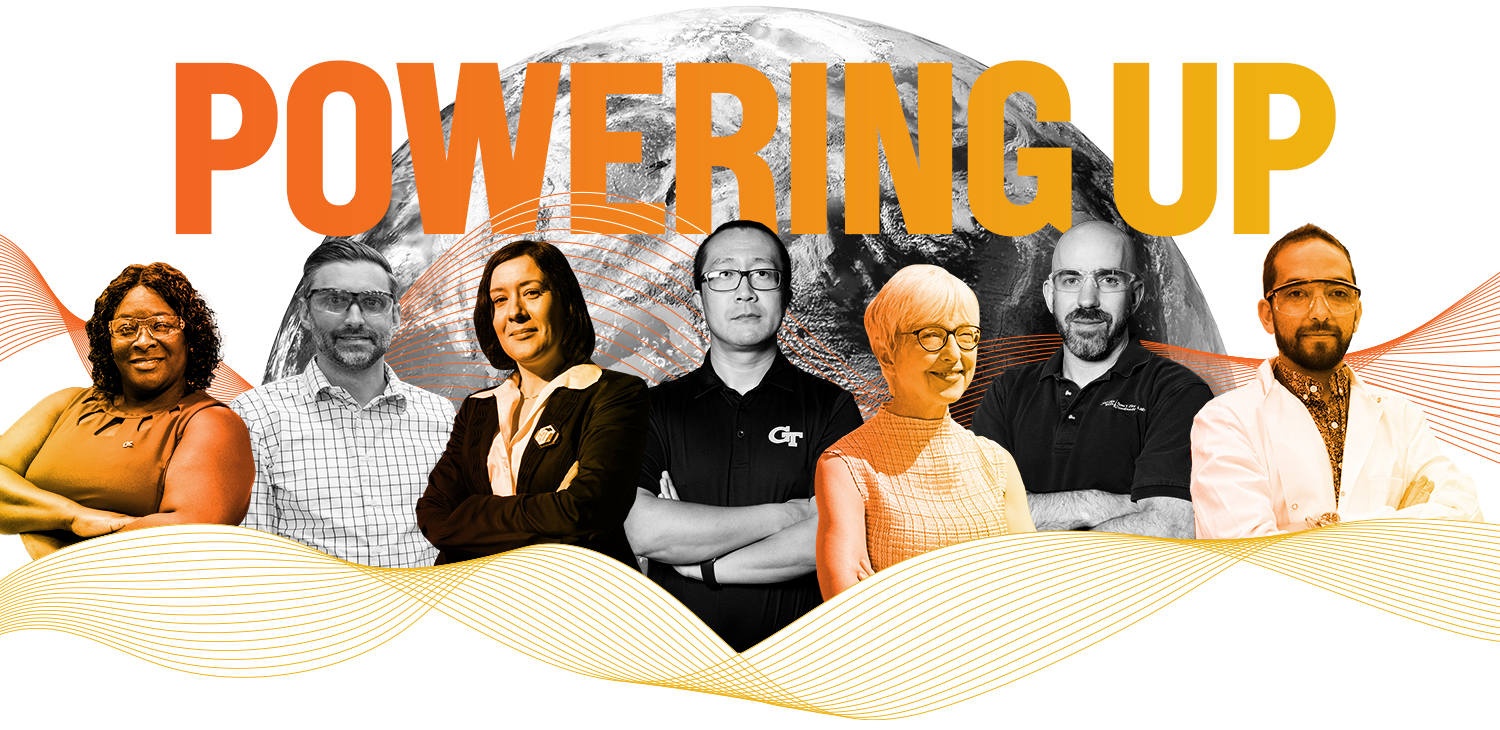
Our researchers are creating new technologies that pollute less and store more energy — while also ensuring the manufacturing process is clean.
(text and background only visible when logged in)
For 20 years, Georgia Tech’s Strategic Energy Institute (SEI) has brought together campus researchers who collectively develop better ways to meet the energy needs of today and tomorrow.
These days, that amounts to more than 1,000 people. Georgia Tech faculty are creating advanced communications and information systems, sensing and control approaches, and transmission and energy storage technologies that will make the nation’s power distribution systems more efficient and cost-effective. Their research also focuses on integrating renewable energy sources and electric vehicles.
“As the nation’s largest technologically focused university, Georgia Tech is playing an integral role in developing solutions that enable more equitable, lower cost, and cleaner generation, storage, distribution, and utilization of energy,” said Tim Lieuwen, Georgia Tech’s interim executive vice president for research. Lieuwen knows SEI better than anyone: he had been its executive director since 2012 until stepping in this summer as interim leader of Tech’s entire research enterprise.
“Georgia Tech researchers are not just helping to create cleaner, more efficient fuel options or mitigate the environmental impact of conventional energy supplies. They also are creating better performing, more economically viable energy options,” he said.
The work at SEI and across Georgia Tech has helped make the state of Georgia one of the nation’s leaders in clean energy, battery technology, and energy sustainability. It’s attracting numerous companies to invest in research and development in the state, including Hyundai, SK Battery America, and solar panel maker Qcells.
Lieuwen, himself a two-time mechanical engineering alumnus, is one of many engineering professors with an eye on energy sustainability. Some are finding new ways — and new materials — to improve batteries. Others are working on solar energy, nuclear power, and sustainable aviation fuels. And some are focused less on the final product and more on how to streamline manufacturing processes to increase sustainability.
They’re all driven by an ideal that Lieuwen said was born on campus about a decade ago and persists today.
“At Georgia Tech, we insist that it’s not enough to only create new energy technologies,” he said. “Our leadership has instilled a responsibility to also focus on how those technologies are created. By focusing on both the manufacturing process and the final product, we can create more sustainable materials at scale. And with our state as the petri dish, it allows Tech to help create green energy jobs that benefit all corners of Georgia.”
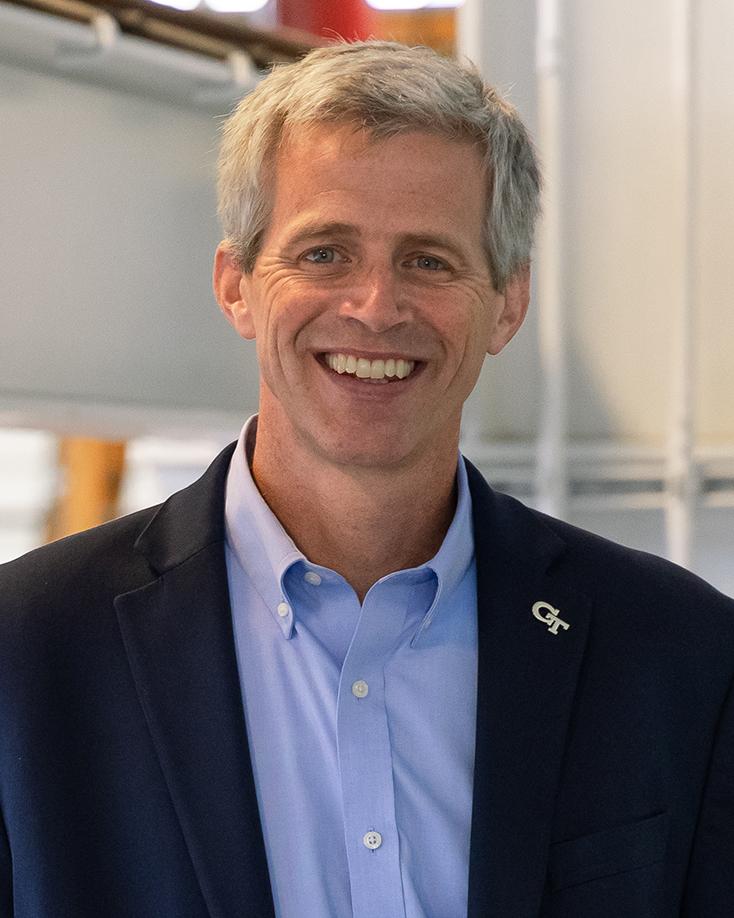
Tim Lieuwen (Photo: Chris McKenney)

Leading the Charge
Matt McDowell is transforming battery technology from the lab to the market
Matt McDowell is a matchmaker. As co-director of the Georgia Tech Advanced Battery Center, McDowell supports the state’s $30 billion investment in battery technology by connecting companies to Georgia Tech for research and development. He and co-director Gleb Yushin promote the campus’s unique facilities to foster relationships between Tech and global partners to create new battery technologies for electric vehicles, grid energy storage, electric aviation, and more.
