The membranes would improve distillation processes that account for 1% of the world’s energy use.
(text and background only visible when logged in)
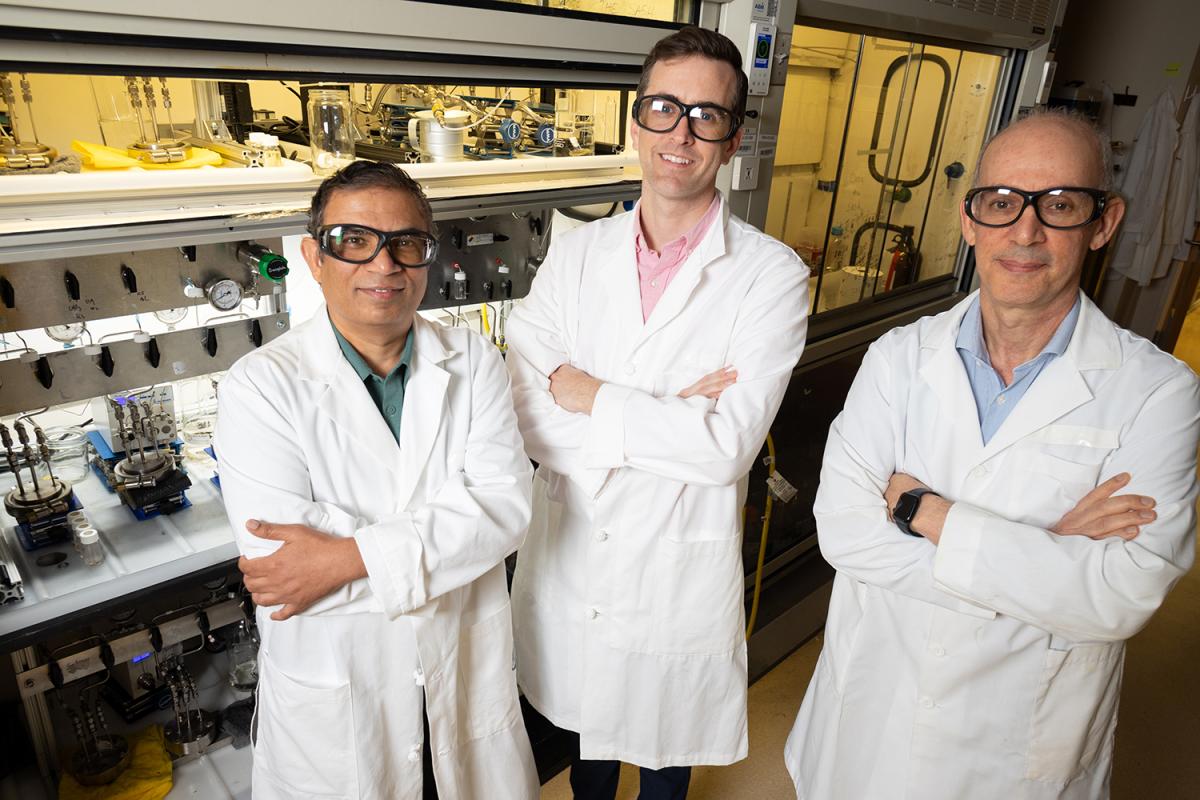
From left, researchers Rampi Ramprasad, Ryan Lively, and M.G. Finn, who have created a new kind of polymer membrane for separating crude oil into useful components. The membrane could greatly reduce the energy necessary for those initial separations. They’ve also created artificial intelligence tools to predict the performance of these kinds of polymer membranes, which could accelerate development of new ones. (Photo: Candler Hobbs)
(text and background only visible when logged in)
A new kind of polymer membrane created by researchers at Georgia Tech could reshape how refineries process crude oil, dramatically reducing the energy and water required while extracting even more useful materials.
