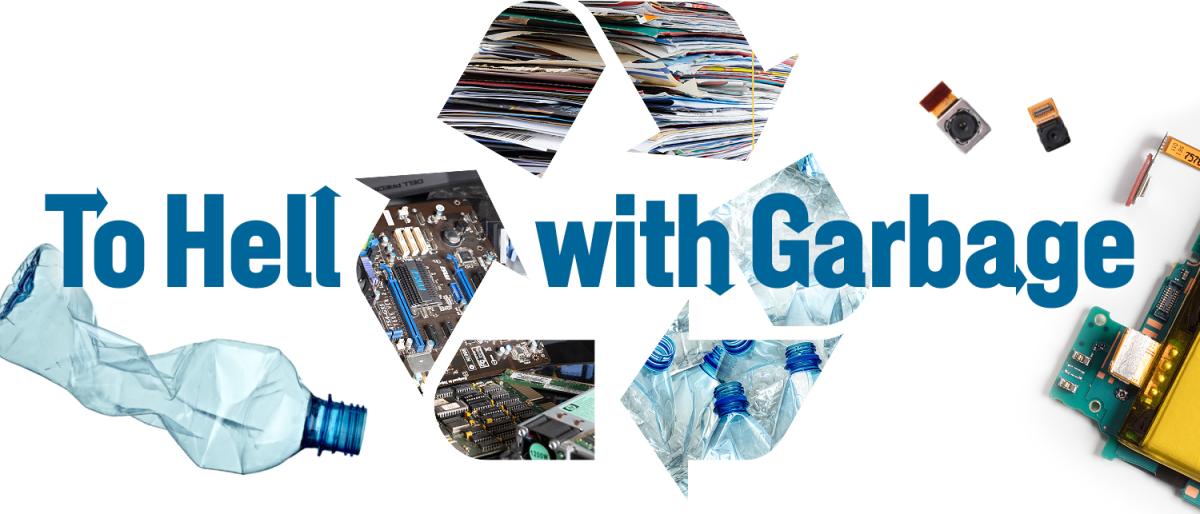
In the quest to reduce, reuse, and recycle, Georgia Tech engineers are at work on ways to divert more trash from landfills, tame plastic pollution, and cut waste from electronics.
(text and background only visible when logged in)
For decades, we’ve been conditioned to look for that little triangle of arrows and taught the mantra “reduce, reuse, recycle.”
And for good reason: The U.S. Environmental Protection Agency estimates each American produces about 5 pounds of trash every day. Nearly 70% goes straight to a landfill as municipal solid waste.
Paper. Plastics. Clothes. Leftover food. Just 32% of that waste is recycled or composted. Mostly, that’s paper, of which nearly two-thirds is recycled in some way.
Georgia Tech engineers are working to improve those statistics and make a cleaner, less wasteful future for our communities. Their efforts are aimed at reducing how much waste people generate in the first place and imagining ways to recycle more of what’s left.
In their labs, they’re designing processes to transform discarded plastic into raw material for new products. They’re creating new kinds of plastic from biological material to vastly reduce plastic pollution. They’re developing systems to eliminate emissions and cut water use in the carbon-intensive papermaking industry. They’re also addressing one of the newest trash problems in our digital age: electronic waste.
In the three R’s of sustainable behavior, “recycle” comes after admonitions to reduce what we consume in the first place and then reuse what we can. That may be because recycling is the hardest to do, and it’s often not economical, even when processes exist to do it. Work at Georgia Tech and by its alumni won’t rearrange the R’s, but it may well reshape how we deal with our trash.