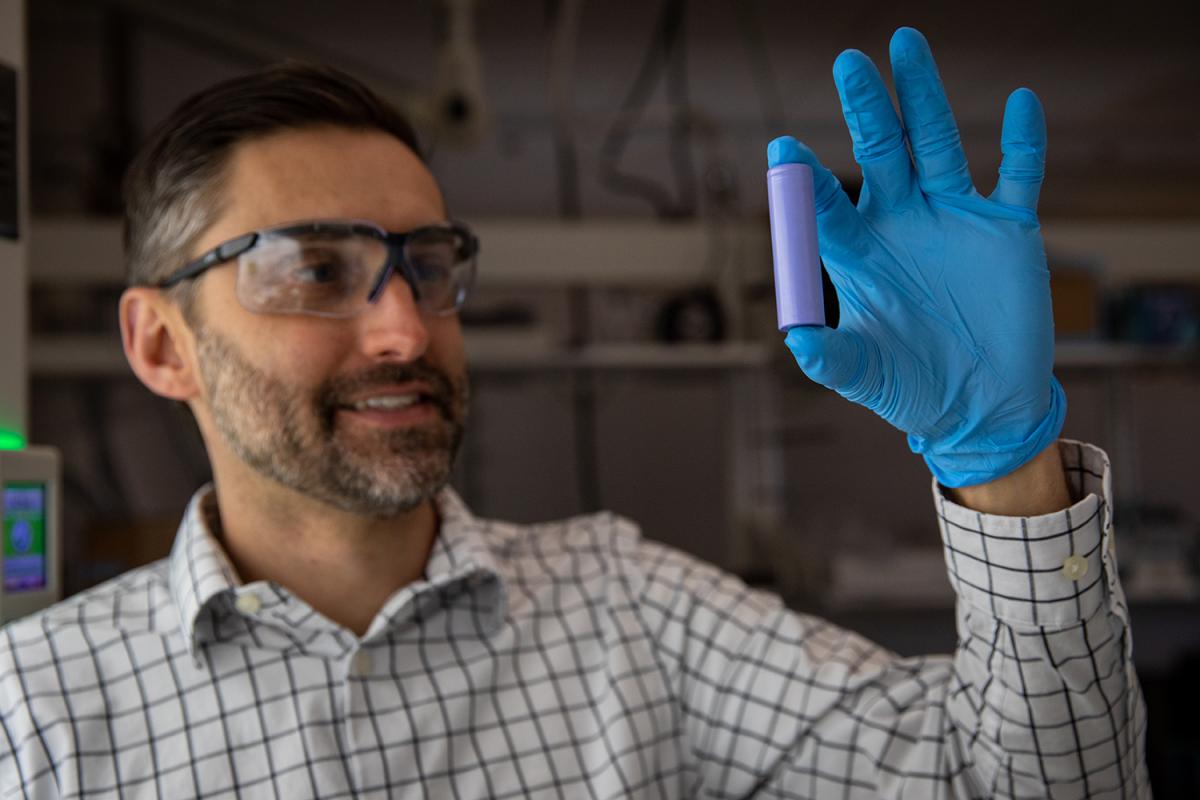
Matt McDowell’s research focuses on materials for next-generation batteries that are safer and more sustainable alternatives to lithium-ion batteries. (Photo: Ashley Ritchie)
Within his own lab in the George W. Woodruff School of Mechanical Engineering, McDowell focuses on reinventing batteries and other energy storage devices by researching how battery materials transform during use.
“Lithium-ion batteries, which are rechargeable and ubiquitous in computers and cell phones, won’t be replaced for a while, if ever,” said McDowell, Carter N. Paden, Jr. Distinguished Chair and associate professor. “However, there are a number of new technologies on the horizon. We’re looking for ways to create solid-state batteries that could be safer and potentially have even greater storage capacity.”
Lithium-ion batteries were commercialized in 1991. When they went into the first electric vehicles in 2008, they cost more than 10 times what they do today. The price continues to fall, and they are trending to soon be as inexpensive as an internal combustion engine.
One of the remaining problems, McDowell said, is safety. The liquid electrolytes they contain are flammable, making solid-state batteries a compelling alternative.
“Next-generation batteries require materials with higher charge storage capacity, or they require the development of new materials for entirely new battery systems beyond lithium-ion,” McDowell said. “For example, sodium-ion batteries have a lower density, could be cheaper to make, and could provide back-up power and renewable energy for the grid.”
Sodium is also more plentiful than lithium and more geographically friendly. Instead of mining in limited areas around the world for lithium, sodium is widely available, including by extraction from the oceans. Sodium-ion batteries also use hard carbon instead of graphite, the main component in lithium-ion batteries.
“Graphite is a great material, but most of it comes from overseas. Scientists can make it, but it takes a lot of energy and high temperatures. Sodium is more sustainable,” McDowell said.
McDowell sees a future — one that isn’t that far away — where electric vehicles are widely available, including at costs less than $30,000. The only way that happens is by bringing down the cost of batteries with new technologies. That’s the goal of the Advanced Battery Center. In addition to McDowell, Yushin, and approximately 20 other faculty members, the center represents battery R&D activities at Tech that includes 150 or so graduate students and postdoctoral researchers.
They’re already looking forward to the next step and deepening Georgia Tech’s impact on the state and nation.
“An important effort within the Advanced Battery Center is the creation and development of a new pilot-scale battery manufacturing laboratory facility on campus,” McDowell said. “This facility will enable translation of new energy storage innovations to commercial scales, and it will be a key resource for Georgia Tech and the broader region.”

Same Flight, Less Carbon
Researchers are creating and testing sustainable aviation fuels for cleaner travel
According to the International Energy Agency, aviation contributes 3% of all global carbon dioxide emissions. Although only a small portion of the world’s population currently travels by air, more people will travel as incomes grow: the industry expects passenger-miles to double by 2050. Facing this prospect of high and growing emissions, the international aviation industry has pledged to eliminate its carbon emissions by 2050.
The best bet to get there is rethinking what fuels are used in aviation. Instead of using petroleum, sustainable aviation fuels (SAFs) — or, more technically, low-carbon fuels — can be produced from a range of feedstocks, including agricultural residues, waste oils and fats, energy crops, and municipal waste.
Many airlines have signed agreements with SAF producers, and some of the fuel is in use. The U.S. Department of Energy reported that nearly 400,000 commercial flights have used SAFs at approximately 50 worldwide airports. Meanwhile, the U.S. Energy Information Administration projects daily production of 50,000 barrels of SAFs in 2025. That’s still a long way from meeting the need: U.S. jet fuel demand is expected to exceed 2 million barrels a day by 2050.
Even though engineers and scientists know how to make SAFs, there are reasons why it’s currently in such short supply. And those used today, aerospace engineering professor Adam Steinberg said, need to be blended with fossil fuels to fly safely.