The so-called DUCKY polymers — more on the unusual name in a minute — are reported Oct. 16 in Nature Materials. And they’re just the beginning for the team of Georgia Tech chemists, chemical engineers, and materials scientists. They also have created artificial intelligence tools to predict the performance of these kinds of polymer membranes, which could accelerate development of new ones.
The implications are stark: the initial separation of crude oil components is responsible for roughly 1% of energy used across the globe. What’s more, the membrane separation technology the researchers are developing could have several uses, from biofuels and biodegradable plastics to pulp and paper products.
“We’re establishing concepts here that we can then use with different molecules or polymers, but we apply them to crude oil because that’s the most challenging target right now,” said M.G. Finn, professor and James A. Carlos Family Chair in the School of Chemistry and Biochemistry.
Crude oil in its raw state includes thousands of compounds that have to be processed and refined to produce useful materials — gas and other fuels, as well as plastics, textiles, food additives, medical products, and more. Squeezing out the valuable stuff involves dozens of steps, but it starts with distillation, a water- and energy-intensive process.
Researchers have been trying to develop membranes to do that work instead, filtering out the desirable molecules and skipping all the boiling and cooling.
“Crude oil is an enormously important feedstock for almost all aspects of life, and most people don’t think about how it’s processed,” said Ryan Lively, Thomas C. DeLoach Jr. Professor in the School of Chemical and Biomolecular Engineering. “These distillation systems are massive water consumers, and the membranes simply are not. They’re not using heat or combustion. They just use electricity. You could ostensibly run it off of a wind turbine, if you wanted. It’s just a fundamentally different way of doing a separation.”
What makes the team’s new membrane formula so powerful is a new family of polymers. The researchers used building blocks called spirocyclic monomers that assemble together in chains with lots of 90-degree turns, forming a kinky material that doesn’t compress easily and forms pores that selectively bind and permit desirable molecules to pass through. The polymers are not rigid, which means they’re easier to make in large quantities. They also have a well-controlled flexibility or mobility that allows pores of the right filtering structure to come and go over time.
