Researchers use UV light instead of high heat to make glass that can be used for medical devices, microelectronics, and more.
(text and background only visible when logged in)
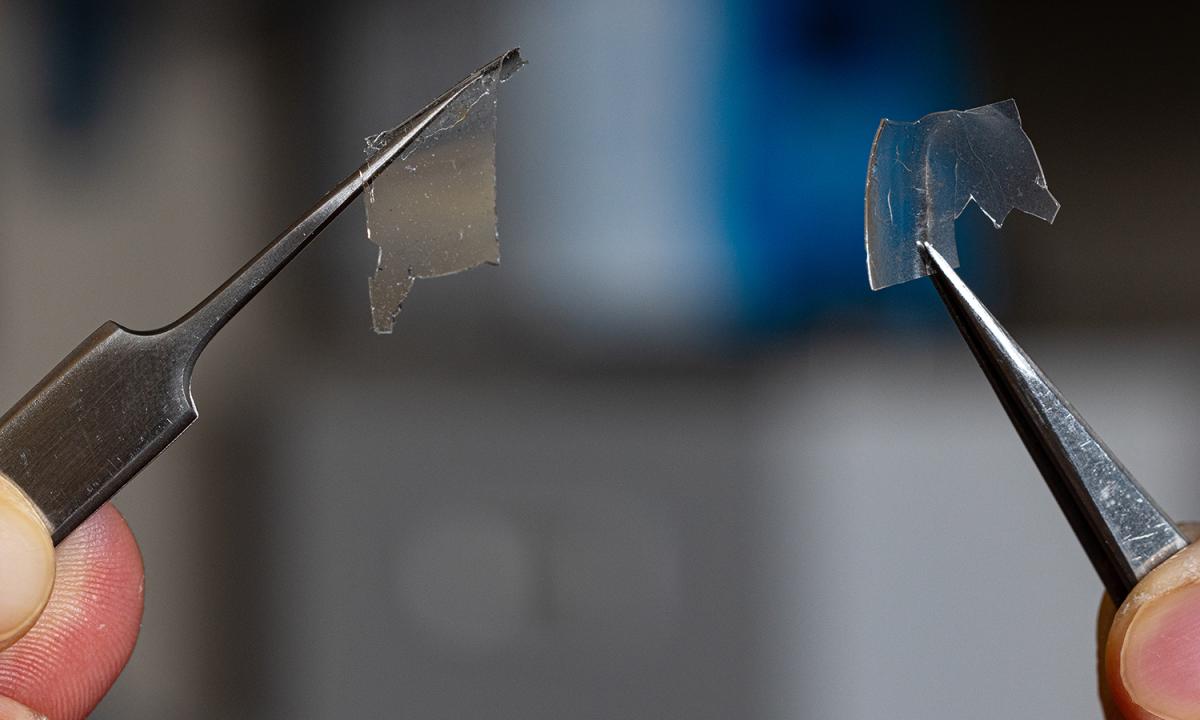
Researchers used this raw material to create 3D-printed glass structures no bigger than the width of a human hair. The researchers employed a light-sensitive resin based on a widely used soft polymer called PDMS, at left. The sample on the right is glass created using deep UV light to convert the the photoresin to hardened inorganic glass. (Photo: Candler Hobbs)
(text and background only visible when logged in)
Using ultraviolet light instead of extremely high temperatures, a team of Georgia Tech researchers has developed a new approach for 3D printing small glass lenses and other structures that would be useful for medical devices and research applications.
Their process reduces the heat required to convert printed polymer resin to silica glass from 1,100 degrees Celsius to around 220 degrees C and shortens the curing time from half a day or more to just five hours. They’ve used it to produce all kinds of glass microstructures, including tiny lenses approximately the width of a human hair that could be used for medical imaging inside the body.
Led by George W. Woodruff School of Mechanical Engineering Professor H. Jerry Qi, the team described their approach Oct. 4 in the journal Science Advances.
