A team led by Marta Hatzell designed a new electrochemical reactor to seamlessly integrate into direct air capture systems and turn CO2 into useful raw materials.
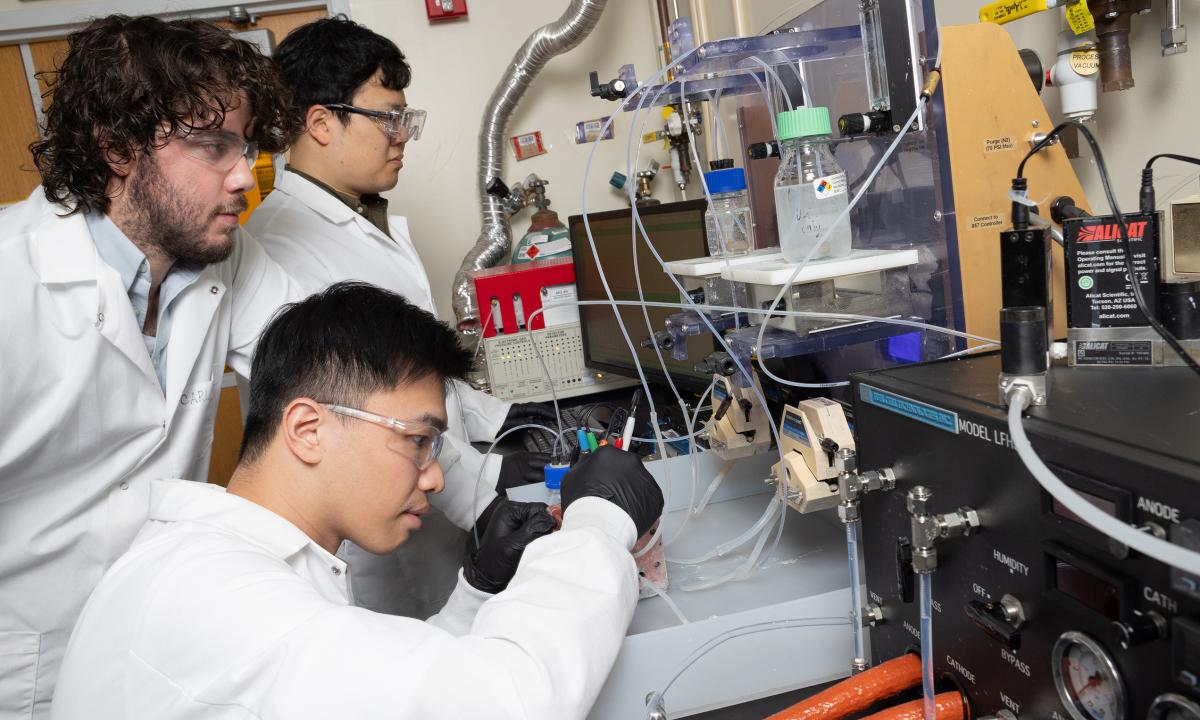
A new electrochemical reactor design developed with Marta Hatzell by postdoctoral scholar Hakhyeon Song (middle) and Ph.D. students Carlos Fernández and Po-Wei Huang (seated) converts carbon dioxide removed from the air into useful raw material. Their approach is cheaper and simpler while requiring less energy, making it a promising tool to improve the economics of direct air capture systems. (Photo: Candler Hobbs)
Engineers at Georgia Tech have designed a process that converts carbon dioxide removed from the air into useful raw material that could be used for new plastics, chemicals, or fuels.
Their approach dramatically reduces the cost and energy required for these direct air capture (DAC) systems, helping improve the economics of a process the researchers said will be critical to addressing climate change.
The key is a new kind of catalyst and electrochemical reactor design that can be easily integrated into existing DAC systems to produce useful carbon monoxide (CO) gas. It’s one of the most efficient such design ever described in scientific literature, according to lead researcher Marta Hatzell and her team. They published details April 16 in Energy and Environmental Science, a top journal for energy-related research.
“All of my team’s research projects focus on decarbonization, which I care about because of climate change, but this one in particular has the opportunity to make an impact and move toward commercialization more quickly,” said Hatzell, associate professor in the George W. Woodruff School of Mechanical Engineering and the School of Chemical and Biomolecular Engineering. “That’s why publishing our work is important, to help get this technology out into the real world.”
Typically, the DAC process involves pulling carbon dioxide out of the air using some kind of chemical or material that wants to grab the CO2 molecules. To release that captured carbon — to store it underground, for example, or process it for productive reuse — requires significant energy and complicated, expensive systems. Along the way, those systems usually lose some of the CO2, often only using half of the carbon they’ve removed from the air or less.
Hatzell’s team is focused on improving an approach that uses a liquid alkaline solution called KOH to capture the carbon in a DAC system. The KOH turns the gas CO2 into bicarbonates, which eventually have to be separated again.
The Georgia Tech design avoids that expensive, energy-intensive step altogether.