The DUCKY polymers are created through a chemical reaction that’s easy to produce at a scale that would be useful for industrial purposes. It’s a flavor of a Nobel Prize-winning family of reactions called click chemistry, and that’s what gives the polymers their name. The reaction is called copper-catalyzed azide-alkyne cycloaddition — abbreviated CuAAC and pronounced “quack.” Thus: DUCKY polymers.
In isolation, the three key characteristics of the polymer membranes aren’t new; it’s their unique combination that makes them a novelty and effective, Finn said.
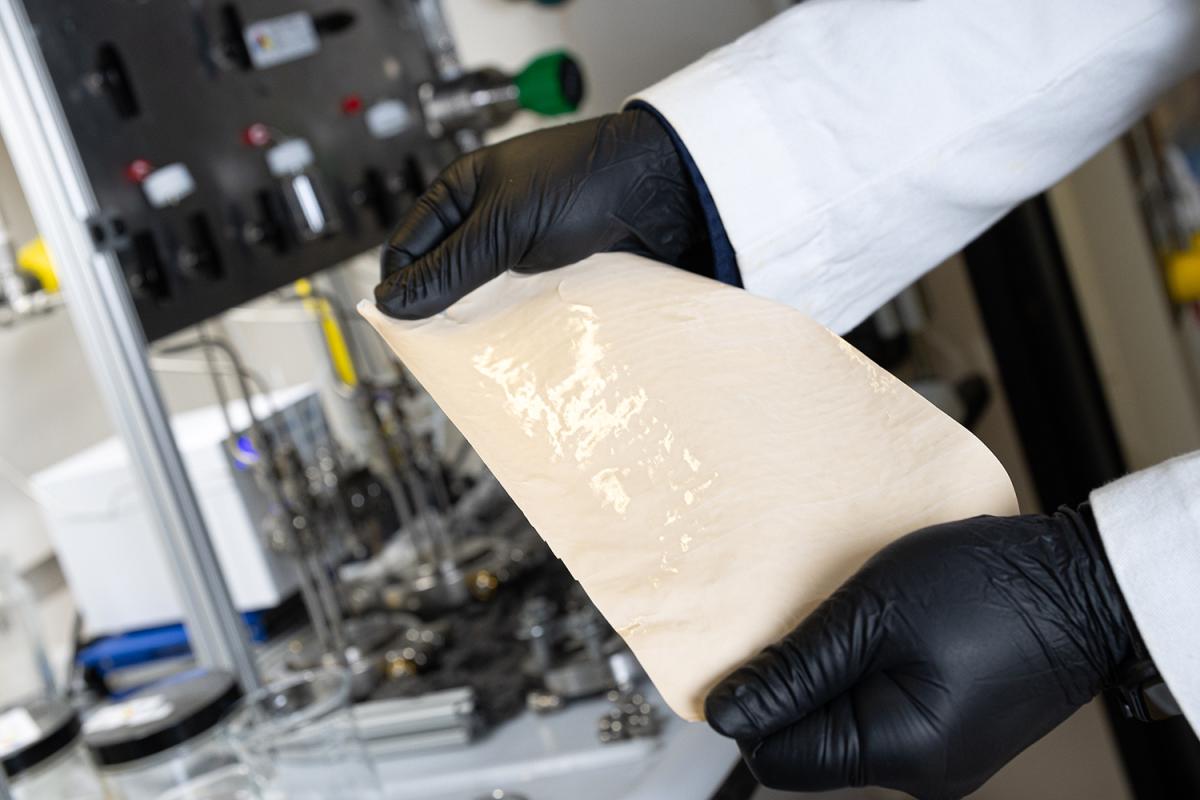
A sample of a DUCKY polymer membrane researchers created to perform the initial separation of crude oils using significantly less energy. (Photo: Candler Hobbs)
The research team included scientists at ExxonMobil, who discovered just how effective the membranes could be. The company’s scientists took the crudest of the crude oil components — the sludge left at the bottom after the distillation process — and pushed it through one of the membranes. The process extracted even more valuable materials.
“That’s actually the business case for a lot of the people who process crude oils. They want to know what they can do that’s new. Can a membrane make something new that the distillation column can’t?” Lively said. “Of course, our secret motivation is to reduce energy, carbon, and water footprints, but if we can help them make new products at the same time, that's a win-win.”
Predicting such outcomes is one way the team’s AI models can come into play. In a related study recently published in Nature Communications, Lively, Finn, and researchers in Rampi Ramprasad’s Georgia Tech lab described using machine learning algorithms and mass transport simulations to predict the performance of polymer membranes in complex separations.
“This entire pipeline, I think, is a significant development. And it’s also the first step toward actual materials design,” said Ramprasad, professor and Michael E. Tennenbaum Family Chair in the School of Materials Science and Engineering. “We call this a ‘forward problem,’ meaning you have a material and a mixture that goes in — what comes out? That’s a prediction problem. What we want to do eventually is to design new polymers that achieve a certain target permeation performance.”
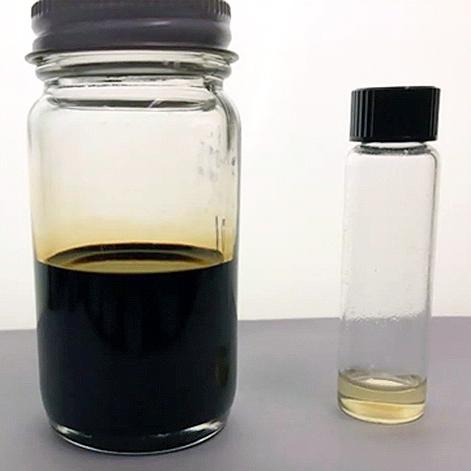
At left, a sample of Arabian light crude oil before passing through one of the new polymer membranes the research team developed. The smaller sample on the right shows some of the valuable material extracted by the membrane. (Photo Courtesy: ExxonMobil Technology and Engineering Company)
Complex mixtures like crude oil might have hundreds or thousands of components, so accurately describing each compound in mathematical terms, how it interacts with the membrane, and extrapolating the outcome is “non-trivial,” as Ramprasad put it.
