Alumna Amanda Nummy is helping move the automotive industry toward more sustainability, from the materials used in vehicles to recycling cars and trucks after they come off the road.
(text and background only visible when logged in)
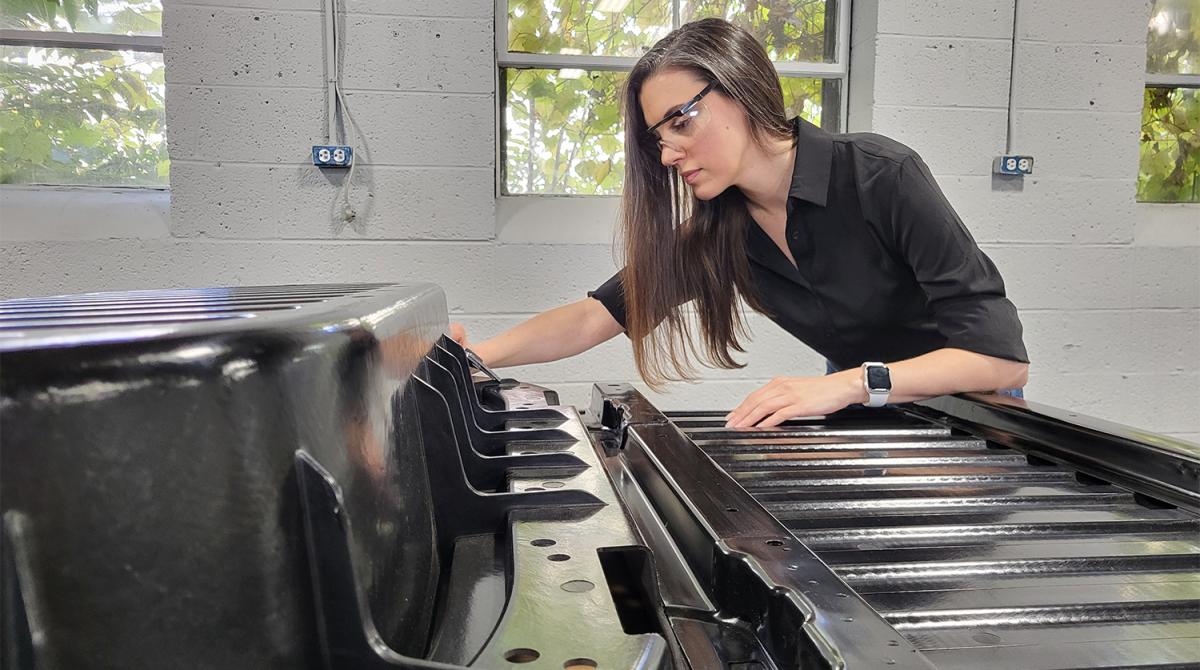
One of Amanda Nummy’s projects is a polymer composite for a truck bed that is thinner and just as durable as traditional materials. (Photo courtesy: Amanda Nummy)
(text and background only visible when logged in)
Something clicked for Amanda Nummy early in her first semester at Georgia Tech.
She was sitting in an engineering exploration course because she was undecided on a specific engineering discipline. On that fateful day, a representative from the School of Materials Science and Engineering was explaining their field, providing a show-and-tell of sample materials researchers and students had developed.
Seeing those tangible pieces, designed for uses in medicine, aerospace, and more, was revelatory for Nummy.
“It sparked the idea that materials are everywhere,” she recalled. “I thought, ‘If I get a degree in materials, I can do anything I want to do. I can get close to whatever industry I want.’”
More than a decade and a half later, that industry is vehicle design and manufacturing, where Nummy has become a leader in finding ways to make more sustainable cars and trucks.
That can mean working to incorporate more durable plastic polymers into vehicles to make them lighter and less expensive. It can mean helping her company, Hyundai Motor Group, design vehicles for recyclability at the end of their lives. Or it can mean finding ways to turn plastic waste in our oceans into new plastic for car parts.