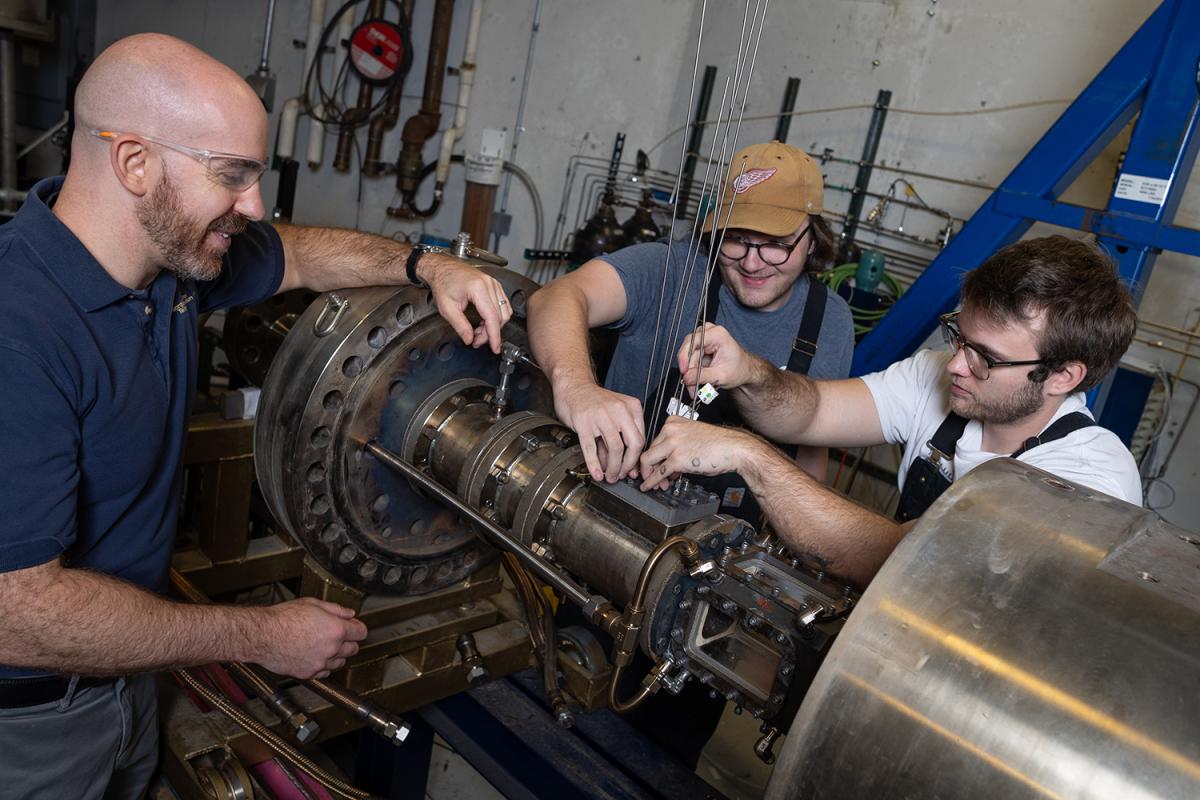
Adam Steinberg (left) works with students in the Ben T. Zinn Combustion Laboratory. (Photo: Candler Hobbs)
“So far, no commercial flights have used a 100% SAF. Other than test flights, today’s SAFs are only certified to fly when blended with at least 50% petroleum-based fuel,” said Steinberg, Pratt & Whitney Chair and professor in the Daniel Guggenheim School of Aerospace Engineering (AE). “SAFs don’t have the exact same chemical components as current jet fuel, which leads to unintended engine complications. A 100% SAF is currently too big a safety risk.”
Many of the engines in current airplanes were designed decades ago. Steinberg said those old machines rely on the makeup of petroleum-based fuels to function. For example, SAFs usually don’t contain the aromatic hydrocarbons molecules that are found in traditional fuels. Getting rid of aromatics may be good for sustainability, but they’re needed to swell seals in current engines.
“The engines leak if the fuel doesn’t contain aromatics. That’s one reason the industry is blending SAF with fossil fuel,” Steinberg said.
Addressing those issues is one of Steinberg’s goals as director of Georgia Tech’s Ben T. Zinn Combustion Laboratory. It’s among the world’s largest academic combustion research facilities. The Zinn Lab allows Steinberg and other researchers to test fuels and their impacts on engines.
“As we design better engines, the machines become more complicated. And that could reveal sensitivities not seen in simpler engines,” Steinberg said. “For instance, if you change to SAFs and the engine goes out at 30,000 feet, does the difference in fuel properties make it harder or easier to relight the engine?”
Wenting Sun also works in the lab. The AE associate professor oversees a Federal Aviation Administration (FAA)-funded project simulating engine conditions and modeling combustion to measure emissions and see what is produced at engine-relevant high temperature and pressure conditions.
“We investigate the combustion processes of both conventional jet fuel and SAFs and compare their differences. Then we examine what we can modify to minimize emissions from both fuels,” Sun said. “This past April, the FAA released a final rule to regulate particle emissions. Our research will likely inform policymakers regarding regulations on future engines and fuels.”
Sun’s goal is to burn fuels as cleanly as possible. One of his favorite ways to explain clean burning is comparing a candle to a natural-gas stove. The smoke coming off a candle flame is the emission, and the orange color is proof that many particles are present. A stove’s flame is blue, which means it’s cleaner and nearly free of particles.
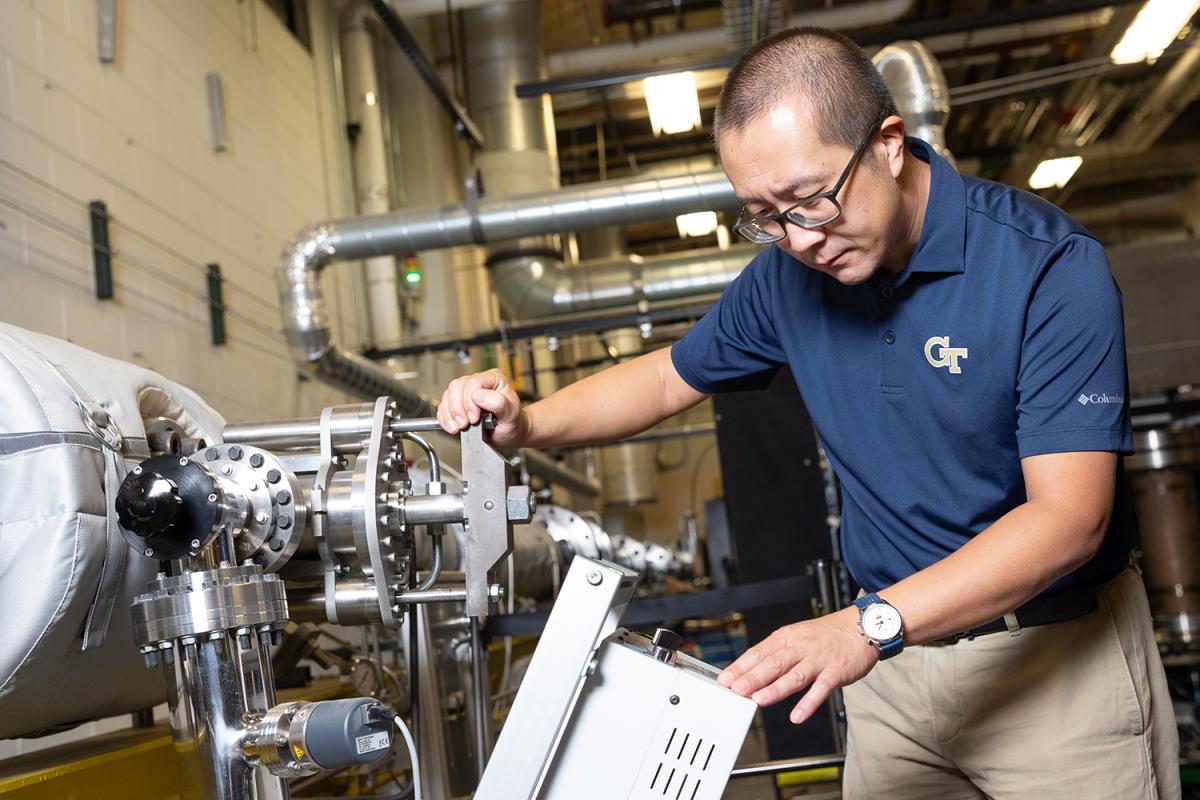
Wenting Sun works in the Zinn Combustion Lab. (Photo: Candler Hobbs)
“Our goal is to develop technologies that increase efficiency and simultaneously decrease emissions of sustainable aviation fuels,” Sun said.