“This is one of the exploratory examples showing that it is possible to fabricate ceramics at mild conditions, because silica is a kind of ceramic,” Qi said. “It is a very challenging problem. We have a team that includes people from chemistry and materials science engaged in a data-driven approach to push the boundary and see if we can produce more ceramics with this approach.”
Along with miniaturization of lenses for medical endoscopes, these 3D printed glass structures could create microfluidic devices — typically small computer chip-like devices with nano- or microscale channels used to study cells or biofluids in motion. Glass chips would offer advantages over current chips made of polymer materials, the researchers said, resisting corrosion from chemicals or body fluids.
The low-temperature process also would enable fabrication of microelectronics with glass structures, according to Mingzhe Li, the study’s first author.
“We can print in situ, directly into microelectronics,” said Li, a postdoctoral researcher in Qi’s lab. “Semiconductor materials used in microelectronics cannot withstand very high temperatures. If we want to print directly on a board, we have to do it at a low temperature, and 200 degrees C can definitely do this job.”

A 3D printed glass microfluidic channel, shown hollow and filled with liquid.
The team’s printing process presents a climate friendlier option for silica glass manufacturing.
Typical additive manufacturing processes for glass require polymer mixtures that must be burned away with heat once the desired shapes are formed. The Georgia Tech team’s approach uses a photoresin that is converted to glass using a kind of ultraviolet light called deep UV light. That allows for lower temperatures that save significant heating energy. And because they don’t have to add extra polymer material, fewer resources are involved in the first place.
The researchers employed a light-sensitive resin based on a widely used soft polymer called PDMS, and they don’t have to add silica nanoparticles to their mix like other 3D printing methods. The result is highly transparent glass without the potential optical issues that can arise with the added nanoparticles. The glass lenses they produced were as smooth as commercially made fused silica glass.
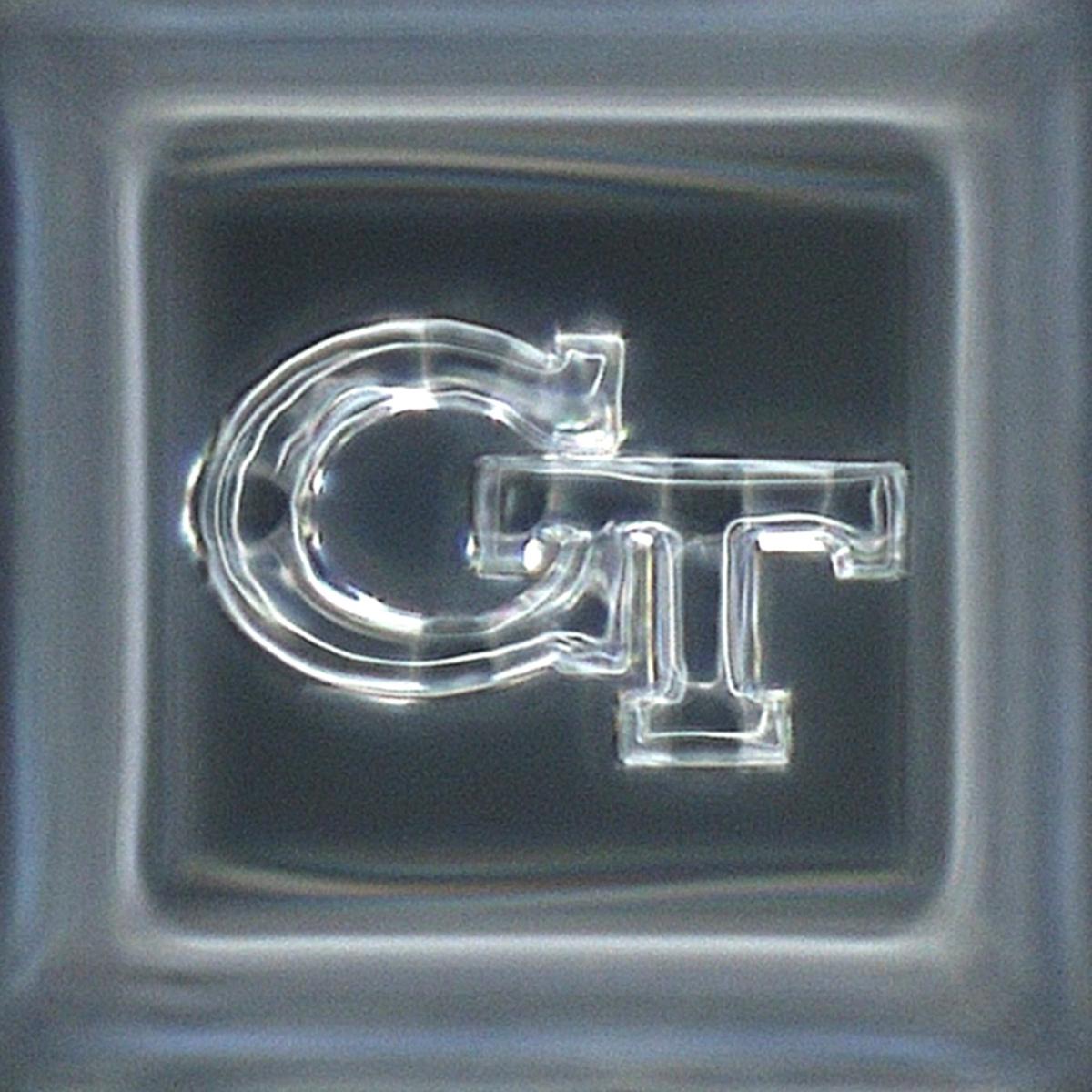
The “GT” logo in glass at only 120 x 80 micrometers.
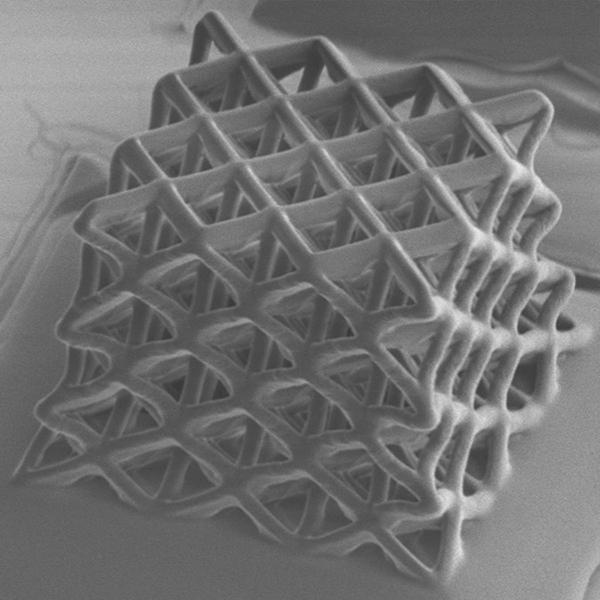
The 3D-printed silica glass can be fabricated in a variety of microstructures.