(text and background only visible when logged in)
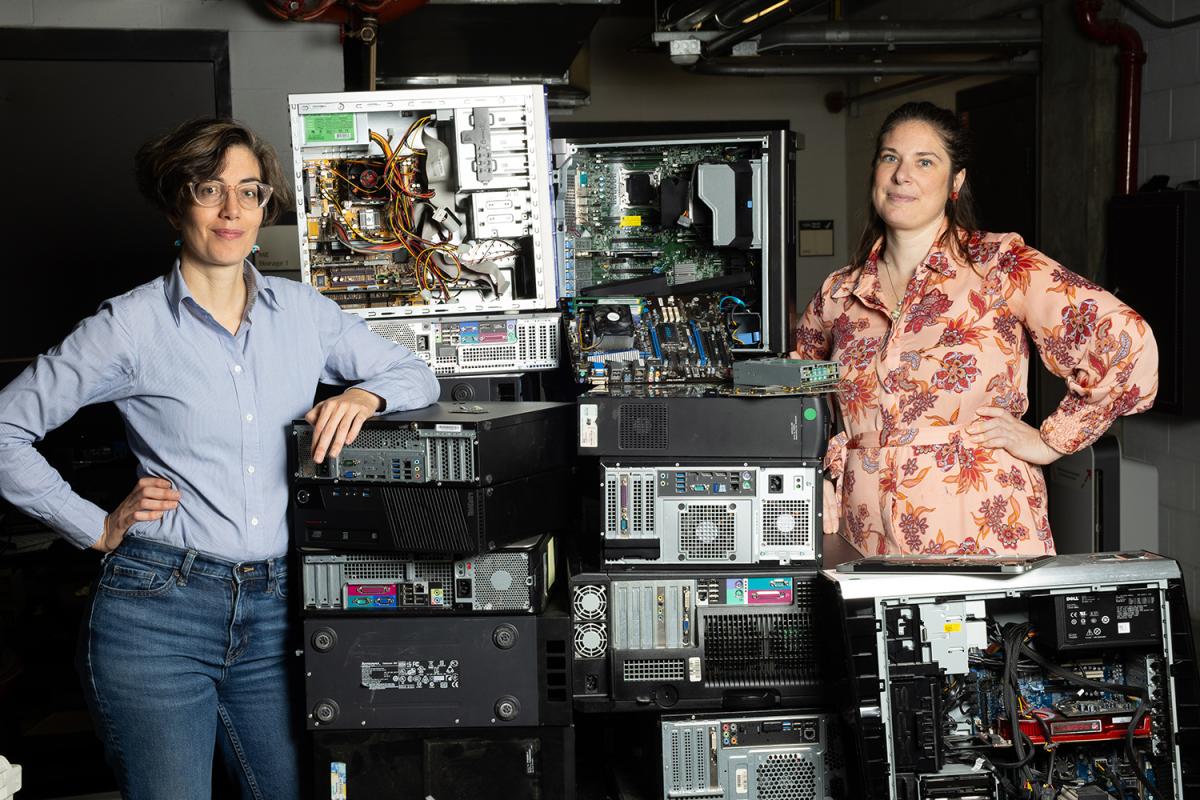
Antonia Antoniou (left) and Vanessa Smet are working to advance electronics performance and sustainability. (Photo: Candler Hobbs)
Working From Behind in Race Against E-Waste
The World Health Organization estimated in 2022 that nearly 62 million tons of waste from electronics is created every year. Only 22% is collected and recycled.
It’s not a surprise to Antonia Antoniou and Vanessa Smet, faculty members and collaborators in the George W. Woodruff School of Mechanical Engineering.
Their research focuses on improving electronic packaging for better performance, while also tying that innovation to sustainable fabrication and recyclability. They’re looking at new, more sustainable ways to assemble and connect components of electronic systems such as active chips, resistors, and capacitors, both to each other and to their surroundings.
They know that they’re working from behind.
“Packaging was typically an afterthought until about 10-15 years ago,” said Smet, an assistant professor and expert in electronics packing. “The main focus was the chip’s performance. Although a chip by itself is obsolete without being powered and able to communicate with other critical system components, everything related to its integration has been treated as a necessary evil.”
That’s a problem, Smet said, because many of the materials involved in creating these integration platforms, such as thermoset polymers with reinforcing fibers, copper, and other metals, don’t degrade or are dangerous when they breakdown in landfills.
It’s one reason why Antoniou called packaging the “next driver of innovation for high performance electronics.” It’s an interdisciplinary field, with mechanical engineers teaming with experts in materials science, electrical engineering, and manufacturing.
Antoniou works on the mechanics side of electronics packaging, figuring out how to design materials and their mechanical properties, and how to keep them from failing. Smet is more of a generalist: She has an applied physics background and looks at packaging as a science to develop comprehensive solutions that jointly advance electronics performance, reliability, and sustainability. She aims to transform that knowledge into new materials and industry-scalable manufacturing practices.