“I’ve always felt that plastic, specifically, kind of got a bad reputation, and that there is an opportunity for appropriate and responsible use of plastics,” said Nummy, who earned her polymer, textile, and fiber engineering bachelor’s degree in 2011. “That’s been a focus for me: How do we use these materials in a way that is beneficial rather than detrimental and pursue a mindset shift around how we select and design with materials.”
From Bottle to Bumper?
In many ways, Nummy was ahead of the curve, making the business case for sustainability in the years before many carmakers adopted commitments around environmental sustainability.
As a senior polymer engineer for Hyundai and Kia, she is charged with finding and developing materials to meet the performance needs of designers and engineers while balancing the cost demands of the purchasing department. She has worked extensively on plastics for vehicle exteriors and powertrains, but responsibility for all the plastic components for vehicles in North and South America essentially falls under her purview.
“I really try to emphasize that sustainability and efficiency can go hand in hand,” Nummy said. “You can have material reduction, which often means cost reduction, waste reduction, weight reduction, and processing improvements. Translating those sustainability aspects into metrics that are relevant to the business is where I’ve had luck moving projects forward.”
One project is converting plastic waste collected along the coastline into recycled plastic pellets formulated specifically for use in vehicle parts. She partnered with a company in Costa Rica that collects and processes the waste.
Their collaboration resulted in a high-density polyethylene automotive plastic with a double-digit percentage of recycled content that met performance requirements and wasn’t prohibitively expensive. Originally, that material was targeted for a cooling pipe in electric vehicles, but Nummy said it also could be used for exterior pieces or even door trim components.
Her Costa Rican partners also collect significant amounts of the plastic often found in water bottles and can turn that into a textile. She’s pitching an interior component that would use the hard plastic she formulated with the recycled textile on top. The team also is looking at blending two different kinds of plastic materials for new applications.
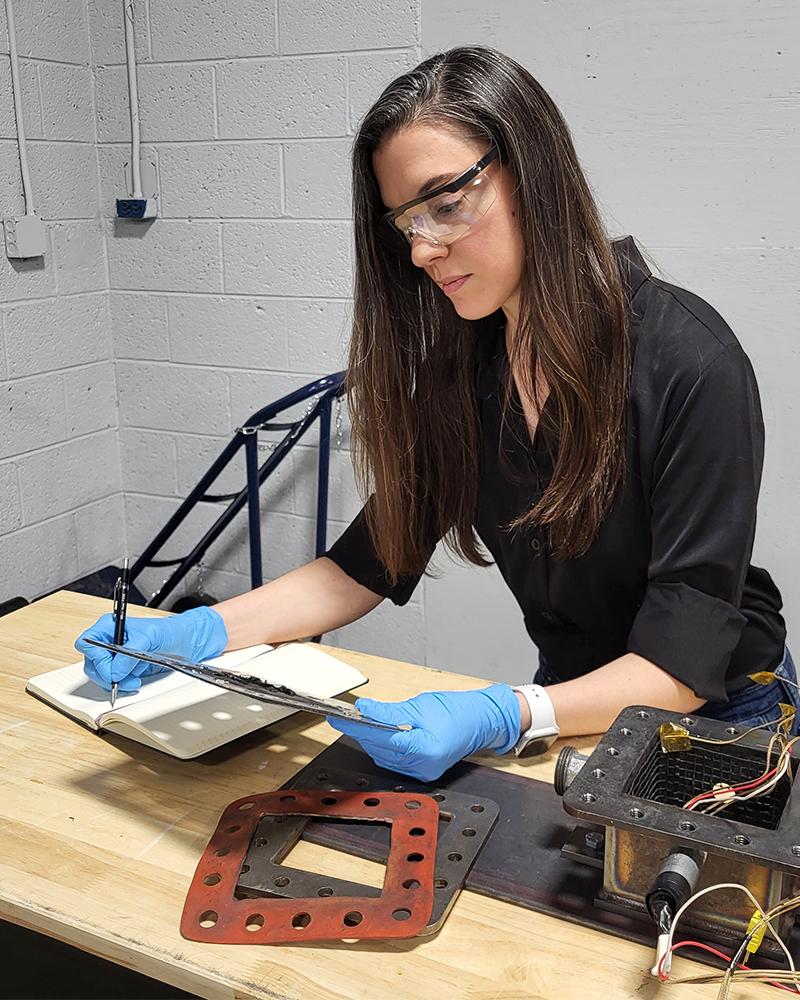
Amanda Nummy examines polymeric battery enclosure materials after flammability testing. (Photo courtesy: Amanda Nummy)
In another project, Nummy explored recycling used personal protective equipment from healthcare and research settings. The idea was to turn face masks collecting in landfills or becoming litter into a useful new material. Again, the driver was waste ending up where it shouldn’t be and Nummy’s desire to create secondary value to short-circuit that cycle.