Work at Georgia Tech on SAFs extends beyond aerospace engineers. Industrial engineer Valerie Thomas performs environmental lifecycle assessments of low-carbon transportation fuels, including those for aviation. She’s nationally recognized in the field and recently chaired a National Academies of Sciences, Engineering, and Medicine committee that authored a report on the topic.
Thomas has studied fuels made from blue-green algae and explored if carbon dioxide can be captured from the air and converted into fuels.
“I think we really can stop using fossil fuels, find ways of living our lives, and run the economy without emitting greenhouse gases,” said Thomas, Anderson-Interface Chair of Natural Systems and professor in the H. Milton Stewart School of Industrial and Systems Engineering. “It’s a big challenge, but it’s not one of these impossible things.”
Our goal is to develop technologies that increase efficiency and simultaneously decrease emissions of sustainable aviation fuels.
WENTING SUN
Thomas worked on ethanol and other fuels for many years. She became interested in aviation fuels when she realized that cars and trucks can transition to electric or fuel cell systems and don’t really need biofuels.
“The options for aviation are more constrained. Not only are biofuels the most viable option for decarbonizing aviation, the amount of biofuel that U.S. aviation would need is basically all the biofuel our nation can sustainably produce,” Thomas said.
Just as she’s convinced eliminating greenhouse gases is possible, she sees a future where the aviation industry stops using petroleum-based fuel. But that shift will require work beyond the technological limitations Steinberg is working through. Thomas pointed to political and economic hurdles, too.
For starters, although the government has enacted regulations and financial incentives to help decrease sales of vehicles that burn fossil fuel, neither exist for aviation.
“Gas prices also are cheaper now than they were about a decade ago, so that has slowed the appetite for companies to invest in something that isn’t as affordable,” Thomas said.
In the meantime, Thomas stressed that engineers and scientists need to put more focus on the methods they use to evaluate emissions. Specifically, she said more needs to be learned about how new and future fuels decrease — or increase — emissions. According to Thomas, Georgia Tech can lead in that direction because it’s a “can-do” place.
“When I suggest something here on campus, people are likely to say ‘Yeah, let’s go do that,’” she said. “That’s true even if my idea isn’t completely formed. We just go and try it out and put it together. Those are the things, along with our facilities and the vision of our leadership, that make Georgia Tech and the future of low-carbon fuels a really good combination.”

Harnessing the Sun
Juan-Pablo Correa-Baena’s journey to sustainable solar energy brought him from Colombia to campus
As a child in Colombia, Juan-Pablo Correa-Baena would look at the sky and think about how things could be different.
“Fossil fuels dominate Colombia’s energy production landscape even though renewables are readily available,” said Correa-Baena, associate professor and Goizueta Junior Faculty Chair in the School of Materials Science and Engineering. “My home country is a large producer of oil but also boasts a huge potential for solar energy production. I grew up wondering why Colombia didn’t make that switch.”
It wasn’t until college that Correa-Baena was able to put his curiosity into action. After earning his undergraduate degree in mechanical engineering with a minor in environmental engineering, he focused on solar technology while pursuing his Ph.D.
He now leads a solar energy materials research initiative for Georgia Tech’s Institute of Matter and Systems and Strategic Energy Institute.
“I want to ensure that all countries around the world have access to solar energy by helping lower deployment costs,” Correa-Baena said.
His research focuses on the development of new materials for low-cost semiconductors used for optical and electronic applications. Correa-Baena’s team also works on advanced techniques for characterizing these very small materials and their interactions. He was awarded a highly competitive Sloan Research Fellowship in 2024 to support these efforts.