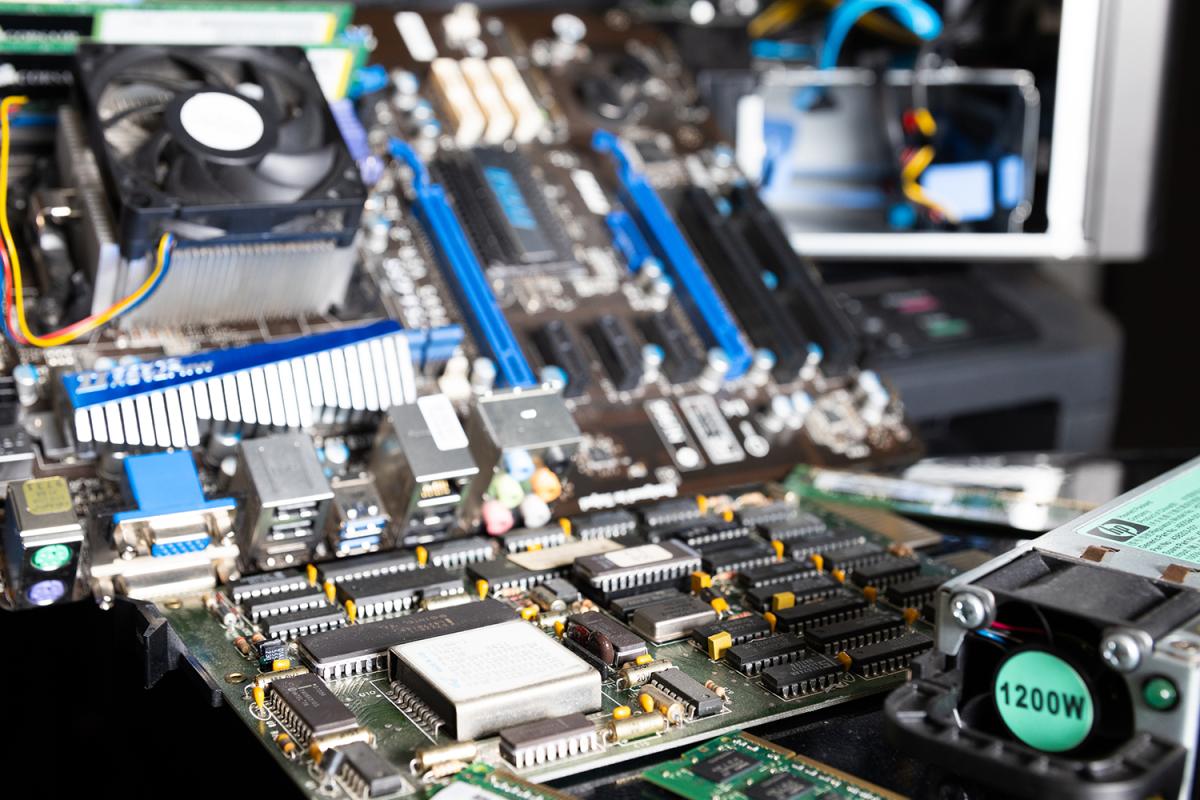
Many electronics materials don’t degrade or are dangerous when they break down. (Photo: Candler Hobbs)
Smet said packaging is coming to the forefront now because of the continuing rise in demand for better performing electronics and the scarcity and expense of the materials used to make them.
“Think about short-term electronics, like phones, that we may keep for just two to three years before throwing away,” Smet said. “There are materials in them that are beneficial to recover, like gold and copper. At the same time, our field is also looking to create sustainable practices to ensure that the manufacturing of electronics is cleaner.”
One idea born out of Georgia Tech labs nearly 20 years ago was using glass substrates, instead of silicon, on computer chips. The technology now is used by companies in Georgia, at Intel, and around the world. Another example Smet pointed to is the switch from copper packaging to recyclable aluminum and graphene, which allows for a cleaner manufacturing process. The key, she said, is making sure new components allow for the same, or increased, signal and power efficiency and reliability than the materials used for decades.
“Electronics are in everything,” Antoniou said. “The process to make them must be cleaner. If we don’t break the waste cycle soon, we’ll be in even bigger trouble than we are now. It’s becoming more urgent as time goes by, and industry must do more sustainable packaging for electronics recycling and end-of-life.”
(text and background only visible when logged in)
(text and background only visible when logged in)
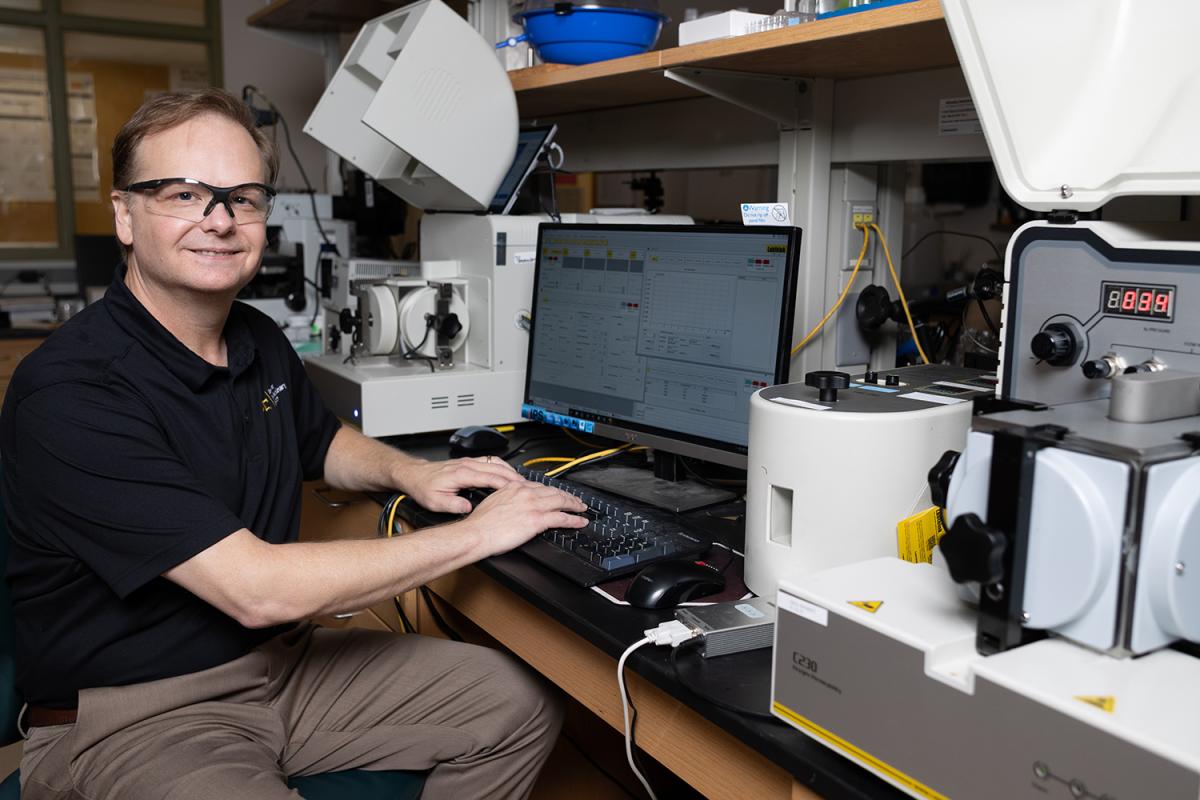
Carson Meredith is a 1993 Georgia Tech chemical engineering graduate. (Photo: Candler Hobbs)
Lowering Barriers for Sustainable Packaging
Carson Meredith’s group in the School of Chemical and Biomolecular Engineering (ChBE) is focused on a different kind of sustainable packaging: advanced barrier packaging.
It’s a fancy name, but it’s simply the plastic packaging most of us encounter every day with food and medicines. They’re a staple in supermarkets: pouches for deli meat and cheeses, the see-through wrappings that cover steak and ground beef, and vacuum-sealed food bags, to name a few.
By providing a barrier to oxygen and water vapor, the plastic wraps extend shelf life by days, weeks, even years. Ironically, the wraps themselves have a very short lifespan.