“In my opinion, there’s no such thing as an unrecyclable material,” she said. “There are just materials that are traditionally not dealt with in standard recycling processing.”
Sustainable from the Beginning
Vehicle sustainability also can take the form of designing new materials to reduce weight, require less material in the first place, and shrink the manufacturing and processing footprint. That means extended range for the vehicles and less impact on the environment from the very beginning.
Nummy’s efforts have included developing a polymer composite for the open bed of a new sport adventure vehicle. It’s thinner and just as durable as typical truck bed materials. A similar project is creating a polymer composite enclosure for electric vehicle batteries. Usually made of metal, these components have to withstand rigorous testing for flammability and durability.
“Both the truck bed and the battery enclosure came from this idea to do a holistic design up front,” Nummy said. “If we had a blank sheet of paper, and we wanted to balance the weight, the cost, the quality, and the sustainability, how would we do that? We looked at material, processing, and design options, and came up with an optimized version of those designs.”
As part of the battery project, Nummy also developed a new testing standard published by Underwriters Laboratory. Instead of investing hundreds of thousands of dollars to design and produce prototype enclosures with new materials — costs that include creating the necessary tooling and production processes — she led creation of a scaled-down version of a key flammability test that allows engineers to design and test new enclosure materials quickly and less wastefully.
“When we move to a plastic from conventional metal, there can be lower processing energy initially, and lower processing energy again through the recycling step. There’s a full lifecycle sustainability story there that we don’t often talk about,” Nummy said.
She’s working on that recycling step at the other end of the vehicle lifecycle too, exploring how to reclaim plastic from automotive shredders. The hope is to recover plastic at a molecular level and turn it into in new plastics for new cars.
A key part of Nummy’s approach to boosting use of new materials is flipping the traditional way automotive design happens. Instead of standing by for engineers and designers to come to the materials team with a need or working in a silo, she likes to present the design team with new materials to see how they can use them.
“I have tended to look at the material as the enabler of a design or technology. I do a lot of qualification and validation upfront to understand how these materials perform, and then take that data to the broader cross-functional teams and say, ‘Here’s what this material can do. Let’s figure out a way this fits into the functional challenges we’re trying to solve on a vehicle.’”
(text and background only visible when logged in)
(text and background only visible when logged in)
Related Stories
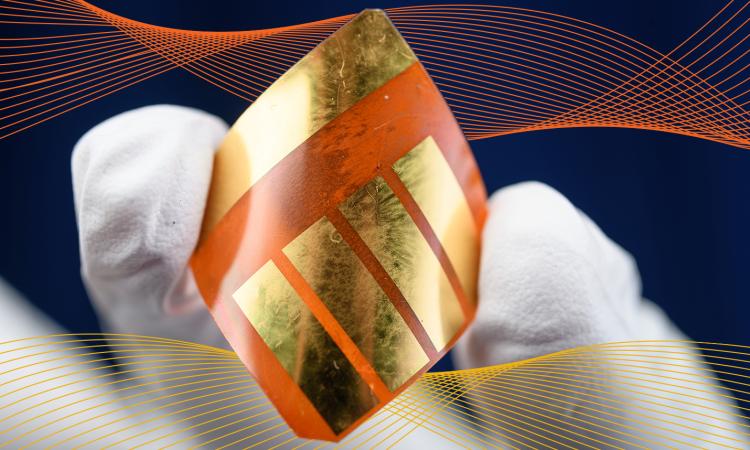
Powering Up
Our researchers are creating new technologies that pollute less and store more energy — while also ensuring the manufacturing process is clean.