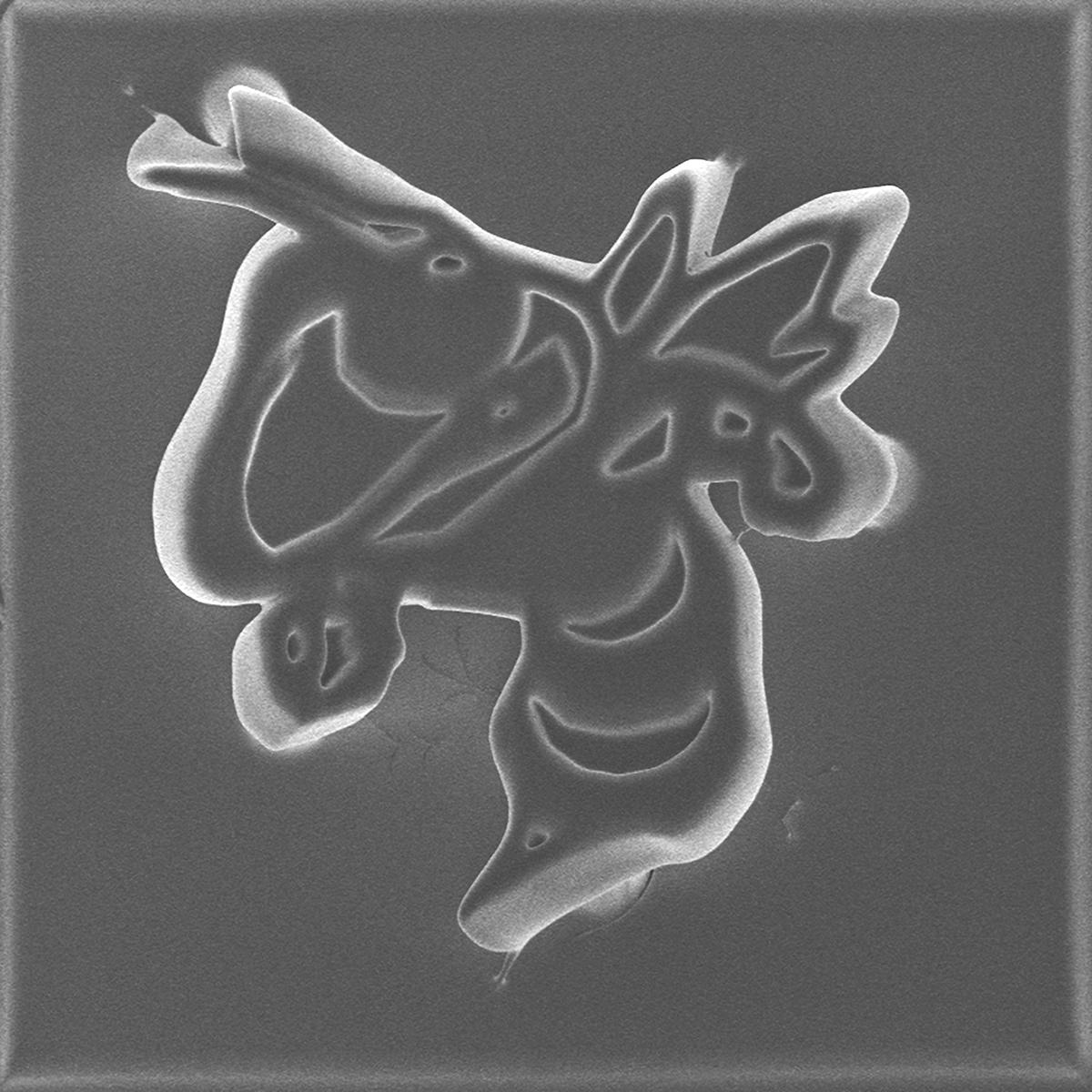
An scanning electron microscope image of silica glass Buzz at 160 x 140 micrometers.
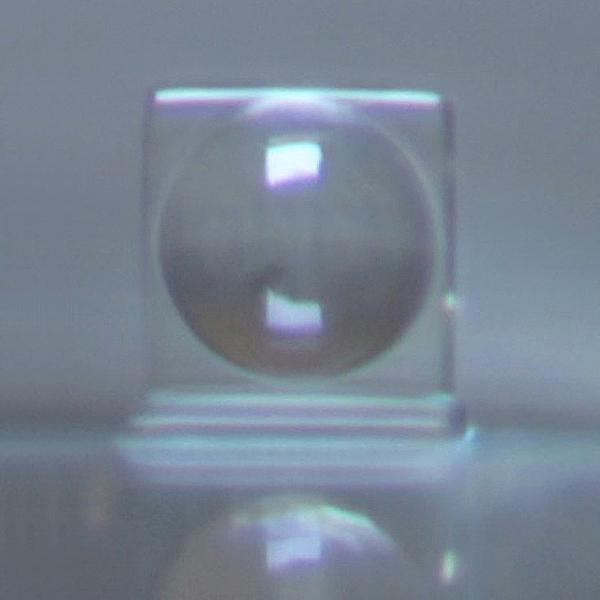
The highly transparent glass can be used for microlenses.
