of chicken,” Starkey said. “Now, it’s two pounds of feed to make a pound of chicken. Think about the impact on the acres of corn, fertilizer and tractor runs all having to do with creating feed for chickens. At the end of the day, what we have created is a much more sustainable industry than it was when I stepped into it back in 1982.”
Civil engineers are reimagining what farm systems look like, ensuring waste is disposed of in a responsible manner, creating a healthy bird habitat. Industrial engineers are optimizing the poultry supply chain, getting birds from point A to point B in the most humane way possible. And of course, mechanical engineers are building the robots that monitor bird health and make plant processes as efficient as possible.
“As partners to the poultry industry, we must be the thought leaders that help industry adapt to changing consumer demands and drive technology innovations that impact the bottom line,” says Britton. “Agricultural robots. AI. Advanced imaging. These are all potentially positive disrupters to the industry. And as engineers, we must be on the front lines exploring and facilitating this change.”