The award came shortly after his recent study that unraveled the mechanism that causes degradation of a promising new material for solar cells — and how to stop it using a thin layer of molecules that repel water. His lab’s findings are the first step in solving one of the key limitations of metal halide perovskites, a new material used to absorb light. They are already as efficient as the best silicon-based solar cells at capturing light and converting it into electricity.
The field’s next challenge, Correa-Baena said, is to better incorporate solar energy into the nation’s electrical grid.
“Now that solar is as affordable as oil, the U.S. must be more proactive in finding ways to transport and store it,” Correa-Baena said. “The government often has been very reactive at this. ‘It’s cheap! Let’s deploy it. Oh wait, how do we connect it?’ The Inflation Reduction Act is a great proactive step that is shaping the future of solar energy deployment.”
He’s also encouraged by Georgia’s investment in solar power and investments made by solar companies Qcells and Silicon Ranch, among others. And yet, just as he looked up as a child in Colombia, he sees the opportunities for more when he looks down as an adult.
“Whenever I fly in and out of Atlanta, I see a lot of roofs with nothing on them. Georgia gets so much sunlight, and those businesses, warehouses, and homes are prime spots for solar panels,” he said. “Things are going well for deployment, especially with solar farms. But we must push for more consumer activism and talk to our politicians about paying closer attention to where this technology can be further deployed.”
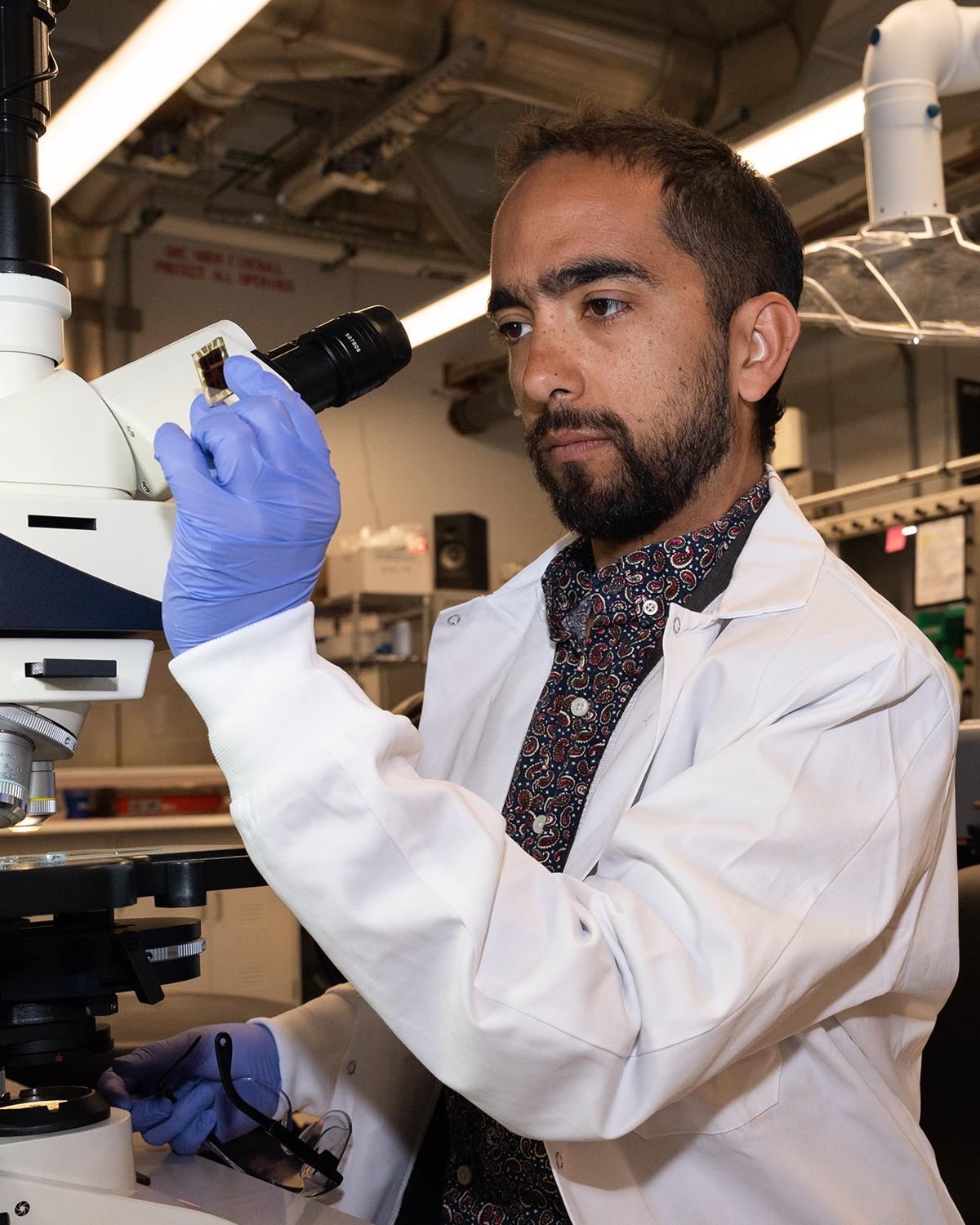
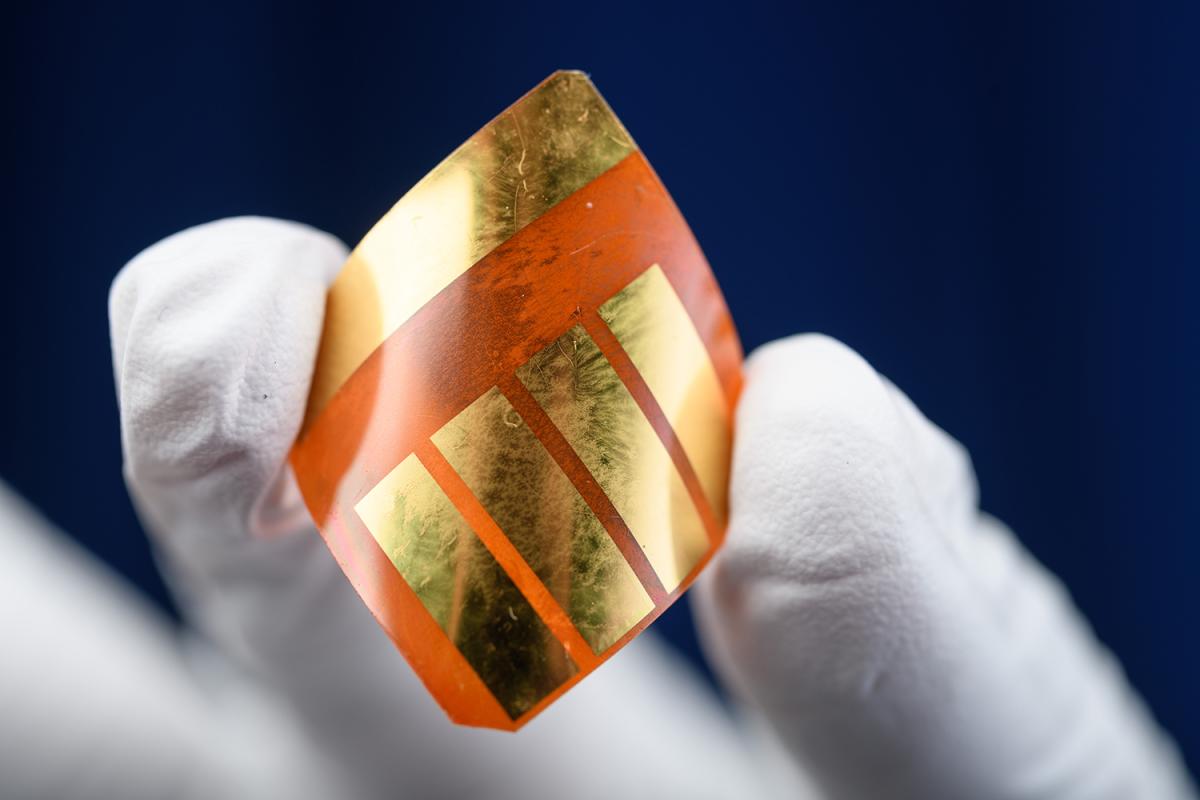
Top: Juan-Pablo Correa-Baena
Above: A flexible, lightweight solar cell made from perovskites, a material that could produce energy from sunlight more cheaply and efficiently. (Photos: Joya Chapman)

Nuclear Power and Net Zero
From Chernobyl clippings to the Woodruff School, Anna Erickson advocates for nuclear energy’s safety and strength
Her mom asked her to stop — repeatedly — but Anna Erickson kept on going. She was just 5 years old, yet Erickson would gather newspaper clippings about the Chernobyl nuclear disaster and read them to her younger sister again and again.
Her mother worried it would scare the baby. But that fascination set the groundwork for Erickson’s lifetime of interest in nuclear energy.
Decades later, Erickson is one of the nation’s most prominent researchers in nuclear power security, safeguards, and sustainability. Nearly every casual conversation about her job inevitably turns to the notorious nuclear disasters at Chernobyl, Three Mile Island, or Fukushima. But just as she was determined long ago to keep reading to her sister, she’s similarly focused now on telling people that nuclear energy is safe — and necessary for the future.
“Nuclear has the best safety record among traditional energy sources,” said Erickson, Woodruff Professor in the George W. Woodruff School of Mechanical Engineering. “Spent fuel, or what some call nuclear waste, lasts a long time. But we know how to handle and store it. Importantly, spent fuel can be recycled into additional energy sources for reactors using isotope separation techniques. Nuclear disasters are incredibly rare. And human health is much more negatively impacted by emissions from coal and fossil fuels.”
The dangers are minimal, Erickson said, and the benefits of nuclear power are unmistakable. She noted that nuclear plants produce maximum power about 93% of the time. Their output isn’t affected by weather, supply and demand, or financial markets.
For comparison, geothermal offers maximum power three-fourths of the time, natural gas 57%, and hydroelectric systems half the time. Coal produces max electric just 40% of the time.
Future electricity needs for everything will only increase. Nuclear shouldn’t be, and can’t be, the only source of power. But it definitely needs to supplement other carbon-free, sustainable sources.
ANNA ERICKSON
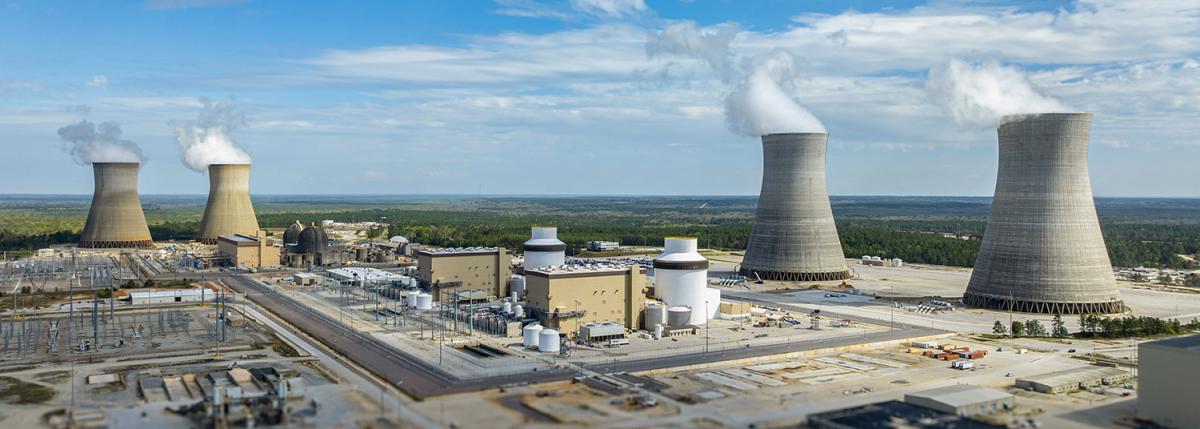
Units 3 and 4 of Georgia Power Company’s Plant Vogtle were the first newly constructed nuclear units in more than 30 years. (Photo courtesy: Georgia Power Company)
Erickson said nuclear energy will be even more imperative in the years to come: more data centers and artificial intelligence will need substantial energy supplies all day, every day. Data centers currently represent about 4% of electricity demand, but Erickson said the number is expected to more than double by 2030. It’s why Microsoft recently announced an agreement to reopen a nuclear unit at Pennsylvania’s Three Mile Island and purchase all of the plant’s electricity.