In addition to Qi’s group in the Woodruff School, the research team also included Rampi Ramprasad’s lab in the School of Materials Science and Engineering. Right now, their process creates structures that are 200 – 300 micrometers in size — equivalent to the thickness of a piece of paper or the diameter of a human hair. They’ve started to work on scaling up the glass structures they can 3D print to the millimeter scale.
Qi said advances in 3D printing technology and interest in ceramics — inorganic, nonmetallic materials that are shaped, fired, harden, and become heat- and corrosion-resistant — pushed the group to think about new approaches to their manufacture. And they found a willing partner in the Office of Naval Research, which funded the effort.
“We really want to do the cutting-edge — things nobody has done before in the space of low-temperature conversion of polymers to ceramics within additive manufacturing,” Qi said. “We were encouraged by the Office of Naval Research. They know the risk is high, but they gave us a lot of freedom to try new things.”
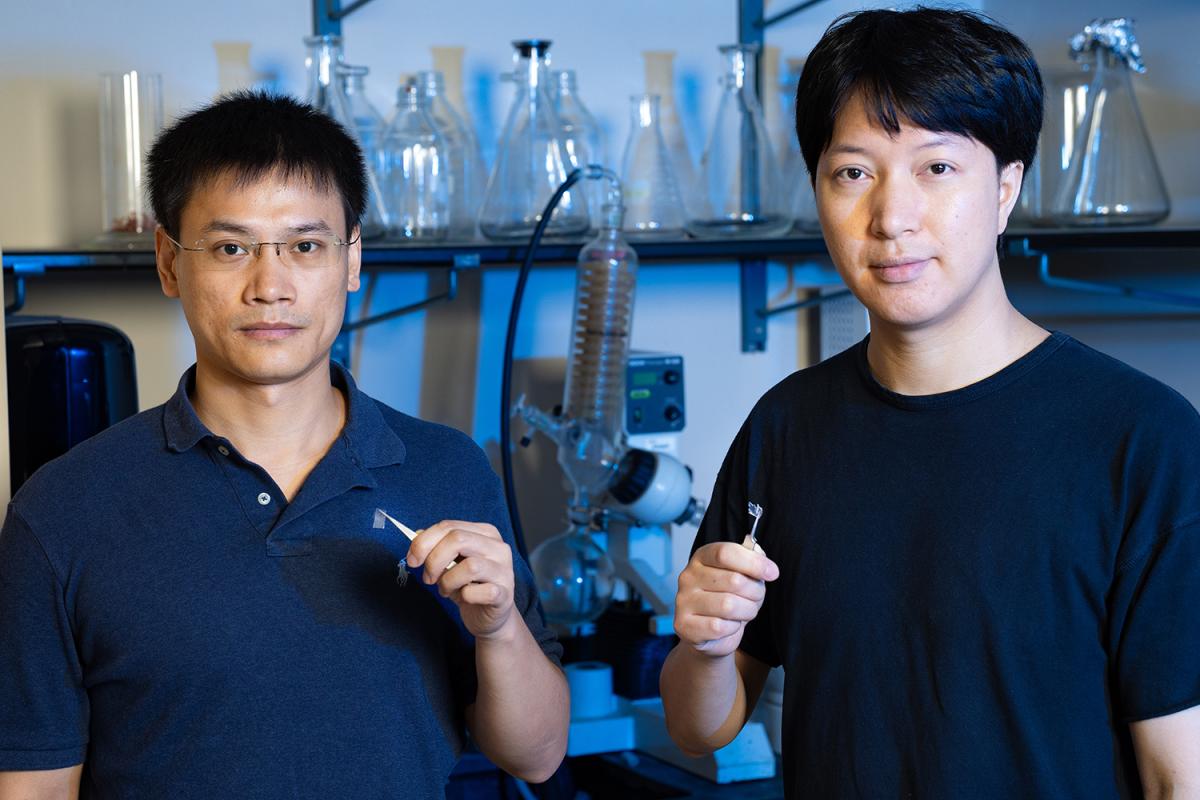
Ph.D. student Mingzhe Li, left, and postdoctoral scholar Liang Yue led development of a process creating 3D-printed glass microstructures using light-sensitive resin based on a widely used soft polymer called PDMS. (Photo: Candler Hobbs)
Related News
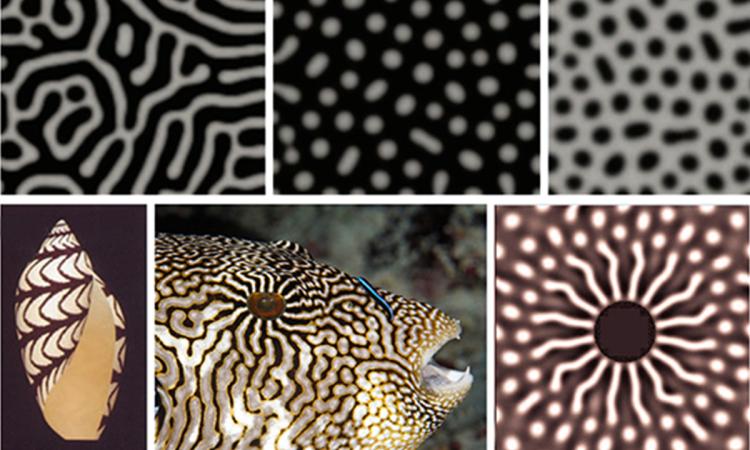
Inflatable Shape Morphing Structures Inspired by Turing Patterns
The findings may offer new concepts for engineering composites and material design.
About the Research
This research was supported by the Office of Naval Research, grant No. N00014-21-1-2258. Any opinions, findings, and conclusions or recommendations expressed in this material are those of the authors and do not necessarily reflect the views of any funding agency.
Citation: Li M., Yue L., Rajan A.C., Yu L., et al. Low temperature 3D printing of transparent silica glass microstructures. Sci. Adv. 9, eadi2958 (2023). https://doi.org/10.1126/sciadv.adi2958
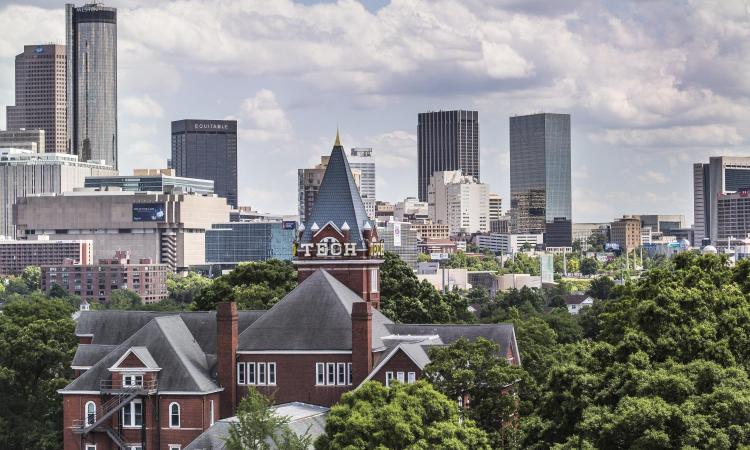
Preeminence in Research
(text and background only visible when logged in)