Unlike simple plastic grocery bags that can be recycled, the barrier wraps are more complex, making them one-and-done single-use materials. They’re made up of several different types of plastics layered into a single film. And that, Meredith said, makes it too difficult and expensive for recycling. It’s why he and his collaborators are searching for new technologies and processes to change the materials’ chemistry and make them more environmentally friendly.
“The amount of plastics in our oceans is certainly upsetting and gets people mobilized. And that social awareness is good,” said Meredith, professor and James Preston Harris Faculty Fellow. “But the bigger sustainability problem is the large carbon footprint of constantly remanufacturing these single-use plastics with fossil fuel-based feedstocks instead of finding ways to reuse their carbon.”
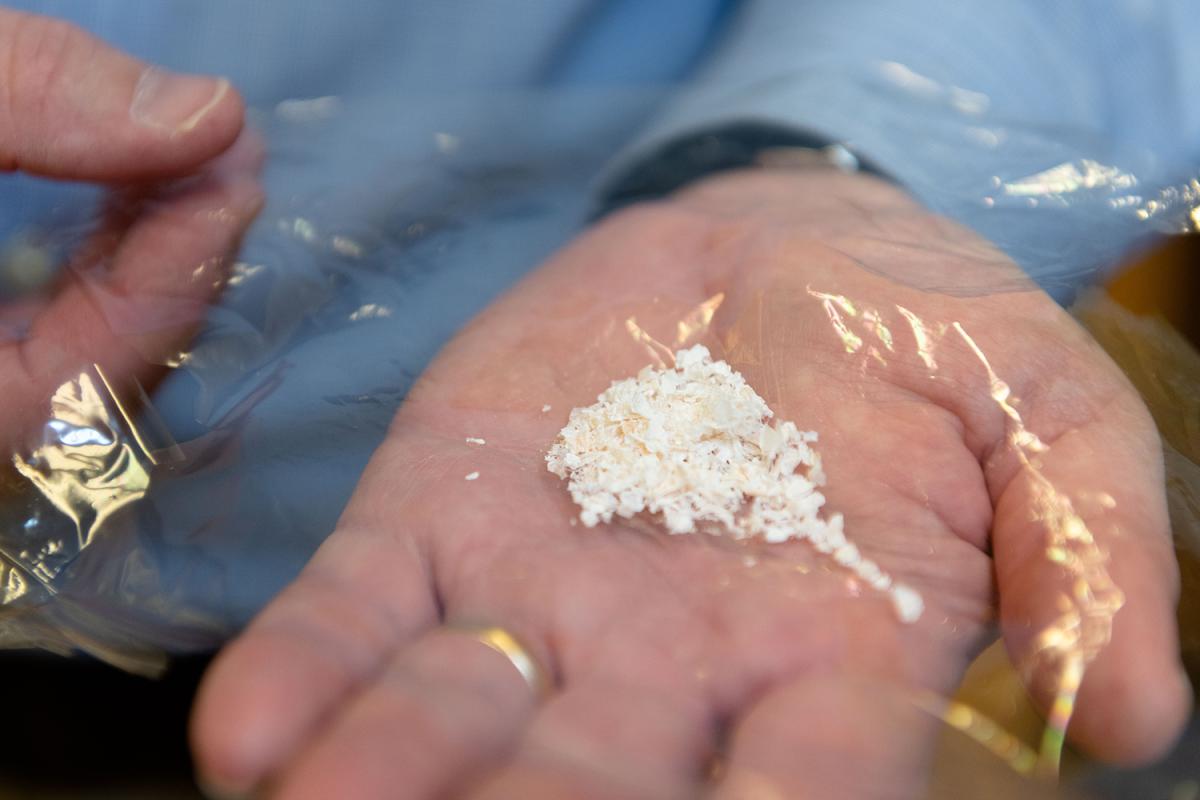
Meredith has created materials made with crustacean byproducts as a more sustainable alternative to traditional plastic packaging. (Photo: Allison Carter)
Meredith and his collaborators have pioneered renewable, biodegradable, and recyclable barrier materials that can serve as alternatives to the familiar synthetic plastic barriers. About a dozen years ago, long before he was tapped as executive director of Georgia Tech’s Renewable Bioproducts Institute (RBI), Meredith received RBI funding to explore whether plant-derived materials could be used for advanced barrier packaging.
He found that blending cellulose nanomaterials with chitin nanofibers — carbohydrates found in the cell walls of mushrooms or crustacean food waste — is effective at generating the oxygen and carbon dioxide barriers important in packaging. These renewable resources have become a main focus of his lab and led to numerous collaborations funded by the Department of Energy (DOE) and industry partners. These materials can even be coated onto paper to transform it into a gas barrier, a major focus of his group’s work. Using paper as the base material is attractive because it is derived from a renewable resource and it is recycled at rates exceeding 70%.
Meredith also is looking at making paper packaging more sustainable. It’s a burgeoning field because of the convenience and popularity of online shopping and shipping.