(text and background only visible when logged in)
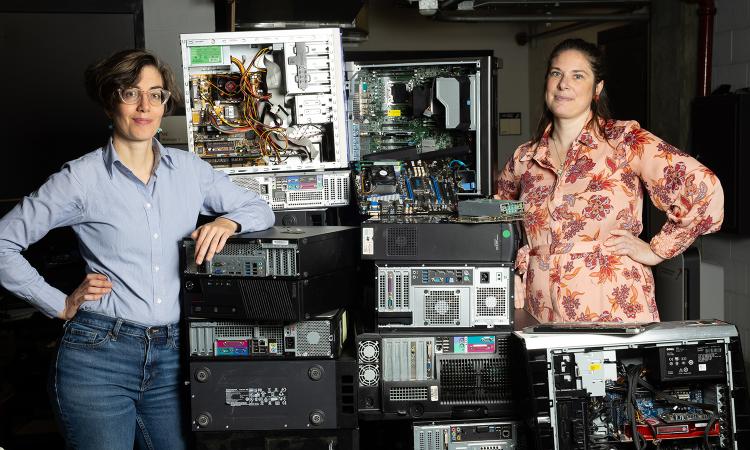
To Hell with Garbage
In the quest to reduce, reuse, and recycle, Georgia Tech engineers are at work on ways to divert more trash from landfills, tame plastic pollution, and cut waste from electronics.
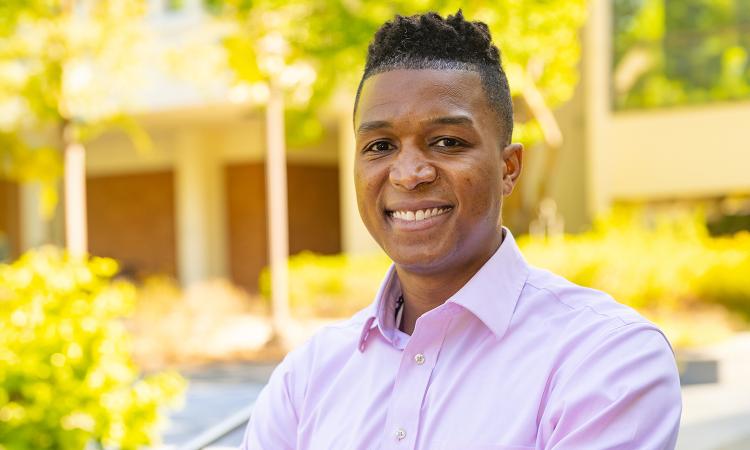
Why Equitable Sustainability Matters
Growing up in a Midwestern inner city led Joe Bozeman to a career understanding how sustainability takes shape for people of many different backgrounds.