“Americans aren’t good at consuming less, so future electricity needs for everything will only increase,” Erickson said. “Nuclear shouldn’t be, and can’t be, the only source of power. But it definitely needs to supplement other carbon-free, sustainable sources.”
To get there, Erickson suggested three strategies.
One: build more nuclear plants. When the third and fourth units began operating within the past year at Southern Company’s Plant Vogtle in Waynesboro, Georgia, they were the first newly constructed nuclear units in the U.S. in more than 30 years. They’re among 94 currently in operation around the country. However, to achieve America’s goal of net-zero carbon emissions from power plants by 2050, the nation will need to triple the output of nuclear power and add 200 more nuclear reactors.
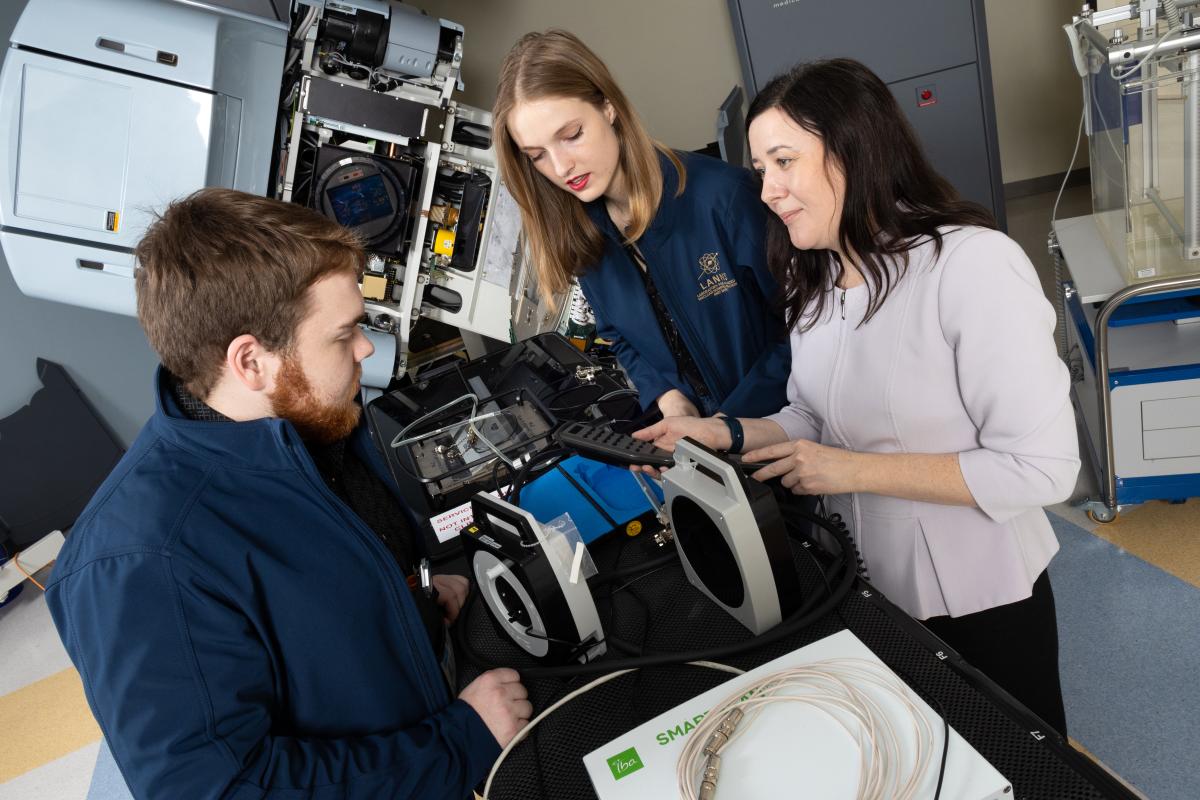
Anna Erickson (right) works with Ph.D. students Natalie Cannon (center) and Alex England in her Laboratory for Advanced Nuclear Nonproliferation and Safety. (Photo: Candler Hobbs)
“Vogtle cost about $36 billion, so it’s not possible to build 200 more at that cost,” Erickson said. “Fortunately, we don’t have to, because we learned so much as Vogtle was ramping up about supply chains and how plants could be built at scale.”
She said a cheaper, faster approach for bringing additional nuclear power to the grid would be reopening decommissioned reactors and extending their operating licenses well into the future. This is her second strategy. Michigan’s Palisades Nuclear Plant near Grand Rapids recently secured a $1.5 billion loan from the Department of Energy with plans to reopen in 2025. It would be the first shut down U.S. nuclear reactor to be revived.
Erickson’s third strategy is to continue pursuing advanced nuclear power, including fusion technologies — something she admitted has been promised “in about 30 years” for decades. She said fusion is closer now than ever before and perhaps about 15 years from viability because of federal and private equity support. Multiple advanced fission reactors also are being designed by a number of national laboratories and private companies, promising additional diversity in nuclear energy generation.
Erickson is encouraged about nuclear power’s future partially because public opinion has shifted. A 2023 Gallup poll found that support among Americans for nuclear power is at its highest point in more than a decade. Part of her job will be continuing to address misconceptions about the technology and advocating for its increased role in sustainability.
“We’ve been creating nuclear power for more than 70 years. If all its waste were stored at the same place, it would only cover one football field, 10 feet deep,” Erickson said.
“We need to diversify to meet the nation’s carbon zero goals. And nuclear is a clear path to making it happen.”

Sustainability on a Roll
Tequila Harris’ roll-to-roll manufacturing techniques mean fewer steps and less waste when making renewable materials
Sustainability is a cornerstone of Tequila Harris’ lab, where she works on coating science and technology for clean water applications, renewable materials, and advanced roll-to-roll manufacturing processes.
A key focus is decreasing the number of steps needed to fabricate thin and thick film technologies used in these areas.
“Fewer manufacturing steps translates to less energy and water requirements, making the manufacturing methods more sustainable,” said Harris, professor in the Woodruff School. “When you consider material scalability, fewer steps when fabricating billions of parts can have a significant impact.”
Harris’ lab explores how the manufacture and design of films, components, and systems affect both their functionality and their life expectancy. From that, she can determine process, structure, and property relationships to enhance performance.
In short, she looks to fabricate materials developed by chemical engineers, material scientists, and chemists, quickly, cheaply, and effectively.
“Our lab determines what systems, strategies, and tooling can be used to process things faster while maintaining the same, or better, performance,” Harris said.
Harris’ go-to tooling and manufacturing system combination for the last 18 years has been a slot die coating on a roll-to-roll facility. It’s one of the fastest growing technologies for scaling thin film materials. She produces thin films, coated on a wide variety of substrates, that can be housed in large rolls for later use. When creating the materials at scale, Harris takes great care to detect and correct defects to minimize waste and increase the amount of usable material.