“In North America ‘working forests’ that produce wood for paper are required by law to replant harvested trees. They usually do so at a rate higher than they are cut, so it is a sustainable resource,” Meredith said. “However, the carbon footprint of making paper is still fairly high, especially in mills that make it from recycled products.”
When a mill makes “virgin” paper from trees, Meredith said, they use lignin derived from the wood as a biofuel to create heat for drying purposes. It’s a circular system: the bio-based carbon emitted during combustion is absorbed by growing more trees. But mills that make paper from recyclables often don’t have the convenient lignin biofuel available. They must find their own fuel — very often natural gas — to dry paper and paperboard products.
“Producing paper requires hundreds of kilograms of water for 1 kilogram of dry product. Evaporating that water is tremendously energy intensive. Our lab is trying to de-fossilize the generation of heat in the production of paper and paper packaging to minimize the carbon footprint,” Meredith said.
One way they’re doing that is by developing a papermaking machine that produces zero carbon dioxide emissions. The device is part of a new $3.1 million DOE award with the Woodruff School’s Cyrus Aidun and RBI’s Patricia Stathatou, who will join the ChBE faculty in January 2025. The development makes use of Aidun’s multiphase forming process being installed as a pilot facility at RBI, which replaces about 50% of the water with air bubbles for paper forming. The remaining water is to be dried with electrified inductive and infrared heating that could be supplied by renewable or clean electricity.
“If you don’t need as much water to form the paper, you don’t have to remove as much water later. So the process ends up saving a lot of energy and reduces greenhouse gas emissions,” Meredith said.
In another interdisciplinary project with Victor Breedveld (ChBE), Blair Brettmann (ChBE/School of Materials Science and Engineering), Chris Luettgen (RBI/ChBE), Scott Sinquefield (RBI), and Valerie Thomas (H. Milton Stewart School of Industrial Systems and Engineering), the team is improving mechanical dewatering steps that remove water without heat.
“The public recycles the majority of used paper, and industry has an established process for using recycled material. The last hurdle is reducing its carbon footprint,” Meredith said. “I’m proud that Georgia Tech is leading the nation in innovative ways to do that.”