Working with Jihun Oh’s lab at the Korea Advanced Institute of Science and Technology, researchers created a new nickel-based catalyst and paired it with a bipolar membrane electrode assembly. Their setup uses electricity to extract CO2 from the bicarbonates right next to the catalyst, which then converts it to carbon monoxide gas.
That’s the secret sauce of the system designed by Hatzell, postdoctoral scholar Hakhyeon Song, and Ph.D. students Carlos Fernández and Po-Wei Huang: It combines two steps into one.
“We're capturing the CO2 into carbonates, which is a spontaneous process and doesn’t take much energy. And we’re getting rid of the desorption process and all of that energy expenditure,” Fernández said. “We save about 90% of the energy in the capture process, and about 50% of the capital cost.”
Their setup also is extremely efficient at using all of the CO2 that moves through the reactor, according to Song. This is vastly better than systems that keep the carbon dioxide as a gas throughout the separation process.
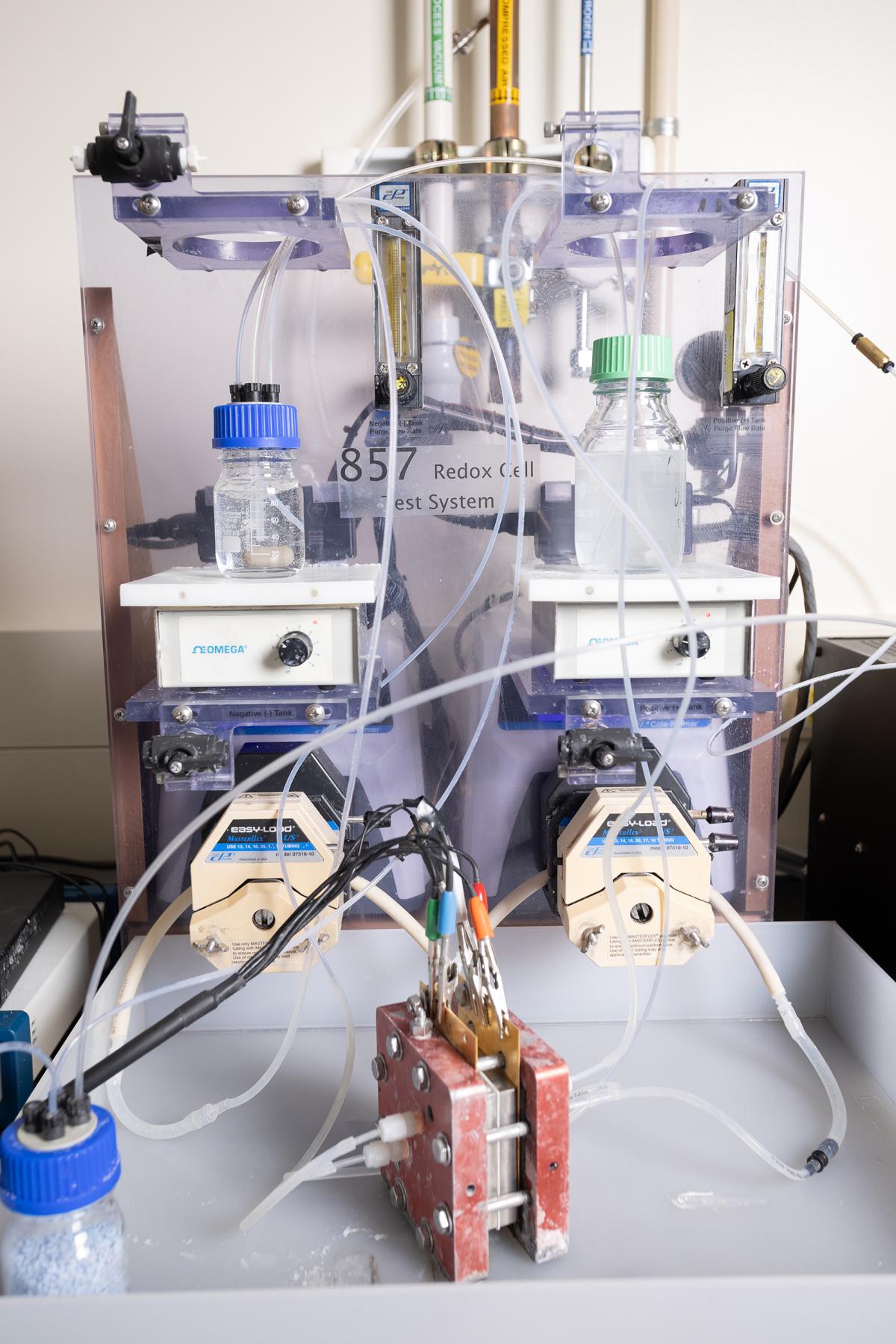
The experimental setup researchers in Marta Hatzell’s lab used to test their new electrochemical reactor for carbon capture. (Photo: Candler Hobbs)
“We’re twice as efficient. Our CO2 utilization efficiency is almost 70%, but the gas-phase system is 35%,” Song said. “The maximum CO2 utilization in gas-based systems is theoretically 50%. But in our case, our maximum efficiency is 100%.”