Training the algorithms also involved combing through all the experimental literature on solvent diffusion through polymers to build an enormous dataset. But, like the potential of membranes themselves to reshape refining, knowing ahead of time how a proposed polymer membrane might work would accelerate a materias design process that’s basically trial-and-error now, Ramprasad said.
“The default approach is to make the material and test it, and that takes time. This data-driven or machine learning-based approach uses past knowledge in a very efficient manner,” he said. “It’s a digital partner: You’re not guaranteed an exact prediction, because the model is limited by the space spanned by the data you use to train it. But it can extrapolate a little bit and it can take you in new directions, potentially. You can do an initial screening by searching through vast chemical spaces and make go, no-go decisions up front.”
Lively said he’d long been a skeptic about the ability of machine learning tools to tackle the kinds of complex separations he works with.
“I always said, ‘I don't think you can predict the complexity of transport through polymer membranes. The systems are too big; the physics are too complicated. Can’t do it.’”
But then he met Ramprasad: “Rather than just be a naysayer, Rampi and I took a stab at it with a couple of undergrads, built this big database, and dang. Actually, you can do it,” Lively said.
Developing the AI tools also involved comparing the algorithms’ predictions to actual results, including with the DUCKY polymer membranes. The experiments showed the AI models predictions were within 6% to 7% of actual measurements.
“It’s astonishing,” Finn said. “My career has been spent trying to predict what molecules are going to do. The machine learning approach, and Rampi’s execution of it, is just completely revolutionary.”
(text and background only visible when logged in)
(text and background only visible when logged in)
Related Content
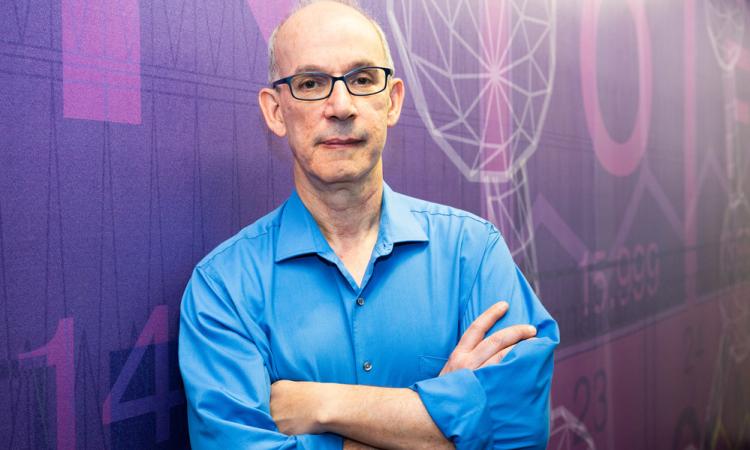
The Nobel Whisperer: M.G. Finn on Click Chemistry and Collaboration
How chemist M.G. Finn helped establish the foundation for the Nobel Prize-winning technique now used in labs around the world.
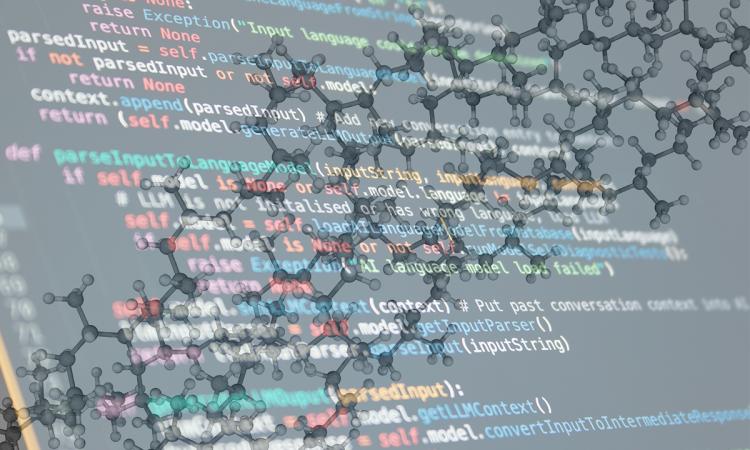
Algorithm Learns Chemical Language to Accelerate Polymer Research
MSE researchers developed a machine learning model to cut down on the time-consuming effort to identify new combinations of materials that could be effective polymers.