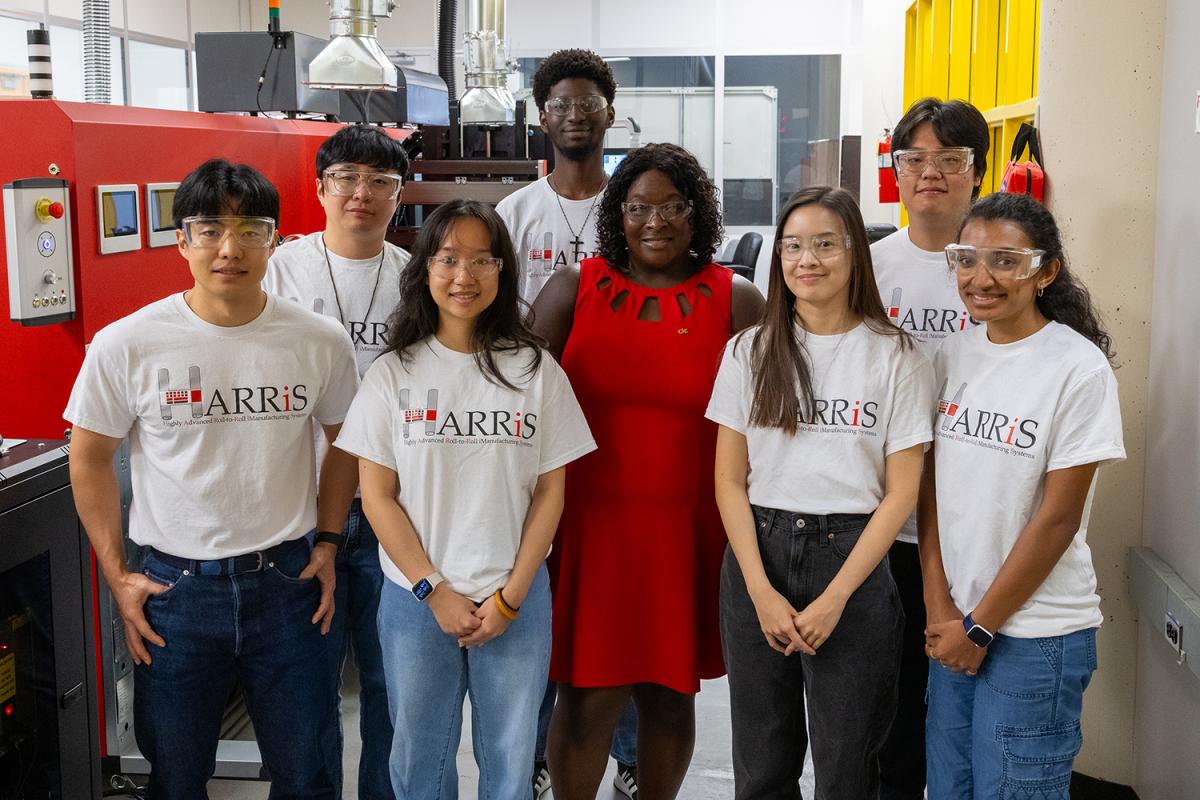
Tequila Harris (center) with members of her Highly Advanced Roll-to-Roll iManufacturing Systems (HARRiS) lab group in the new roll-to-roll manufacturing facility. (Photo: Chris McKenney)
That relentless focus on eliminating waste is why the mantra in her Highly Advanced Roll-to-Roll iManufacturing Systems (HARRiS) group is “No gaps, no scrap.”
That work received a boost this fall. Harris opened a new modular, pilot scale roll-to-roll facility to advance thin film research and development beyond the lab. The facility is open for a large variety of materials that Harris’ group can use across a plethora of different technologies.
“Using our new modular, pilot scale roll-to-roll manufacturing facility, we can analyze film fabrication at speeds a thousand times faster than what has been realized at the laboratory scale,” Harris said. “Instead of creating material at one-tenth or three-tenths of a meter per minute, we process materials at coating speeds up to 200 meters per minute, using flexo, gravure, or inkjet printing in addition to slot die coating at the pilot scale.”
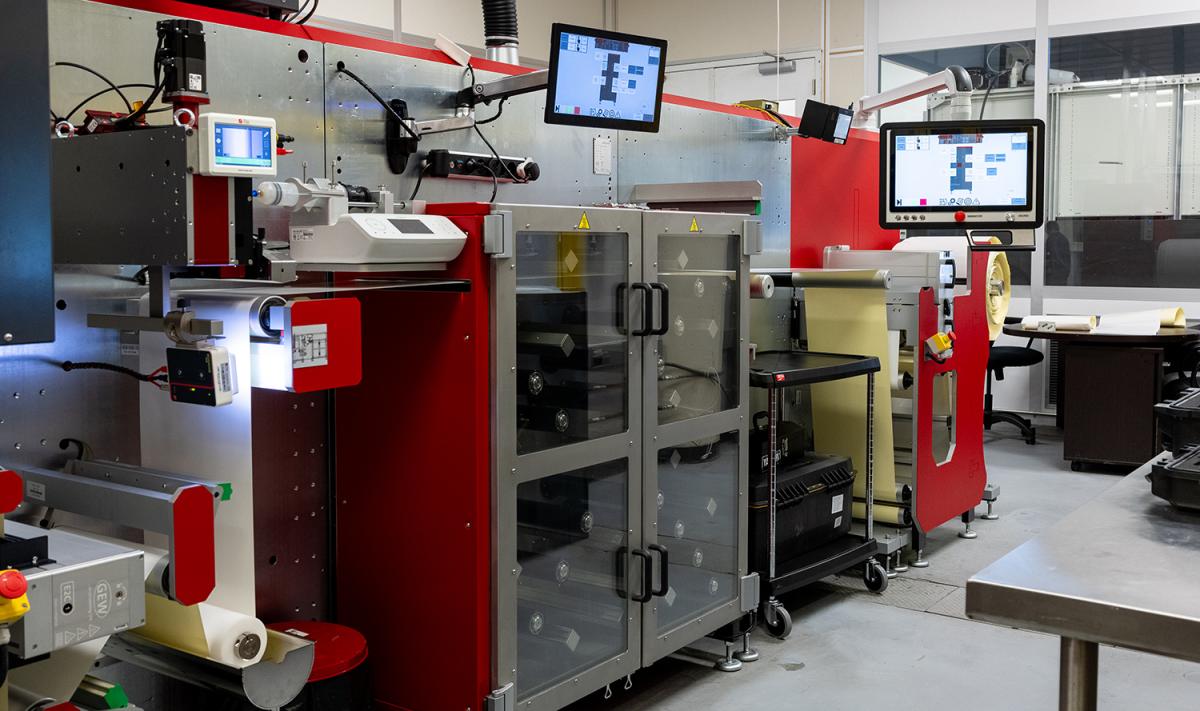
The Modular Pilot Scale Roll-to-Roll Manufacturing Facility will serve as a test bed for scaling up manufacturing research. It’s open to Georgia Tech researchers and academic, government, and industry partners. (Photo: Chris McKenney)
The HARRiS lab works with academic, government, and industrial users, all with the goal of building an ecosystem around scalable manufacturing for a broad collection of materials. On campus, Harris works with Sankar Nair in the School of Chemical and Biomolecular Engineering (ChBE) on new membrane materials for papermaking. With ChBE’s Carson Meredith and Meisha Shofner in MSE, Harris’ lab is collaborating on renewable food packaging. She is planning for a future partnership with McDowell on his battery technologies.
Her focus on improving products and materials comes, in part, Harris said, from a childhood where she was exposed to a combination of a small farm-to-table lifestyle and industrial factories in neighboring towns where many people in her community worked.
“I preferred improving and making products to farming,” she said. “In graduate school, I studied manufacturing and design of machine tools. When I began my career at Georgia Tech, my focus shifted from solely coating technology to the integration of coating science. This has led to the design and implementation of innovative manufacturing approaches with an understanding of the entire coating process and the quality and performance of the resulting materials.”