(text and background only visible when logged in)
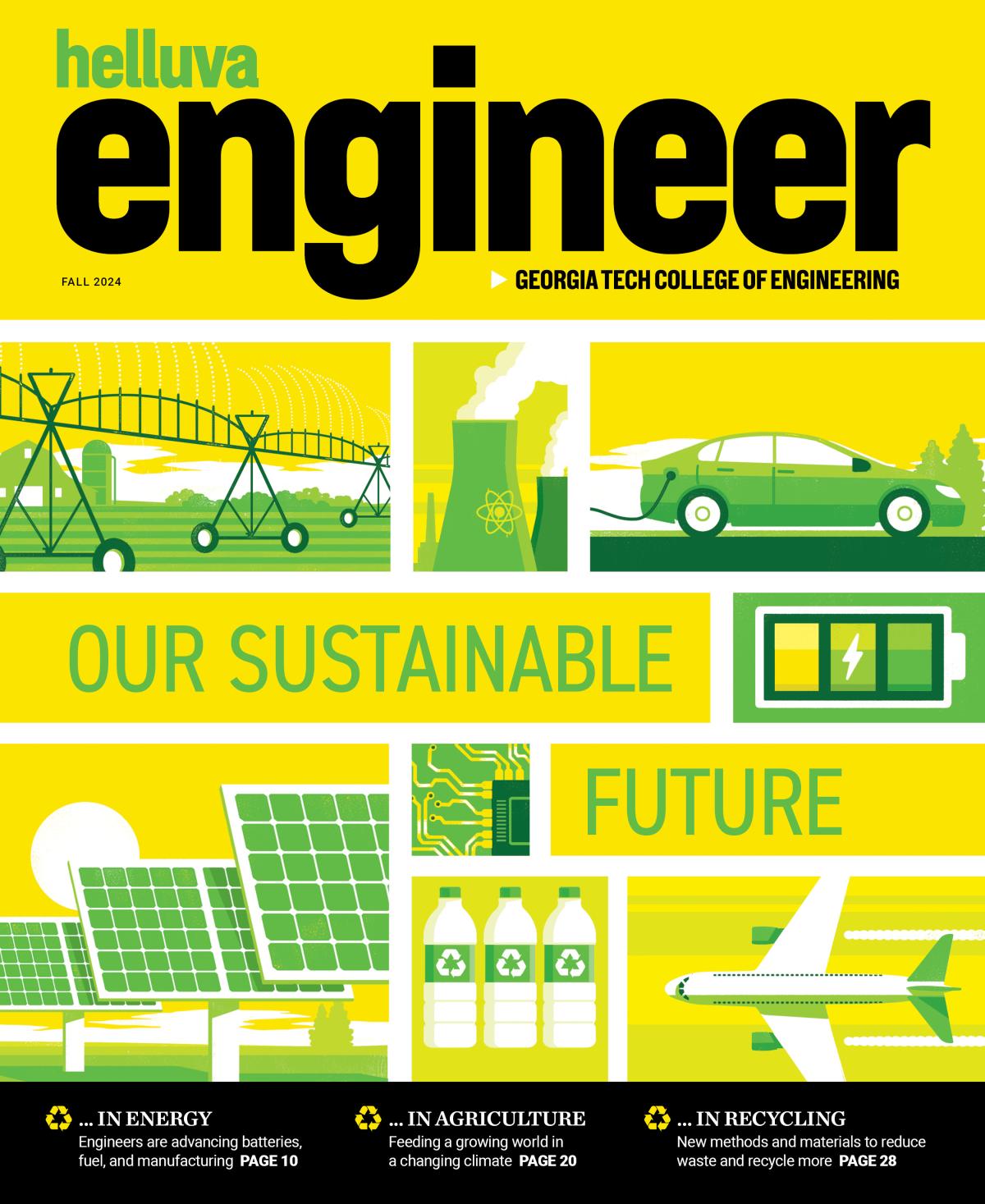
Helluva Engineer
This story originally appeared in the Fall 2024 issue of Helluva Engineer magazine.
In a world with more people, more energy needs, and more waste than ever, Georgia Tech engineers are hard at work developing the tools and technology for everyone to thrive. We’re diverting trash from landfills and taming plastic pollution (while finding alternatives to plastic in the first place). We're reducing the environmental impact of agriculture and finding new ways to fertilize the fields growing food for a growing world. And engineers are powering up the batteries, fuels, and renewable sources to meet surging energy demand. The future is coming; we're making it more sustainable.