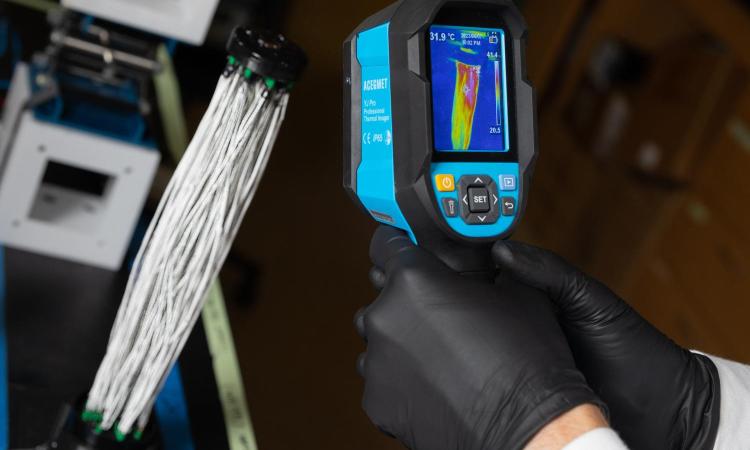
Inside-Out Heating and Ambient Wind Could Make Direct Air Capture Cheaper and More Efficient
Chemical engineers use coated carbon fibers and eliminate steam-based heating in their simpler design, which also can be powered by wind energy.
(text and background only visible when logged in)
About the Research
This research was supported by the U.S. Department of Energy, grant No. DE-EE0007888; the European Research Council, grant No. 758370; the Kwanjeong Educational Foundation; a Royal Society University Research Fellowship; and the ExxonMobil Technology and Engineering Company. Any opinions, findings, and conclusions or recommendations expressed in this material are those of the authors and do not necessarily reflect the views of any funding agency.
Citations
Bruno, N.C., Mathias, R., Lee, Y.J. et al. Solution-processable polytriazoles from spirocyclic monomers for membrane-based hydrocarbon separations. Nat. Mater. (2023). https://doi.org/10.1038/s41563-023-01682-2
Lee Y.J., Chen L., Nistane J. et al. Data-driven predictions of complex organic mixture permeation in polymer membranes. Nat Commun 14, 4931 (2023). https://doi.org/10.1038/s41467-023-40257-2
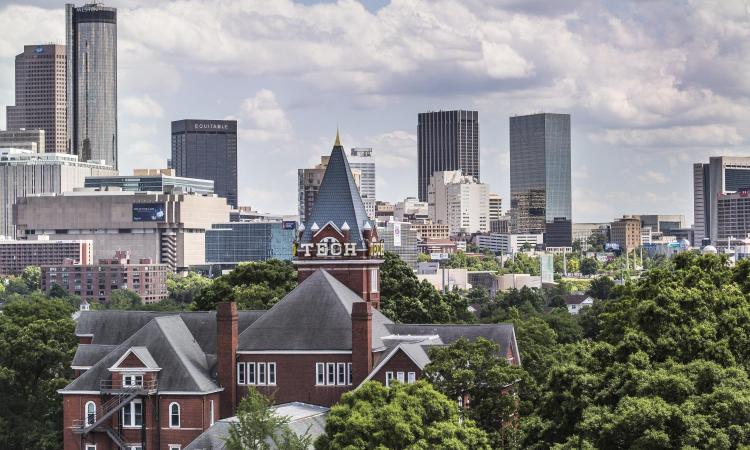