(text and background only visible when logged in)
(text and background only visible when logged in)
Related Stories
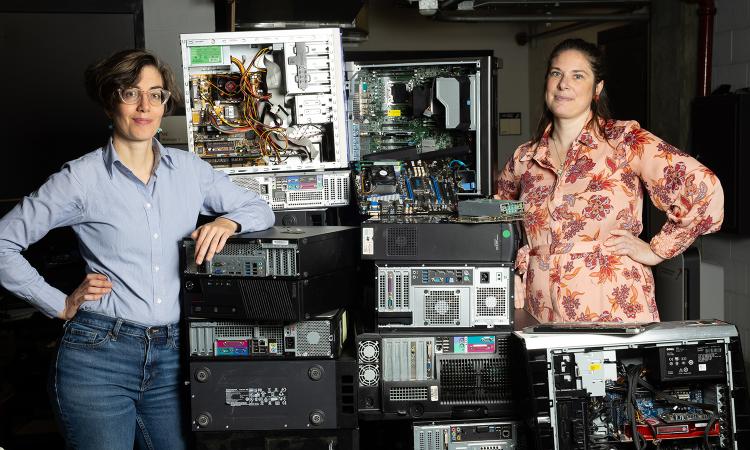
To Hell with Garbage
In the quest to reduce, reuse, and recycle, Georgia Tech engineers are at work on ways to divert more trash from landfills, tame plastic pollution, and cut waste from electronics.
(text and background only visible when logged in)
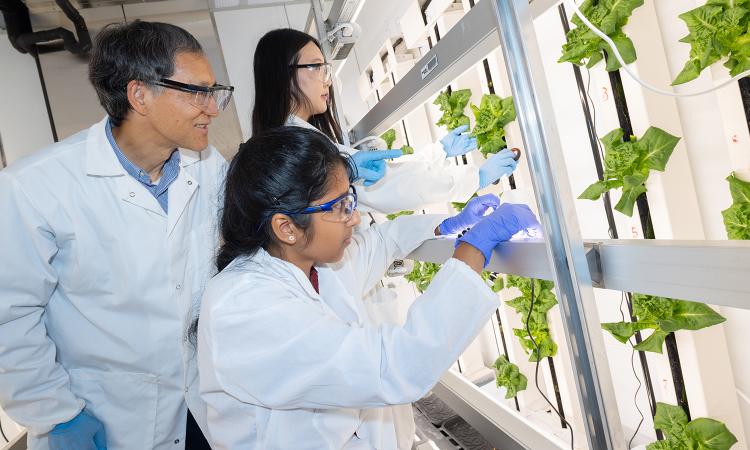
Planting the Seeds of the Farm of the Future
Georgia Tech engineers are working to reduce the environmental impact of farming while creating technologies to help farmers feed a growing world and adapt to a changing climate.
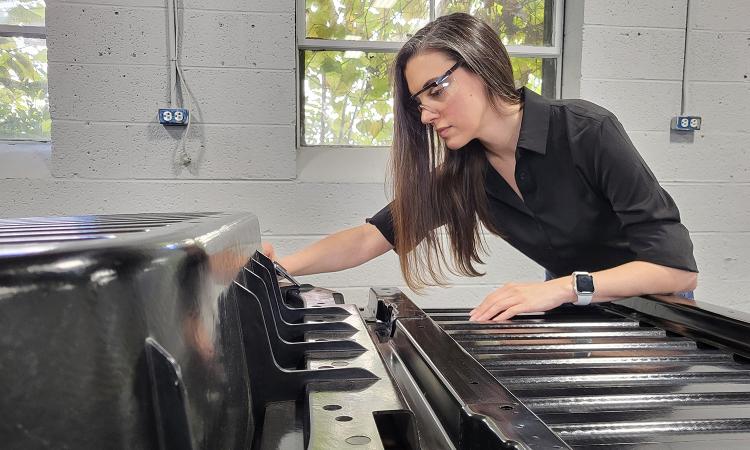
Driving Change
Alumna Amanda Nummy is helping move the automotive industry toward more sustainability, from the materials used in vehicles to recycling cars and trucks after they come off the road.
(text and background only visible when logged in)
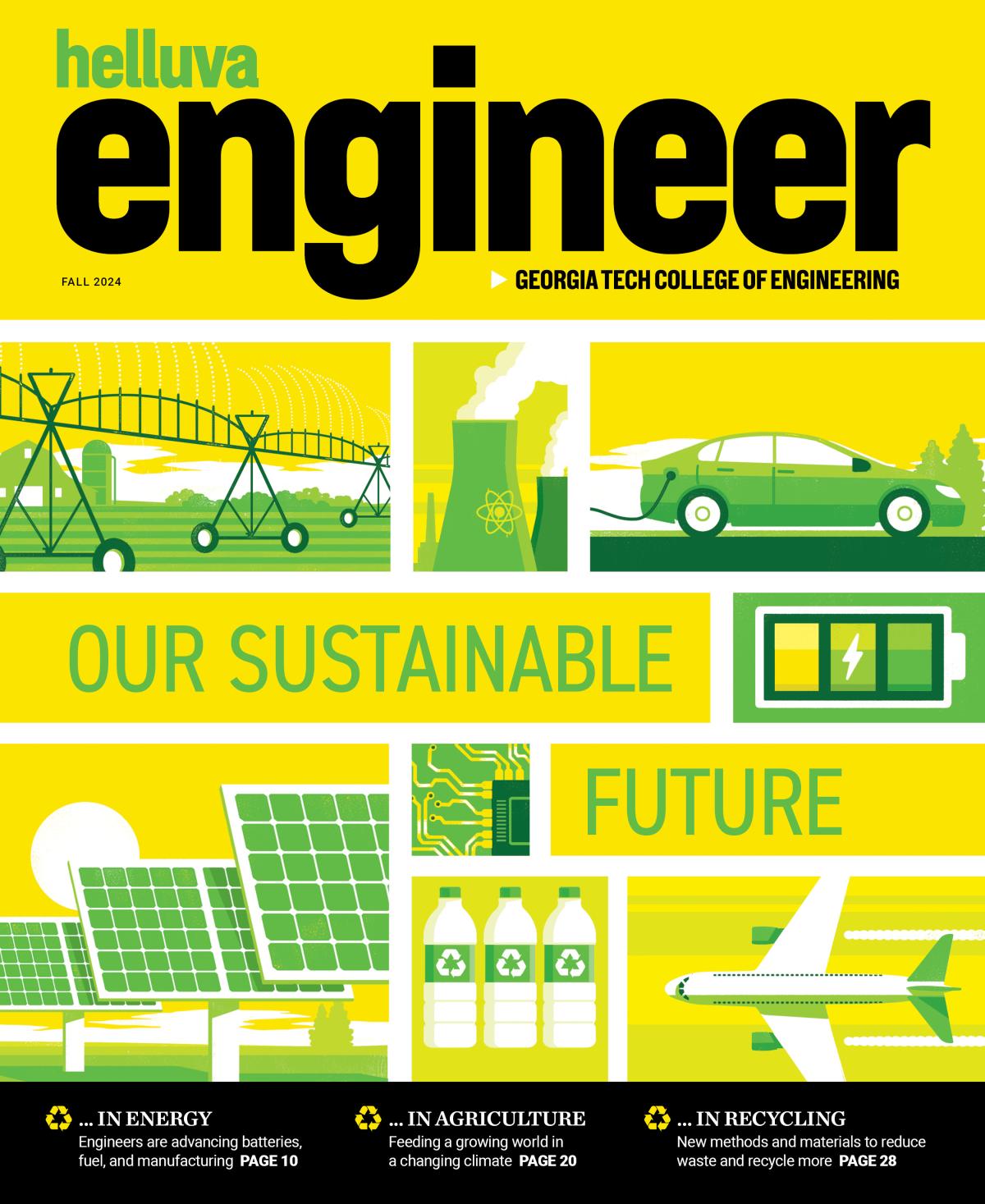
Helluva Engineer
This story originally appeared in the Fall 2024 issue of Helluva Engineer magazine.
In a world with more people, more energy needs, and more waste than ever, Georgia Tech engineers are hard at work developing the tools and technology for everyone to thrive. We’re diverting trash from landfills and taming plastic pollution (while finding alternatives to plastic in the first place). We're reducing the environmental impact of agriculture and finding new ways to fertilize the fields growing food for a growing world. And engineers are powering up the batteries, fuels, and renewable sources to meet surging energy demand. The future is coming; we're making it more sustainable.