(text and background only visible when logged in)
(text and background only visible when logged in)
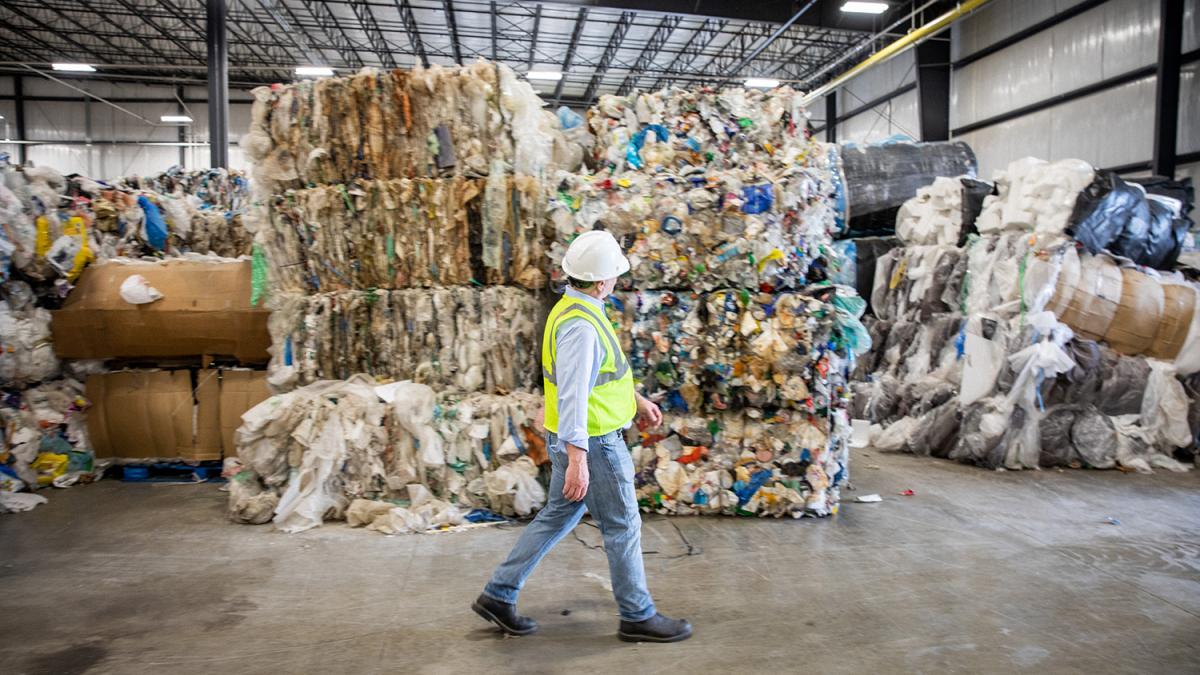
Alumnus Bob Powell walks in front of bales of plastic to be recycled at Brightmark’s circularity center in Ashley, Indiana. (Photo courtesy: Brightmark)
Closing the Circle to Recycle Plastics, Organic Waste
Bob Powell’s career in sustainability began as a 5-year-old child in his grandmother’s garden when she warned him about spreading too many pesticides on her tomato plants.
“She told me that rain would take the pesticides into the creek, which flowed into the river, which fed into the Gulf of Mexico. She said the chemicals would harm fish and animals,” Powell remembered. “That’s when I first realized people and waste can have a negative impact on our world.”
Powell would later attend Georgia Tech and earn his electrical engineering degree in 1988, followed by a master’s degree in management in 1990 from what’s now the Scheller College of Business. An education filled with microelectronics and business skills took him around the world and equipped him to take leadership positions at gas and electric companies. He often played a main role in acquiring other companies.
His job eventually brought him to Jakarta, Indonesia in 1995, where another 5-year-old boy refocused him on sustainability.
“I looked out my window as we drove through a neighborhood and saw a child running in the night, leaping over open sewers,” Powell said. “It made me think about my 5-year-old son at home.”
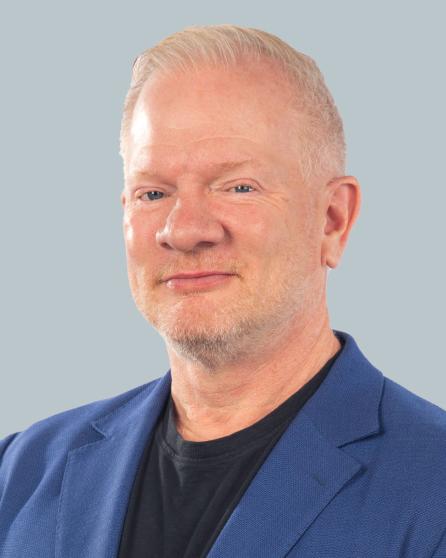
Bob Powell
That image, framed by a taxicab window, triggered a flood of thoughts about waste and its effect on children. Powell had spent his career involved in wind and solar energy, gas, and the electric grid. But deep down, he knew that others in those fields could have a grander impact than he ever would. With memories of his grandmother and the boy in Indonesia, he shifted his full focus toward waste and how to eliminate it worldwide.
In 2016, he founded a company called Brightmark that uses circular innovations to recycle plastics and organic waste.
“Our company wasn’t founded on technology. It was founded on a mission: reimagining waste,” said Powell, Brightmark’s CEO and president. “Our goal is to look at the waste we create and to eliminate it to create fewer environmental impacts.”