In another important advance, the team’s catalyst works well in an acidic environment, which has been a limitation of existing systems using bipolar membranes. When the reactor layer with the catalyst turns acidic, another chemical process called a hydrogen evolution reaction occurs that competes with the reaction that reduces CO2 to CO. The new nickel-based catalyst suppresses this interference.
Producing carbon monoxide from the CO2 scrubbed from the air is a complicated, intensive process. But if done economically, the resulting raw material could be linked to existing chemical processes and turned into new useful products.
Making those connections is next on the team’s plate. CO can become the basis for plastics, important industrial chemicals like ethylene, and maybe even jet fuel one day.
“That's why we chose CO,” Fernández said. “Other products are harder to make, and CO is a good base for any carbon chemical. You can go from CO to almost anything through thermochemical processes.”
(text and background only visible when logged in)
About the Research
Citation: Song, H., Fernandez, C. A., Choi, H., Huang, P. W., Oh, J., & Hatzell, M. C. (2024). Integrated carbon capture and CO production from bicarbonates through bipolar membrane electrolysis. Energy & Environmental Science. https://doi.org/10.1039/D4EE00048J
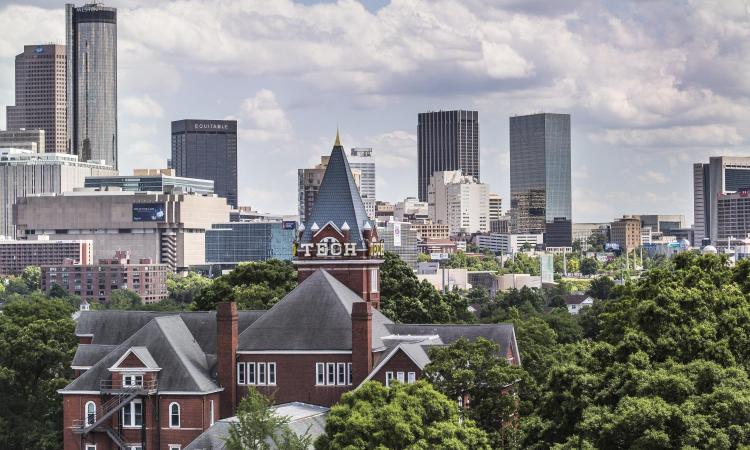
Preeminence in Research
Related Content
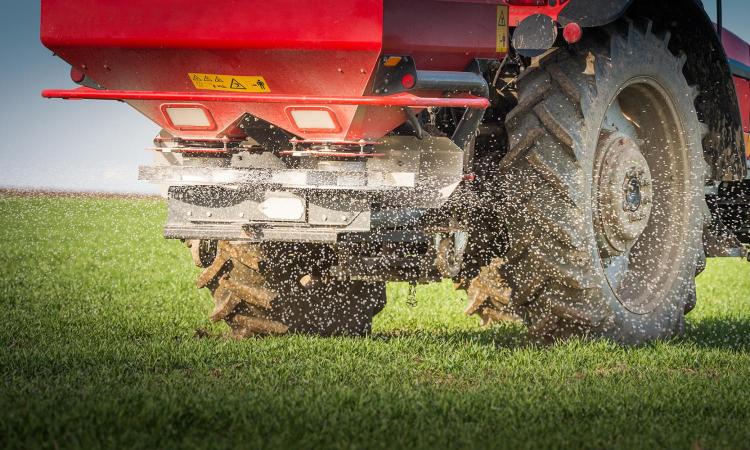
Photochemistry and a New Catalyst Could Make Fertilizer More Sustainable
New insight into the role of carbon in a low-temperature, light-based reaction may help create ammonia for fertilizer while a new catalyst offers a path to recycling the runoff.
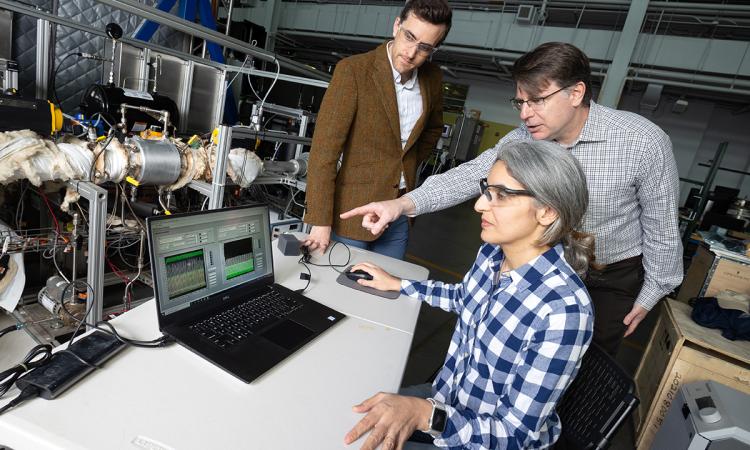
Cutting Emissions Isn’t Enough. We Need to Scrub Carbon Directly from the Air
New Direct Air Capture Center will leverage Georgia Tech’s leadership in a burgeoning field.