Brightmark has built more than 30 circularity centers nationwide to address cow manure and other organic sources of greenhouse gases and partnered with dairy farmers, waste management companies, and food processors. The centers store the manure in anaerobic digesters, capturing its methane and converting it into renewable natural gas. The remaining solids created by the anerobic digestion technology are turned into fertilizer and compost. Excess water is returned to the farm or transported to nearby water treatment facilities.
To address plastic waste, Powell’s company processes discarded plastic, then dries, shreds, and compresses it into small pellets. The pellets are heated using a patented pyrolysis process where the plastic chemically breaks down when exposed to high temperatures in an oxygen-starved environment. Released vapor is captured and cooled into a liquid, then processed into pyrolysis oil that is sent to customers as building blocks for new plastic products. To date, Brightmark has recycled nearly 6 million pounds of plastic waste.
Though his career has been spent building, acquiring, and starting businesses, Powell said being trained as an engineer at Georgia Tech continues to benefit him 36 years after receiving his degree.
“The foundation Georgia Tech provided serves me well, especially when chemistry, thermodynamics, and Boyle’s Law come up at our centers,” he said.
“More than anything, I’m thankful for Tech teaching me about intuition and thinking differently about ways to solve problems.
“We’re trying to solve a global issue — one that is bigger than Brightmark. I’m proud to be part of a movement that is improving our amazing Earth.”
(text and background only visible when logged in)
(text and background only visible when logged in)
Related Stories
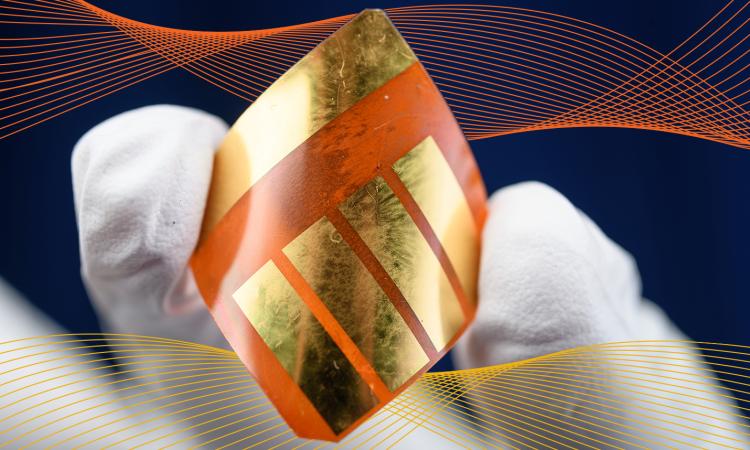
Powering Up
Our researchers are creating new technologies that pollute less and store more energy — while also ensuring the manufacturing process is clean.
(text and background only visible when logged in)
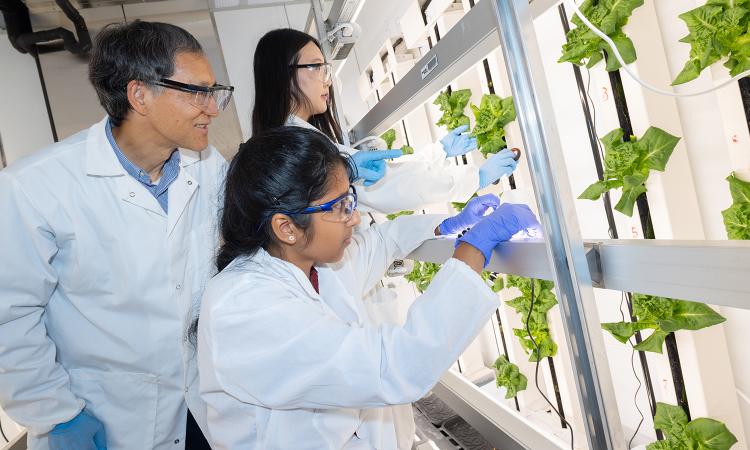
Planting the Seeds of the Farm of the Future
Georgia Tech engineers are working to reduce the environmental impact of farming while creating technologies to help farmers feed a growing world and adapt to a changing climate.
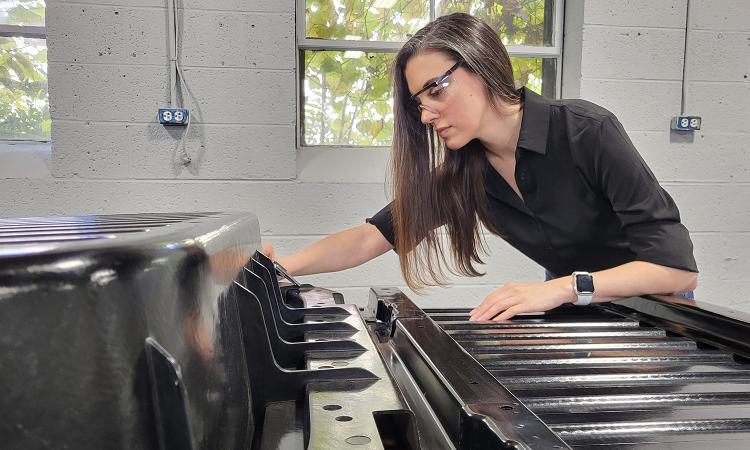
Driving Change
Alumna Amanda Nummy is helping move the automotive industry toward more sustainability, from the materials used in vehicles to recycling cars and trucks after they come off the road.
(text and background only visible when logged in)
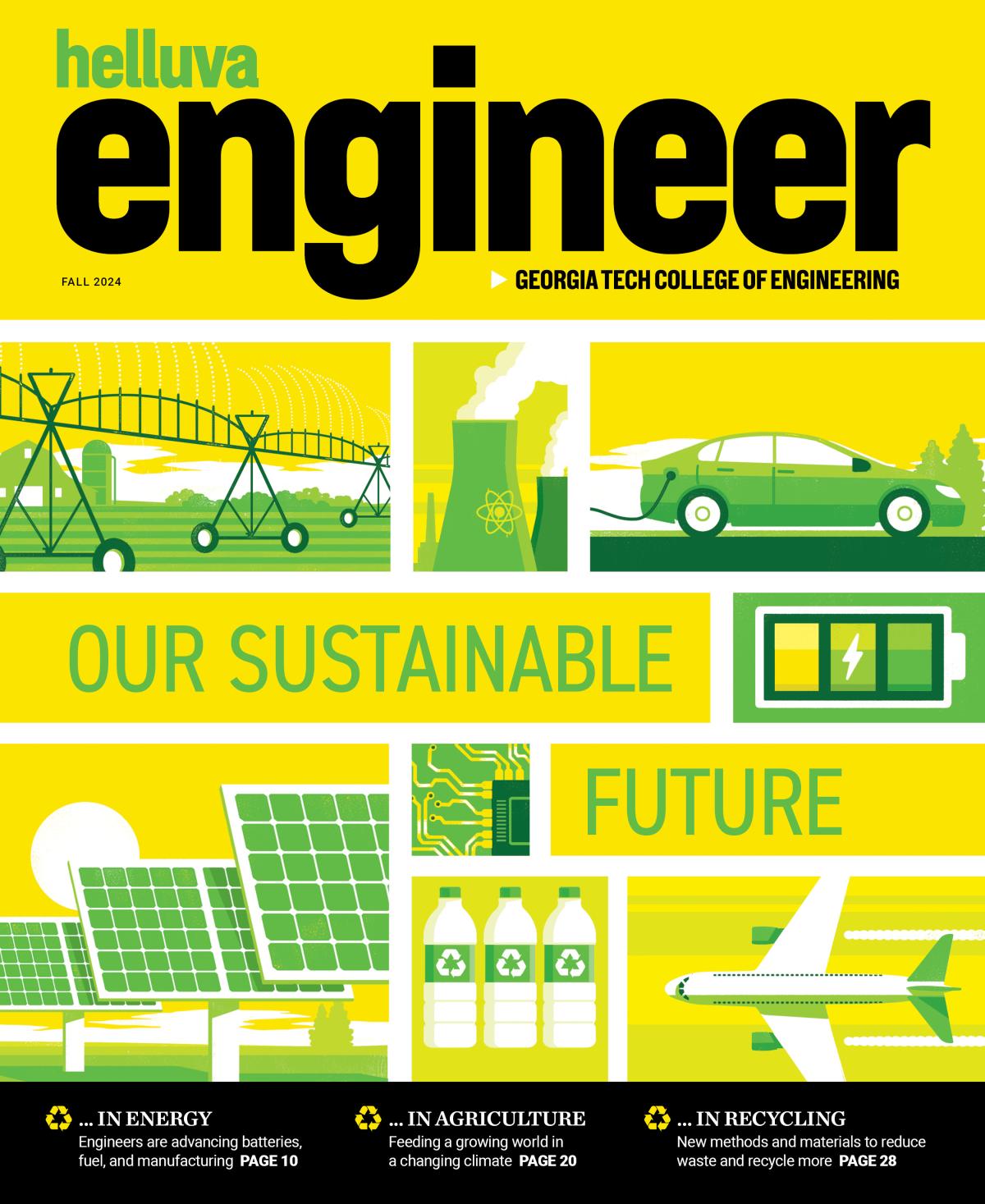
Helluva Engineer
This story originally appeared in the Fall 2024 issue of Helluva Engineer magazine.
In a world with more people, more energy needs, and more waste than ever, Georgia Tech engineers are hard at work developing the tools and technology for everyone to thrive. We’re diverting trash from landfills and taming plastic pollution (while finding alternatives to plastic in the first place). We’re reducing the environmental impact of agriculture and finding new ways to fertilize the fields growing food for a growing world. And engineers are powering up the batteries, fuels, and renewable sources to meet surging energy demand. The future is coming; we’re making it more sustainable.